DIY Saw Horse Plans and Ideas (Homemade Designs). Simple saw horses
DIY Saw Horse Plans and Ideas (Homemade Designs)
If you buy something through our posts, we may get a small commission. Read more here.
A sawhorse is a handy structure for supporting wood projects and items’ weight in a workshop. Considering how costly and bulky some of them are, it’s best to construct one with a good DIY plan. Unfortunately, some plans are complex for beginners to comprehend.
This post contains various DIY sawhorse plans recommended by our pro woodworkers to construct a robust structure.
Inexpensive Sawhorse Plans
As the name suggests, these saw plans minimize the costs of building a reliable saw horse without compromise. They contain a limited number of materials for a design with detachable legs.
With detachable legs, not only is storage easier, but it will save some space in your workshop. You can neatly fold the design and hang it on the wall when not in use. The instructions are straightforward too. Therefore, no one will find it complicated to build with the plans.
Cheap, Improved Sawhorses
Sawhorses help to keep your tools and materials off the ground. However, the vast majority are expensive and flimsy. Cheap, Improved Sawhorses will help you to construct a durable structure without spending a fortune. All you need to carry out this construction is some scrap wood and screws.
The good thing about this plan is it’s easy to set up and work with. You can build the sawhorse quickly once you have all the tools and materials down.
Beginner Sawhorse Plans
Beginner Sawhorse Plans are some of the best homemade plans to follow for beginners. The design is comprehendible, making it possible for woodworkers to cut, measure, and build. Unlike the inexpensive DIY plans, the structure after construction isn’t foldable.
The advantage here is the rigidness can support heavier items than most foldable designs. over, the sawhorse will have shelves for extra storage. These plans will be perfect if you are not concerned about saving space in your workshop.
Heavy-duty Sawhorse Plans
These plans will build a pair of heavy-duty sawhorses, durable enough to bear the weight of bulky items. Heavy-duty sawhorse plans allow you to create matching dovetail grooves along the perimeters of the sawhorses to prevent shifting and enable the user to secure material to the structure.
The sawhorse plans feature simple layouts and several instructional videos that are comprehensible. They show how to cut and construct specific parts of the structure to attain perfection.
(But if you want to layout your project yourself, here’s a complete guide on how to draw woodworking plans to make the final product as good and accurate as possible.)
How To Build A Folding Sawhorse – Quick and Easy
For the amateur or the professional woodworker, a good pair of sawhorses is an essential element to any project. See our full review of the best sawhorse to buy. Steve Ramsey of Woodworking For Mere Mortals takes the simple task of making your own sawhorses one step further.
The only real problem with basic sawhorses is they take up a lot of room in your shop or garage. This simple folding sawhorse design from Steve is very easy, quick, and will solve the storage problem basic sawhorses cause.
The best part, you only need two 2x4x8’s to build each sawhorse (not including the shelf).
What You’ll Need
- 2. 2x4x8’s
- 1. 1/2 inch 4×4 Sheet of Plywood
- 2 1/2 inch Screws
- 2. 3 inch Strap Hinges (with screws)
- 4. 2 inch x 1/2 inch Dowels
- Cordless Drill
- Miter Saw or Table Saw
- Band Saw or Jigsaw
- Wood Glue
Cut The 2x4x8’s
Like I said earlier, you only need two 2x4x8’s for each sawhorse. The best way to start is to cut all of your base material in the beginning.
Sawhorse Base
2x4x8 number one. cut into 3 equal lengths at 31.5 inches.
2x4x8 number two. cut one piece at 31.5 inches, and one piece at 48 inches.
The Shelf
The remaining section of 2x4x8 number two will need to be cut into four strips at 3/4 inches wide x 15 inches long. Or, if you don’t want to go through the trouble of cutting a 2×4 into strips, just purchase a 1×2 strip and cut to length.
The shelf should be a 1/2 inch plywood rectangle at 13.5 inches x 27.5 inches.
