How to repair a trigger cable with your own hands. How to make a lawn mower…
Repair of electric and gasoline lawn mowers with your own hands
Repair of lawn mowers of both gasoline and electric may need at the most unexpected moment. We will talk about the main breakdowns of homemade and proprietary equipment, tell you what to pay attention to, and by what signs you can recognize the malfunction.
Lawn mower. A wonderful alternative to a manual spit that facilitates and accelerates the mowing of grass in a wide variety of places, including those where an ordinary braid for grass simply does not turn around. But for comfort and convenience there is a complex modern mechanism that requires tireless attention and regular service.
Regardless of the manufacturer, all units have a similar design. Therefore, the repair of the Viking lawn mower with your own hands is carried out similarly to the repair of other brands: Husqvarna, Shtil, Bosch, Garden, Oleo-Mac. A home.made lawn mower will not be exceptions, but elimination of breakdowns requires elementary knowledge. Consider the most typical reasons for the engine failure, and repair the lawn mower with your own hands in the field.
Repair of the mechanical part for all types of lawn mowers
Regardless of the type of engine, the mechanical part of the braid braid includes knives, the ejection or accumulation device of mowed grass and the transmission mechanism. Most often, knives come out or end the fishing line for a trimmer.
Cleaning the mechanical part of the Bosh lawn mower
Damage or bending of knives is visible to the naked eye. Depending on the material and the degree of damage, the knives are replaced or restored by simple bending into the original state. With severe wear, the cutting part can be submitted. DIY trimmer’s lawmaker, made with your own hands, can fail for many reasons. Most often, this is an excess of the maximum permissible load for torque and the engine, since a knife is used instead of a fishing line.
When examining, check the condition of the air duct for the supply of grass to the container and, if necessary, clean it. complex mechanical breakdowns require a complex tool, special equipment, professional skills and elimination of such malfunctions is better to entrust professionals.
How to restore a boss at the end of the cable
In this review, we will consider a few simple ways how to make a lead boss for a cable.
Method 1
To do this, we need a piece of a metal thin.walled tube of a suitable diameter, a bolt with a nut and a lead.
First of all, we cut off a piece of a metal tube of the desired length. Using a corner grinder, we make a slot on one side.
Perhaps you will also be interested to read how to make a fishing line for a trimmer for motorcycles (trimmer for grass) from plastic bottles.
The main stages of work
At the next stage, we take a bolt of suitable diameter (so that it enters the tube), and cut off the upper part with a hat from it. We screw the nut on this bolt.
Next, insert the bolt into the tube (as shown in the photo below) and fix the parts using a nut.
After that, it will be necessary to melt the lead (although they usually use a solder). Remove the slag on the surface and pour the molten metal into a home.made shape, having previously inserted the end of the cable into the cut in the tube.
When the lead froze, just remove the bolt with a nut, then push the cast beavers from the mold. Cut the corner grinder all superfluous.
Method 2
Bobs at the ends of the cables often break off, and usually a similar problem is solved by replacing the cable. However, you can restore it. You just need to cast a new boss.
First of all, it will be necessary to make a form for casting. To do this, we need a bolt (hairpin), a piece of a bar or a nail, nuts. We take a piece of hairpin or cut off the threaded part from the bolt. We clamp in a vice. We drill a through hole.
Then we drill a hole in the upper part of the hairpin with a drill of a larger diameter.
We recommend that you also familiarize yourself with the method of galvanizing metal without using electricity.
A steel bar or a nail will be inserted into the hole of smaller diameter (below the hairpin) so that you can extinguish a cast beavers from your seat.
The main stages of work
At the next stage, it will be necessary to make a slot in the upper part of the hairpin. Then we wind the nut.
We take the cable, we level its edge. Then this edge will have to be fluffed a little. We insert the cable into the slot in the hairpin and fix it with a nut. Also insert the metal pin from below.
We melt the lead and pour into the shape. Let us cool. Then we push the boss from the stiletto. We process a file or a grinding nozzle for a drill. The new tip for a cable is ready.
