Milwaukee Sawzall Reciprocating Saw Blades – a Quick Guide. Longest reciprocating saw blade
Milwaukee Sawzall Reciprocating Saw Blades – a Quick Guide
Shopping for reciprocating saw blades can be a daunting task these days, due to the sheer number of different options.
A reader wrote in today, asking for some help in making sense of all of Milwaukee Tool’s various Sawzall reciprocating saw blade options.
Milwaukee actually has 18 distinct categories of reciprocating saw blades listed on their website, but the selection becomes simplified once you understand what makes them different.
Milwaukee Premium Sawzall Blades
There are 3 product family names you need to know – The AX, Torch, and The Wrecker.
The AX blades are for wood-cutting.
TORCH blades are for cutting metal.
The WRECKER are multi-purpose types of blades for cutting wood, nail-embedded wood, plastics, and metal. It’s a general purpose-type of demolition blade.
These premium blades often have special features and tooth profiles to deliver faster cutting, longer life, and greater tooth durability.
There are 2 basic styles of blades – carbide and non-carbide, with bi-metal or ice-hardened teeth depending on the style.
The blades with carbide teeth are the longest-lasting (and also the most expensive).
Some of the styles are self-explanatory, such as The Ax with carbide teeth for pruning clean wood blade.
Milwaukee Standard Sawzall Blades
There are also “standard” Sawzall reciprocating saw blades.
Clean Wood Cutting Blades
Nail-Embedded Wood Blades
Standard Multi-Material Blades
Milwaukee Ice-Hardened Standard Sawzall Blades
Ice-hardened blades offer longer durability.
Ice Hardened Metal Blades
Ice Hardened Multi-Material Blades
Milwaukee Specialty Reciprocating Saw Blades
Tungsten Carbide Grit Blades – for cutting tile, masonry, fiberglass, and other abrasive materials.
There is a catch-all category for other specialty blade styles:
- Metal Scrolling
- Wood Scrolling
- Plaster
- Drywall Access
- Ductwork
- Rough In
- Flush Cut
- Brick and Block
How to Choose Milwaukee Sawzall Blades
Things get fairly straightforward once you sort blades according to what you’re cutting, such as wood, wood with nails, or metal.
Once you shop according to application, blades are generally sorted in “good, better, best” types of tiers.
For instance, if you need a pruning blade, you have two options – the standard Sawzall pruning blade, or The Ax pruning blade. From there, you choose the length. The standard blade is available in 9″ and 12″ lengths, and The Ax pruning blade is available in 6″, 9″, and 12″ lengths.
The premium specialty-named blades often have features that deliver greater performance. Aside from that, stepping up to different levels generally reflect differences in blade durability (and price).
For instance, a blade with ice-hardened teeth with usually last longer than standard blades, and blades with carbide teeth last longest.
Ice-hardened blades are said to last up to 50% longer than standard blades, and so you’ll have to do the math to see if they’re worth the price increase. (Personally, I don’t go out of my way to buy them.)
Wood-Cutting Reciprocating Saw Blades
Clean-cutting? There’s only one option.
Pruning? There’s a standard pruning blade and premium The Ax pruning blade with carbide teeth.
Metal-Cutting Reciprocating Saw Blades
- Basic: Standard
- Improved: Ice-Hardened Metal Blades
- Improved: Torch
- Better: Torch Ice Hardened
- Best: Torch with Carbide Teeth
There’s also the Sawzall Torch with Nitrus Carbide blade, for cutting cast iron and other thick metals. This blade is described as the next generation of carbide teeth technology, and so it’s marketed as being a level up from the Torch with carbide teeth.
Metal-cutting blades require additional sorting, as the TPI (teeth per inch) depend on the material being cut.
Some blades are suited for any metal cutting, but most are application-specific, such as for thin metal cutting (e.g. tubing or sheets) or thick cutting (e.g. pipes and structural parts). You will sometimes see a graphical depiction of a sheet or thin-wall tube for thin metal-cutting blades, and an I-beam for thick metal-cutting blades.