Click here to view the cut list and full plans for this sawhorse.
Cut 19 Degree Angles
Using a table saw or miter saw, cut the ends of each 31.5 inch board at a 19 degree angle. The angles should be parallel on each board.
Mike Makes Sawhorses | DIRESTA vs. Matthias Wandel Design!
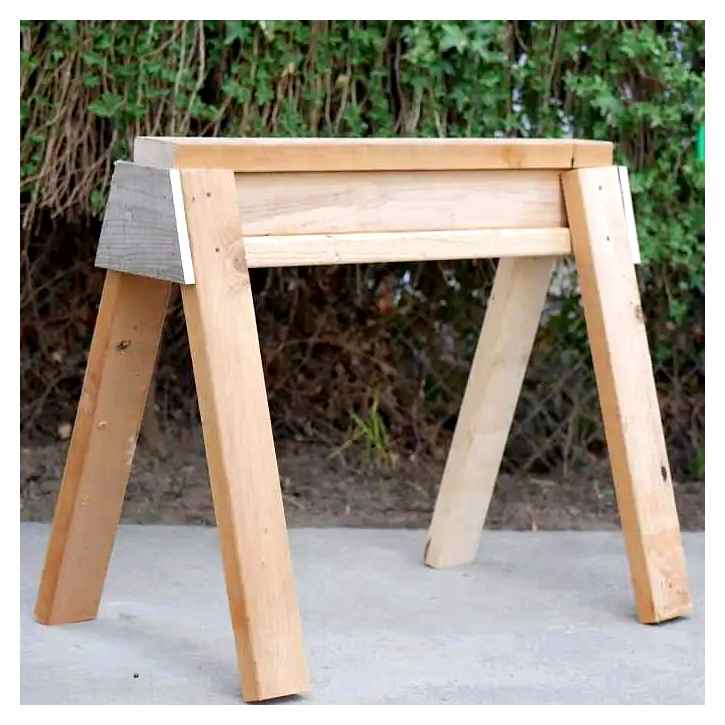
Make sure you are not changing the overall length of each board.
As shown in the picture below, you can save a bit of time by setting your saw at 19 degrees when cutting the boards in described in step one.
Drill Holes
Drill holes on one end of each 31.5 inch leg to connect the leg to the top of the sawhorse. Simply ensure you are using the correct bit for the size screw you will use.
On that same note, be sure to use a screw long enough to penetrate both boards, but not long enough to drill all the way through the top board.
For one, I don’t work for Kreg, nor do they pay me to endorse their products. However, if you don’t have one of their Kreg Jigs, you are missing out. If you need to make a hole, this is the tool for you.
Watch this quick video below to learn more.
Pre Drill and Secure 3 Inch Strap Hinges
Using a straight edge, draw a straight line 4 inches from each edge of the 48 inch brace board to mark where the sawhorse legs will be attached.
Center your leg on the top board and, using your strap hinge, pre drill the holes where the hinge will be attached to the leg and brace board.
Attach the hinge to the leg, and attach the leg using the appropriately sized screws (2 1/2 inch) to the top board.
Note: You are only attaching the leg so you can accurately mark the hinge holes on the other leg.
You are probably thinking, “how am I supposed to fit a pencil in between the boards to mark the holes?” Well, all you need to do is cut a pencil down to about 2 inches and there you go. It’s also a good idea to have a few stubby pencils laying around for this purpose.
Unscrew the legs from the top brace board. Next, pre drill the holes you marked, and attach the hinge.
Mark A Line Halfway Down Each Leg
Now you should have your legs ready to modify for the shelf. Using a straight edge, mark a line halfway down the sawhorse legs. This is where you will drill the holes for the dowels that will hold up the shelf brackets.
Note: If you don’t need a shelf, skip to step 8.