Method 3
If you plucked the brake on a bicycle (that is, a cable break occurred), then this problem can be eliminated on your own. And for this you will need to make a home.made device for repair.
A reliable way to combine a ragged cable
In this review, the author will share with us, although not the simplest, but rather reliable way to connect a ragged steel cable.
In principle, it cannot be said that this method is some kind of megaganous, and only the “chosen” can put into practice. No, it’s not at all. Every master will cope with this task easily, and indeed. any man who knows how to hold a tool in his hands.
First of all, you need to cut off a piece of stilettos of suitable length. In it, it is necessary to drill a through longitudinal hole (slightly larger than the diameter of the cable).
The main stages of work
At the next stage, clamp the hairpin in a vice, we take a corner grinder and cut the hairpin to the middle to make a hole.
We insert two ends of the cable from the ends of the hairpin and spread them through the “window” in the central part.
After that, wind up two nuts onto the hairpin, and tighten them to press the ends of the cable. Naturally, you need to delay not by hand, but with the help of worships.
Removing and disassembling the starter, replacing broken parts
To repair the starter of the trimmer for the grass, you will need to disassemble it first, and then collect it. This process is not a particularly difficult occupation. For work, you will need a screwdriver with the tip of the desired shape.
Everything should be done carefully, observing safety precautions, mainly that the spring does not injure the master if an accident.
Parsing the starting node
They disassemble the launch mechanism in order to install new parts instead of broken in the following sequence:
- spin a screw with a screwdriver, fixing the pulley with a starter lid;
- take out a spring and antennae;
- Remove carefully with the pulley (you need to unscrew the head or work, having dressed the glasses and gloves before);
- determine why the launch mechanism has broken;
- If the spring collapses almost completely, then it is replaced;
- When the spring exits from the hook, it is installed in the original place, bending the antennae before this (the photographs show the laying process);
To change the spring, you should work carefully and accurately: it can, under the influence of the effort caused by the installation of it in place, accidentally burst. Even if you carefully remove the video, then the spring strip flies very quickly from the coil and can injure your hand with its sharp edges.
Immediately putting a springy plate in the same place does not always work. It often slips, so attempts are required to repeat until the desired result is achieved.
Starter assembly
The assembly of the starting node is carried out in a number of stages:
When making the stated manipulations, it is necessary to lay two goals. If this is not done, then the spring over time damage the plastic cup, and when it is pulled. Because of this, a feeling appears, as if the spring had flown. To eliminate such a drawback, you need to install this part of a larger length or an additional goal.
When such spare parts are absent, you can just unscrew the screw a little, and the starter knot will begin to work without shaken. But this option is temporary. it is better to repair qualitatively as quickly as possible.
Spring tension
After installing the spring, it should be pulled. The following actions are performed for this:
- Remove the handle from the starter cord;
- Then the rope is inserted into the coil groove;
- They stretch the spring, rotating the coil in the direction opposite to the clock of the clock arrow (reviews);
- make the desired number of revolutions specified in the instructions for the use of the trimmer model used and the corresponding length of the cord used;
- At the very end, the rope is threaded into a hole designed for this, located in the starter cover;
- put the handle in place, fixing it with a node.
If after the repair the spring continues to fly, then you can get rid of this in the following ways:
- Squeeze the suitable piece of the plate into the groove at the location of the spring hook;
- drill holes on two sides of the groove in the coil, into which the spring hook is inserted and fix it using a wire.
Replacing a torn cord
A torn rope is replaced in the following sequence:
- The old cord is removed;
- choose a suitable rope (thickness and length);
- Having reached it through a special hole in the coil, a knot is tied;
- Sprinkle a spring, producing the required number of revolutions;
- Fix the pen.
It is better to stretch the spring plate along with the partner so that the edge of the cord does not hit the starter mechanism.
It is easy to assemble a starter on a trimmer and wound a spring, only you should do it carefully and with caution. For different models, the gas tanks of the launching mechanisms are the same, so they are repaired in a similar way. In this case, there are some nuances associated with their constructive features.