Milwaukee’s applications tables show the following recommendations:
- 10 TPI: threaded rod, schedule 80 pipe
- 14 TPI: angle iron, schedule 80 pipe
- 18 TPI: rigid conduit, strut
- 24 TPI: EMT/tubing, duct/sheet metal
The Torch blade with carbide teeth has a 7 TPI design for cutting thick metal, such as black pipe, angle iron, cast iron, stainless steel, and other such materials.
Multi-Material Reciprocating Saw Blades
- Basic: Standard
- Improved: Ice Hardened
- Better: The Wrecker
- Best: The Wrecker with carbide teeth
The multi-material blades are great for demolition work, or for applications where you will be cutting multiple materials without having to change blades.
The multi-material blades have dual-pitch cutting edges and can cut wood, wood with nails, PVC and similar plastics, copper, aluminum, non-ferrous metals, thick metals.
The standard blade has 8/12 TPI and 10/14 TPI options. I would assume the higher-pitch might be a little better suited for cutting thinner materials.
Which Milwaukee Sawzall Reciprocating Saw Blades do I Prefer?
For cutting wood, I grab an “Ax” blade, either the standard blade or the one with carbide teeth. I rarely cut wood with nails, but the Ax is a great choice regardless.
If I need a clean-cutting blade, I don’t use a reciprocating saw.
For metal, I generally go with The Wrecker blade, as it gives me more mileage.
I would go with the Torch blade for application-specific metal-cutting tasks, but most of my metal-cutting tends to be incidental or unplanned. I have metal-cutting blades for if or when I need them, but the Wrecker is more of a toolbox.
I also use standard blades on occasion, mainly because I purchased a couple of assortments a few years ago and haven’t used them up yet. The standard blades work great, but Milwaukee has put their best features and engineering into the named blades (Ax, Wrecker, Torch).
If I’m working with a difficult material, or in a space where I’m likely to quickly dull or damage a blade, I sacrifice a standard blade to get the task done.
Is there really a difference? Yes – I have noticed differences in cutting performance and longevity. Are the more premium blades worth it? I think so.
Milwaukee’s assortments offer great per-blade pricing on standard blades – especially during holiday shopping seasons, but if I’m buying individual blade sizes and 5-packs, I go for the premium styles.
42 Комментарии и мнения владельцев
We were always quite happy with MK Morse b-metal blades. Worth a try if you are seeking a different (also made in USA) brand: https://mkmorse.com/recip
I almost exclusively use MK Morse blades, particularly their CTR carbide blades. https://mkmorse.com/CarbideTippedRecip
In my personal experience, they seem last longer. I haven’t tried the new Diablo Steel Demon Amped or Milwaukee Torch Nitrus, but the standard carbide Steel Demon and Torch seemed much more prone to teeth breaking than the MK Morse. It could be I just have a bias for them as well, I’ve had really good experience with all their stuff (hole saws, metal circ saw blades, Band saw blades, etc.) The MK Morse are also a bit tougher to find, I get mine at Menards, usually stock up when they have their 15% bag sale.
I love their holesaws, hands down my favorite and they’ve kept up the quality over the years unlike most others (Starrett is still good, too, although with apparently more defects these days). Haven’t tried their recips although if the process and material is like the holes and bands, they’ve got to be great. Mostly sticking with Diablo recip lately…those have been much better than the current Milwaukee or Lenox for me. Many of the bi-metal blades out there now are hardly even sharp out of the package…
Thanks for the breakdown, Stuart. The variety of blades they offer is bewildering. I wonder how other people figure out whether a blade is a good value. To me, if a blade that lasts twice as long costs twice as much, that’s a bargain, because a worn blade cuts slowly and roughly, making you less productive. Also, stopping to change blades hurts your productivity, even if only a little bit. And lastly, a worn blade can stop you in your tracks if you run out of spares. I’d be willing to pay maybe, and I’m making this up right now, 2 1/2 times the price for a blade that lasts twice as long. How do other people think about it? Also, what the heck is “nitrus carbide”? That doesn’t make sense as a chemical name. It also means we can’t look up hardness or toughness numbers, and get a better sense if it’s worth the premium.