Drill Holes For Dowel Rods
Drill a 1/2 inch hole in the center of each line on your legs. Just remember, if you are using a different sized dowel rod, you have to adjust the size of the hole. For instance, if I am using 3/4 inch dowels, I need to drill a 3/4 inch hole.
Note: Steve Ramsey has a nice drill press to help with this step, but you can drill the holes with a cordless drill as well.
Attach Dowel Rods
As always, add a generous amount of wood glue to each hole before hammering in the dowel rods.
Place the dowel rods in each hole and lightly tap until all dowels are approximately the same length. Wipe off any excess glue.
Secure Legs Onto Top Sawhorse Brace
You probably already feel like you’ve done this, and you are right. Now, just repeat the steps and attach the legs to the top brace.
This sawhorse is sturdy enough at this point, but adding the shelf only increases the strength and sturdiness.
Drill Holes, Notch, And Attach Shelf Brackets
Using the sawhorse legs as a guide, hold your 15 inch strips against the center line on the legs, and mark where you will drill each hole to attach onto the dowel rods.
On one of the holes on each board, notch out a hole so it can be lifted off the dowel rod.
Note: Steve uses a Band saw to make his notch, but a jigsaw, or most other saws will work if you are careful.
Secure Plywood Shelf
Secure your 13.5 inch x 27.5 inch plywood shelf onto the brackets. Ensure you do not screw into the dowel rods, or your shelf will not be able to fold as intended.
All Finished!
Time to sit back, relax, and enjoy all the extra room you just created with your new foldable sawhorses.
How to Build a Quick and Easy Sawhorse
A few months ago, Craftsman flew me up to Chicago to visit their Craftsman Experience shop for a blogger summit. (If you’re ever in Chicago, I definitely recommend stopping by the Craftsman Experience and checking it out. It’s free and open to the public.) I spent the day playing with tools and learning how to build various projects under the tutelage of several DIY bloggers. One project that I really enjoyed and found pretty dang useful was from Timothy Dahl, owner of the DIY blog Charles and Hudson.
Timothy showed us how to make a simple, yet sturdy sawhorse that even a handyman noob like myself could build without screwing up too much.
Why Do I Want to Build a Sawhorse?
Good question. Sawhorses come in handy in a variety of situations. The first and most obvious situation where a sawhorse is useful is when you need to saw something. Duh. A sawhorse gives the board you’re sawing the support and elevation you need to make a clean cut.
A pair of sawhorses can also be used to make a makeshift work table or scaffold. Just use the two sawhorses as the legs, and place a sheet of plywood over it. When I worked as a painter one summer back in high school, my boss would use a pair of sawhorses and an old door he found on the side of the road to make his worktable. Makeshift tables from sawhorses particularly come in handy when you’re setting up for a garage sale.
Let’s see. Other reasons you should build a sawhorse… How about for a makeshift seesaw? Or what about using it as the fulcrum for a home defense catapult? Just spitballin’ here.
And while you can certainly buy ready-made sawhorses at your local big box hardware store, you miss out on the fun and satisfaction of building a piece of equipment that will serve you for years to come.
Materials
Here are the materials Tim recommends for his sawhorses. It’s enough to make a pair.
- Six 32½-inch 2x4s (for the I-beams)
- Eight 30-inch 2x4s (for the legs)
- Twelve 3-inch wood screws
- Thirty-two 16D galvanized nails
How to Build a Sawhorse
Building a sawhorse is super easy. It makes for a great starter project for the man who has never really worked with tools, but wants to become handier around the home.
Note: This is one way to build a sawhorse. I know there are plenty of other ways to do it. This plan is great for everyday use in a typical suburban garage. If you plan on using your sawhorses for heavy work, you might try another design.
Measure and Cut Your Timber
The 2x4s I bought came in lengths of sixteen feet, so I had to cut them down to the needed sizes. Here I am measuring and cutting 32½-inch pieces for the I-beams and 30-inch pieces for the legs. Remember to measure twice and cut once!
Here I am using a portable compound miter saw to cut the timber. You can use a hand-held circular saw or even an old-school handsaw.