Common malfunctions of electric trimmers
Electric trimmers for grass differ from gasoline devices with a more simplified design. Conditionally electric braid is divided into mechanical and electric part. Accordingly, the same groups of malfunctions are distinguished, arising to these equipment.
Most of the breakdowns can not be visually identified. For this you will need to use various devices. You can visually determine the following:
- the integrity of the power cable is violated (insulation is broken from it, or it is clearly interrupted);
- sustaining or jamming of the trigger button;
- mechanical external damage to motorcycles;
- problems with the cutting part;
- stopping braids for grass when clogging with grass;
- Damage to the fork.
To find out which part has broken in other cases, you will need to disassemble the electric shock and sequentially check the most likely options. At the same time, they pay attention to the external manifestations of deviations from the normal operation of the device. They contribute to the establishment of the cause.
Repair of an electric trimmer for grass will require the presence of the following devices and tools:
Ryobi Trimmer Repair. How to replace the Throttle Trigger Spring
Electric braids for grass often do not work due to causes that are not directly related to them, but caused by a decrease in the supply voltage in the network or the ineffective condition of the used outlet used.
How to independently disassemble and repair an electric braid
Before disassemble and repair an electric braid, you should check the condition of the outlet and the voltage in the network. If its value deviates from the norms specified in the instruction manual, then you should not even try to work as a device without a stabilizer designed for appropriate power. Otherwise, the electric motor may fail. Only after determining the fact that the cause of the trimmer refusal is directly connected with it, we can begin to analyze the mechanism with the repair goal.
Dismantling and repair of the electric part
Dismantling of electric cosmos for the repair of its electric part is carried out in such a sequence.
- Put a trimmer for grass on a flat surface (for example, a table) that does not contain extra objects.
- Spin the screws of the lids located on one side.
- Remove the unscrewed half of the case, getting access to the start button, electric motor, brush unit, bearings, electrical connections (these elements are shown in the photo below).
Brush and bearing nodes are presented in the photo below.
The braid for the grass will work without a thermorele, you will only need to constantly check the temperature of the electric motor, periodically let it cool down. You can also install a new similar sensor.
The button for starting the electric motor can be checked by the jumper by the jumper of its contacts. If the trimmer for the grass works, then the problem is clear. But this option is unsafe. Everything should be done carefully so as not to get an electric shock. To change the button, you should use the screwdriver to extract it from the seat and attach the wiring from the old to the new. After replacement, you need to assemble an electric shout, and then check its performance.
Replacing brushes is required if they are destroyed. At the same time, it is enough to pull out the old ones from the grooves, and set the new ones in their place.
The connecting terminals on different models of trimmers are practically identical, so the connection-reference of the wires is equally performed.
Replacing the bearing is a rather complicated operation, because it can boast and not be removed from the engine shaft. Tighten or hit it carefully so as not to damage the rotor or seat.
When a trimmer electric motor for the grass fails, and it must be replaced with a new one, you should carefully remove the fan and bearings, and then install them in the same place. In terms of expenses, replacement is almost comparable to the acquisition of a new mechanism. Its implementation in the absence of experience with electric motors is best entrusted to specialists.
Assembly Electrics
Instructions for assembling the electric part of the motorcycles are as follows:
- install the engine, tightening the fasteners;
- connect an electric circuit;
- The wires are placed neatly between the individual compartments into existing recesses;
- close the top cover, snapping the locks and screwing it with screws.
After assembly, check the performance of the device.
There are a lot of possible breakdowns in gasoline and electric trimmers. So that the device is working for a long time, it should be kept clean, in a dry place. An important point is regular preventive measures (for example, reducer lubrication) and compliance with operation rules set forth in the instructions for the device. Buying equipment is better than high quality from well.known manufacturers.
Disassembled the mechanism, it is recommended to take pictures of the process in stages so as not to forget anything, and when assembling, not to miss a single part. When replacing parts, you should pay attention to the choice of suitable components: it is better to use original spare parts.
In some models, the rod consists of two parts. a coupling is used to connect them. Such devices are convenient during transportation.
How to make repair of the lawn mower with your own hands?
Those who have land are very familiar with what struggle is weed.
Especially when it often rains and the grass grows not by the day, but by the hour. Earlier, and sometimes even now, this issue was resolved with the help of a good old braid for grass.
But technologies are not standing still and now in this case, assistants such as electric and gasoline lawn mowers help.
The gasoline mower has several significant advantages over electric, such as mobility and lack of danger of electric shock. But there are many drawbacks, for example: high price, a lot of noise, expensive fuel and significant weight.
Electric mowers are cheaper, easier, work on inexpensive energy, and are not difficult to maintain and repair. These advantages become the main reason for their great popularity among buyers of this type of technique.
But despite the pretty good quality, improper operation and a lot of load, they can disable the device. In such cases, you should not immediately carry the device to the repair shop, but try to find and eliminate the cause of the breakdown yourself. over, as mentioned above, electric lawnmands do not have as many nodes and details as gasoline.
The main thing is to have some tools and faith in yourself. In this article, I will just show you how I did my own repair.
AL-KO, the lawn mower of the company, has serious problems in work, namely: the engine stop without load and its strong overheating, was taken as an example. The motor stops, buzzes and start it again, only re.pressing the “Start” button helps. The button has to restart almost every 30 seconds, and with further work and more often.
Of course, you can work, but it is very annoying and gives the feeling that somewhere the problem is. Therefore, I wanted to figure out where?
After the mower was working within an hour, the engine temperature was measured. It was impossible to touch him with a finger. He directly radiated heat. If you continue to pay attention and continue to work on such a mower, an electric motor will inevitably fail.
It is necessary to determine the cause of the motor overheating. To do this, remove the top cover of the case, under which the engine is located and its power chains.
The lid is held on six screws with a hat under a cross screwdriver.
Unscrew these screws and remove the lid. upward.
Having removed it, you can see the impeller, the capacitor, two connectors and the engine itself.
At first glance, no special problems are invisible. The engine winding darkened slightly from the temperature, but so far it is not critical.
To more carefully inspect the capacitor, it is necessary to unscrew the mount and pull it out.
The capacitor of some external damage did not show.
To check it, you need to disconnect the capacitor and feed the engine for a short time. If he did not start and began to buzz, then the capacitor is intact, because the engine was launched with him. Disconnect the power and connect the container connector back to the engine circuit.
Next, try to twist the impeller. It is mounted on the axis of the rotor and rotates rather tight.
And the reason for such severe rotation is a mechanical brake, which for safety stops the engine rotation when the power is turned off.
It looks like a sleeve that moves freely from top to bottom, along the rotor axis.
Когда напряжение на двигатель не подано, эта втулка прижимается верхней частью о крышку, на которой приклеено две резиновые полосы. Thus, the knife is inhibited on the rotor shaft.
When feeding, the brake sleeve under the influence of the magnetic field is drawn to the center of the rotor and provides free move.
With a careful examination, this sleeve with the brake noticed that at the time of turning on the engine, the brake is retracted and gives the shaft free rotation, but after 2-3 seconds it is released again and begins to slow down the motor. This should not be. Hence the stop of the knife during operation and overheating of the engine.
To find out what is the reason for this work, you need to remove and disassemble the engine.
To do this, disconnect the connectors and put the device on the side to get to the clamping screws. Access to them closes a knife with mounting elements.
To remove it, first you need to unscrew the knife bolt (cm. Figure below).
Direction of rotation, like a regular bolt, and not with left thread. That is, unscrew it counterclockwise, and tighten the clock.
The head of the bolt is plastic, so using the key, it must be well planted so as not to “lick” the edge.
After extracting the bolt, the knife and its plastic disk are removed.
Under it is a height sleeve. With its help, you can slightly lower the knife.
Adjustment is carried out by the washers put under the sleeve (see. drawings below).
We remove everything, only the engine shaft and the hexagonal screws of its fasteners remain.