Take three of your 32½-inch 2x4s and screw them together in an “I” formation.
I found it helpful to drill a pilot hole before driving the screws in.
Drive three wood screws right down the middle on top and bottom of the I-beam. Place two of the screws near each end and drive the other one right in the middle of the I-beam.
Nail the Legs to I-Beam
Butt the end of the 30″ 2x4s into the top of the I-beam like so. Hammer two nails at the top of the leg so that they go into the middle I-beam piece.
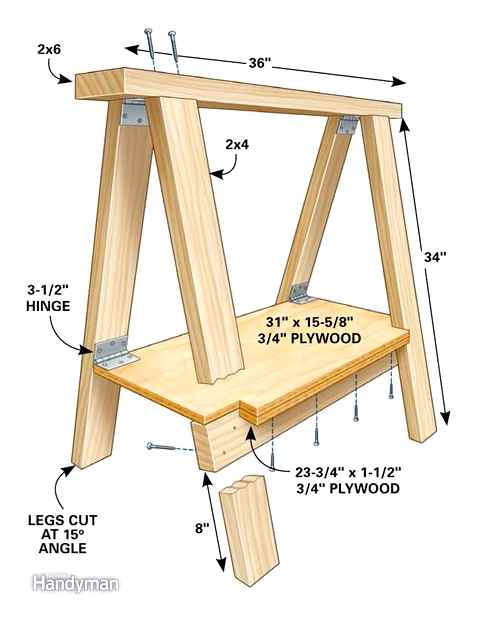
Nail two more nails into your leg so that they go through the bottom I-beam piece.
If you’ve done things correctly, you should form a box pattern with your nails. Notice my hammer dings in the wood. I need to practice.
Completed Sawhorse
My finished sawhorse. Rinse, wash, and repeat to make your second sawhorse for a pair. To store these bad boys, just stack ’em.
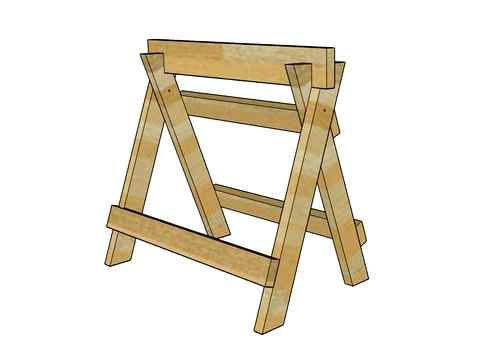
How to Build a Set of Sawhorses
Back some years ago, we used to “test to salt” of a carpenter based on whether or not he could whip up a sturdy set of sawhorses. It was common practice to have the new guy on the job make a set of wood sawhorses on his first day as a kind of test of his skills. We watched how long it took and also paid attention to the quality of strength and longevity. Passing the test was a way of earning respect and your place on the crew.
Nowadays a tradesman can purchase all types of foldable sawhorses from plastic, to metal, to aluminum, and, of course, there are a myriad of stands for tools or saws that slide, fold, articulate, roll—you name it! It seems that there is a portable stand or sawhorse made by any one of a hundred different manufacturers, each touting their quality and use for specific applications and tools.
With all the workstations and sawhorses available ready-made today, do you think you could pass this age-old test? This post is about wood sawhorses specifically and why they are still a good all-around fit for today’s jobsites.
A Timeless and Durable Classic
Wood sawhorses come in handy on jobsites whenever you need temporary workstations and material storage. During my career I’ve made many different wood sawhorses for different applications, and I still use them today on my jobsites because they are so versatile. The beauty of a wood sawhorse is that it can be easily modified for a specific jobsite’s circumstances. They can be cut down, added to, made large or small, and used indoor or outdoor. I don’t worry much about leaving my workstation set up outdoor—I don’t care if the sawhorses get wet, muddy, cut into, or forgotten when the project is done, because I can always make a new set from scraps in the shop.