The key for these bolts has a distance between faces of 6 mm. Unscrew them counterclockwise. Removing the last screw, with one hand, hold the engine.
Next, put the mower on the wheels, and clasping the engine with our hands. we raise it.
To disassemble the motor, you need to free tightening studs. We unscrew them all.
Remove the impeller with two screwdrivers.
We proceed to the removal of the back cover. A wooden block and a hammer will help this.
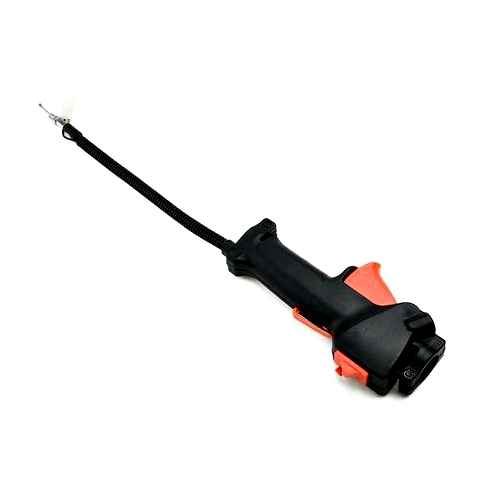
But first you need to mark the position of the covers with something sharp to the engine body.
Put the engine on the side and hit with a hammer, through a wooden gasket, on the rear shaft.
The motor at that moment should hold another person.
We hit until the axis comes out of the bearing to the end.
The most common problems
Here are the most common malfunctions:
- the engine does not start;
- The motor stalls arbitrarily;
- The engine does not gain momentum or does not hold them;
- Immediately after the start of the mowing, the engine speed falls and it stalls or works with interruptions;
- smokes strongly;
- It goes badly;
- does not stop even after the operator released the wheel drive lever;
- shakes hard;
- Poorly cut the grass.
The engine does not start
There are quite a lot of reasons why the motor does not start:
Push Mower Cable Kill / Zone Cable Easy Fix Step By Step
- empty fuel tank;
- a air filter is clogged;
- a muffler is clogged;
- The ignition switch is installed in the wrong position or faulty;
- The air damper control lever is in the wrong position;
- faulty candle;
- broken or clogged carburetor.
Primary inspection
To establish the real cause of this defect, you must first conduct a full external inspection and make sure that the openings of the air filter or muffler are not clogged, there is gasoline in the tank, and the throttle control lever and the ignition switch are in the correct position.
If everything is in order with this, then it is necessary to carry out pre.launch work, including cleaning air or fuel filters, described in detail in the instructions for the operation of the mower, and then try to start again.
After making sure that the motor still does not start, the mowing is placed on the table and proceed to a more detailed search for the reasons.
First, the spark plug is twisted and tightly plug the candle hole with your finger, then smoothly, but quickly and strongly pulled the hand starter cable or pressed on the electric launch button.
The moving piston should create sufficient air pressure so that it pushes the finger and goes outside. If this does not happen, then the motor needs serious repairs, which is difficult to make at home, so it is better to take the mower to a specialized workshop.
After all, the reason that the piston does not move after the starter’s cable or rotating the shaft of an electric starter may be:
- Damage to the starter, because of which he does not transmit the energy of rotation to the engine shaft;
- The cut off the flywheel that connects the flywheel and the starter with the engine, and also provides the correct ignition angle.
To eliminate both malfunctions, not only tools, but also skill are needed, so those who do not have the skill of repairing any engines are better not to try to eliminate such problems on their own.
Further check
If the piston moves, then you must first check the fuel supply, for which the candle is thoroughly wiped with a dry clean rag, then screw it into place, and the regulator of the position by the air damper is placed in the “OFF” position, as during the start of the engine.
After that, the fuel is pumped up (if the engine design provides) and twitch the hand starter cable several times or pressed on the electric starter button and hold it for 1-3 minutes.
Then, the lever of the air damper is transferring to the “ON” position and the candle is unscrewed, which is carefully examined.
Wet contacts indicate that gasoline enters the engine and the problem of ignition, and dry contacts say:
In both cases, knowledge and equipment are necessary for proper diagnosis and repair, therefore, it is better to take the device to repair the apparatus to a specialized workshop.
If the fuel comes, then it is necessary to check the external condition of the ignition coil and the high.voltage wire. If they have cracks or poor contact as between the wire and the coil, so at the place of connection of the wire with the candle tip, they must be replaced.
If everything is fine, then you need to check the spark, for which you can use both a deliberately serviceable candle and a bolt suitable in diameter, which is inserted instead of a candle in a high.voltage wire.
The operations described below, if they are performed with errors, can damage the ignition coil, so if you are not sure that you can do everything right, then it’s better not to take risks and entrust such a check to professionals.
The candle is leaned with threads against the ribs of the engine cooling shirt, and the bolt is placed so that it does not come into contact with the mowing case or its engine, and the distance from it to the cooling shirt was 1-2 mm.
After that, disconnect any wire going to the ignition switch, then pull the lever of the manual starter or press the electric button and see if the spark will appear.
If there is no spark, then the device does not start for one of the reasons:
For the repair of these damage, skills and equipment are needed, so those who do not have them are better to trust professionals. If there is a spark, then the problem is in the spark plug, so after replacing it will work.
The motor stalls arbitrarily
The most frequent reasons why the engine stalls during operation are:
- Dirty air filter;
- Dirty fuel filter (only for models with a fuel filter);
- faulty ignition switch (does not completely open the ignition circuit);
- damaged insulation of the ignition shutdown wires;
- faulty air damper drive;
- the tightness of the ignition coil is broken or its winding is broken.
The primary inspection is performed in the same way as described in the previous section. If everything is fine outwardly, then carefully examine and feel all the wires suitable for the switch that blocks the operation of the ignition system, is possible somewhere damaged and when contacting the naked metal of the case, there is a short circuit that extinguishes the spark.
A gasoline lawn mower is a complex motorized equipment that needs proper timely maintenance and periodic repair.
Now you know what malfunctions can independently eliminate most of the owners of gasoline lawners and how to do it, and in which cases it is better to contact the workshop.
What is needed for home repair?
To eliminate any breakdown of the electrimmer, you will need:
- repair skills;
- the ability to repair electrical equipment;
- Understanding the principles of work Electrics;
- knowledge of how a specific model of a trimmer for grass is arranged;
- Corresponding tools.
Electric trimmer for grass is a complex electromechanical device, so you will need the skills of repairing mechanisms and electrical equipment.
In the first case, repairs and adjustment skills will be adjusted:
In the second case, the skill of repairing electrical equipment equipped with electric motors, for example, household appliances or medical equipment, but if there are no such skills, even the ability to repair and lay the wiring is suitable.
After all, the main thing is to understand the general principles of the operation of electrical equipment and work with electrical devices.
Understanding the principle of operation of the electrocos and all its individual elements is one of the conditions of successful repairs, because the task is to restore the normal functioning of the damaged element, but how to do this, if you do not understand the principle of its work and the tasks performed by it?
Loading device Electrics
Separation of electrocos into separate blocks allows you to more accurately determine the damaged part and the reason for its failure.
We offer to use the following configuration of the blocks:
- power cable;
- internal wiring;
- power control elements;
- electric motor;
- barbell;
- intermediate shaft;
- gearbox;
- cutting tool (coil, disk or knife);
- frame;
- Handles.
Devices with the lower location of the engine are deprived of an intermediate shaft and gearbox, however, they have all other blocks, so such a pollinating design is applicable to any electrical model.
Repair of electric and gasoline lawn mowers with your own hands
Repair of lawn mowers of both gasoline and electric may need at the most unexpected moment. We will talk about the main breakdowns of homemade and proprietary equipment, tell you what to pay attention to, and by what signs you can recognize the malfunction.
The lawn mower is a wonderful alternative to a manual spit that facilitates and accelerates the mowing of grass in a wide variety of places, including those where an ordinary braid for grass simply does not turn around. But for comfort and convenience there is a complex modern mechanism that requires tireless attention and regular service.