Admittedly, a set of wood sawhorses aren’t the easiest things to transport from job to job because they are big and bulky. I purchased a set of sawhorses that are made of pipe with a wood 2×4 on top that fold flat like a pancake so I can hang them on the wall of my truck, out of the way. But when I need to set up for more than one workstation, I use a few different wood sawhorses and wood box beam setups to get exactly what I want for whatever circumstances I’m working in.
Strength, Economy, and Versatility
At my company here in Seattle, Westbrook Restorations, we are not only a remodel contractor but also a carpentry firm specializing in historic and vintage homes. No two projects are alike for us, and we work in a variety of circumstances that include limited working space, varying weather conditions, dust containment, hard access areas, and the like. By using wood sawhorses, wood box beams, and wood tables, we can cover an unlimited number of jobsite setup logistics quickly and easily. That’s why wood sawhorses are essential for today’s jobsites! You simply will not find that level of versatility in any of the ready-made tables, sawhorses, or saw stands on the market today.
How To Build A Set of Sawhorses
Sawhorses are essentially comprised of three components: the top (or box), the legs, and the leg brace. All components are made with 15-degree angles, and the legs will fan out at a compound 15-degree angle. That’s it! From there they can be as simple or complicated as you want.
HEAVY DUTY DIY Folding Sawhorses
Height
The first thing you need to do is decide how high you want your sawhorses. (Keep in mind, there is no standard height.) You might want them lower for working on cabinets, or higher for making cuts with a compound miter saw. There is no wrong answer here, but height is certainly something you want to think about with the end project in mind.
Length
The next thing to consider is how long to you want them. I’ve made sawhorses as short as two feet, and as long as four feet. The length really just depends on the application. If you start using the sawhorses and it turns out they’re too long for the space within which you’re working, they can always be shortened by removing the legs, cutting the box down, and then reattaching the legs.
Width
The width is totally up to you! I’ve used 2′ x 4′, 2′ x 6′, 2′ x 8’—and all the way up to a 2′ x 12′ in one case!
Top or Box?
Rip the spine out of a 2′ x 4′ at 15-degrees, then cut the top 5/4 x 6 to the same length.
Legs
Simply figure the length of the legs to what you want, and cut the top and bottom at 15-degrees with your saw set at a 15-degree angle. You can easily use a skill saw set at 15-degrees and just mark the top and bottom of the leg at 15-degrees. The tricky part is to remember you need four legs angling one way and four legs angling the opposite way. I say this because I’ve gone totally wild before, cutting all the legs only to find they all went in the same direction. I had to recut four more.
The Leg Span Brace
Finally, cut the leg span brace at 15 degrees on either side. You could cut the sides and top at a compound 15-degree angle to be fancy, but it’s not necessary. If you refer to the photo below, you can see I inserted the brace inside the legs. But you can attach it directly to the outside of the legs. The main thing here is to remember that this brace also should be in contact with the bottom of the box to add further strength—so it must be sized right for that purpose.
Assembly
Assembly is pretty easy using good course-thread outdoor screws. The first thing I do is attach the top to the spine through the spine so that there are no screws from the top. This just saves saw blades cutting through any screw heads. Then turn the box over so the bottom of the spine is facing up. Attach the legs, lining them up in the crotch between the spine at the top, making sure they are far enough from the end to reduce tripping on the bottom of the legs when it is set up.
I put in two screws to start with. Attach all four legs in this way. When you’re done, the sawhorse will be sitting on your bench top upside down. Next install the end braces using screws, lining up the legs to the sides of the brace. Make sure the brace is against the spine so everything is tight. Then simply add a screw or two to the top of the legs and really that’s all it takes to build a simple set of wood sawhorses!
There are as many ways to build a set of sawhorses as there are carpenters—and that’s a lot. Just remember: 15 degrees!
I’d be interested in seeing any pictures of sawhorses you’ve built—post them below with your story!