Regardless of the manufacturer, all units have a similar design. Therefore, the repair of the Viking lawn mower with your own hands is carried out similarly to the repair of other brands: Husqvarna, Shtil, Bosch, Garden, Oleo-Mac. A home.made lawn mower will not be exceptions, but elimination of breakdowns requires elementary knowledge. Consider the most typical reasons for the engine failure, and repair the lawn mower with your own hands in the field.
Repair of the mechanical part for all types of lawn mowers
Regardless of the type of engine, the mechanical part of the braid braid includes knives, the ejection or accumulation device of mowed grass and the transmission mechanism. Most often, knives come out or end the fishing line for a trimmer.
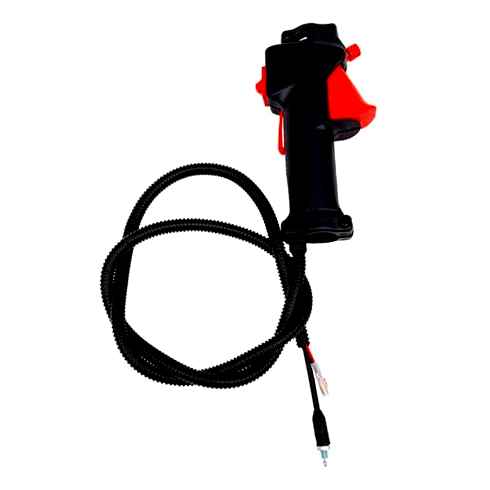
Cleaning the mechanical part of the Bosh lawn mower
Damage or bending of knives is visible to the naked eye. Depending on the material and the degree of damage, the knives are replaced or restored by simple bending into the original state. With severe wear, the cutting part can be submitted. DIY trimmer’s lawmaker, made with your own hands, can fail for many reasons. Most often, this is an excess of the maximum permissible load for torque and the engine, since a knife is used instead of a fishing line.
Restoration of the handle of a trimmer for grass
When examining, check the condition of the air duct for the supply of grass to the container and, if necessary, clean it. complex mechanical breakdowns require a complex tool, special equipment, professional skills and elimination of such malfunctions is better to entrust professionals.
the reasons
Pull the cord several times to determine the gap in the cord. Minor backlash indicates clogging or clogging inside the body in the upper part of the engine. Lack of backlash means that the cord is hooked and can be damaged. Unscrew the screw in the upper part of the case to gain access to the cord and the pulley disk for further verification.
Inspect the cord and pulley for the presence of stones, sticks or confusing weeds around the disk or cord. Try to remove an object from a disk or cord; If this is not possible without further damage, pull the disk and cord together to get access to an extraneous subject. Clean the disk of dust and dirt. Return the disk and the cord to your place, changing the procedure for their removal.
The cable.hooked disk or pulley body can seriously damage the cable and the pulley disk. Inspect the cord to determine the degree of engagement and the severity of the point holding the cord. Over time, pulley discs can break or form sharp edges and ultimately hook the cable at the damage point. Carefully remove the pulley and cord together. Wipe the cord completely and throw it away. After damage, the cord can easily snap. Replace the cord with a fresh cord, setting in the way the reverse of how you removed the old cord. Make sure that the cord is leveled with holes and recesses, otherwise it will hook again.
Prevention
Follow possible problems when mowing high grass, weeds or rocky soil. Grass or weeds are higher than a mower, can get confused in moving parts or drop seeds and garbage in open cavities, such as the hull of the pulley disk. Dirt and dust rise up, and the mowing can settle in open cavities. Clean the mower after each use. Blow out the compressed air into the chamber of the pulley of the pulley to displace the garbage from the inside. Inspect the cord on a regular basis in search of scuffs, breaks and cuts. Replace the cord if you find damage.
Measure the length between the engine body and the gas mower handle. Double this number to get the length of the new cord. Use coating cord to prevent sticking or sudden damage. Remember, however, that the coating cord will lose the coating over time due to friction between it and the disk.