This is just a guess here, but perhaps Titanium Carbo-Nitride is involved, perhaps as a coating? TiCN.
“A unique carbide blade” – that’s all they specified when it first came out. I take it to be a bespoke carbide for thick metal cutting applications. Most brands aren’t able to get into the level of detail I need, and so I rarely ask about proprietary metallurgy anymore.
Are you really telling me that you, of all people, don’t have a gas chromatograph and SEM on your workbench? I never expected to end the day so disappointed in you when I woke up this morning.
None of that makes a difference. The melt shop needs chemical composition to control contaminants. An SEM is a university toy to understand principles. But neither one tells you hardness, abrasion, cutting performance, etc. most of the magic is in casting, forming, and heat treatment. For instance Damascus and Japanese steel has so so chemistry but the folding and heat treatment is the whole key. Plus when ir comes to heat treatment there is a lot of trial and error. Plus it’s a moving target. And tweaking one thing affects everything else. So even if they gave you every detail next month is different. Carbides are like diamonds. It is a completely foreign material to the steel. They are more or less embedded physically. Some chemical bonding can be done but fundamentally a cubic crystal and a hexagonal one never mind atomic spacing are fundamentally incompatible. Plus thermal properties are different: And like diamond caebidea are very hard so they hold an edge but also brittle. They require some kind of tool holder which is the steel blade.
Perhaps, but an SEM would help to explain why the teeth on one saw blade might be harder and wear resistant than those on another. It’s an easy way to analyze carbide grain size, structure, and composition.
It’s on my shopping list. =) No, seriously – if I win the lottery, that’s the first thing I’m buying – a FESEM with all the trimmings and a service contract. That, and a lease on an industrial space. I can always rent time at local university labs, and I might some day, but the hours would add up fast. To build knowledge about different accessories’ carbide teeth, from the ground up, would take an inordinate amount of time. 2-3 years ago I looked into an inverted stage optical microscope, which can be used to analyze polished metallurgical samples (e.g. different tool and accessory alloys), and was quoted 45K – 55K. I was quoted 11K for a basic entry-level model. So… that’s not a viable alternative either. And just as seriously, on a scale of 1 to 5: 1: level of understanding the average media entity needs to talk about a product 1.01: vague alloy name/description marketing claims 1.1: level of metallurgical insights that can be gleaned after a lot of back and forth with brand reps 4: level of detail I would like to have 5: max insights known to the brand If there’s a lot of interest, or this was a major product line, that would be different. But candidly, asking for greater insights into carbide claims is not a productive activity. However, if anyone at Milwaukee’s accessory team is reading this, perhaps they could volunteer some information and maybe a micrograph or two comparing Nitrus Carbide and standard Carbide teeth?
Generally speaking you get wildly different steel crystals using liquid nitrogen mixed with traditional heat treatment. You can get tool steels so hard they shatter like glass…although that takes it too far. The crystals get huge and hardness goes way up at the expense of ductility. Maybe not as useful as an SEM but with acid etching a conventional 40-109x optical is useful and STEMs are lunch box size and quite powerful. A lot of metallurgical labs do just fine with a reasonable “hobby” optical microscope and an arc spark for the melt shop. The ultimate in electron microscopy is the TEM but it isn’t badly priced by itself but the fridge, vacuum, and sample prep lab that come with it drive the price into millions. One thing about metallurgy (I hold an MS in it…I know what I’m talking about) is it’s a “soft science”. Too many variables. There is a LOT of experimentation and honestly we do not truly understand the mechanisms behind some things. Google “ductile iron” as an example. It was discovered purely by accident. There are 4 theories about how it works, all disproven. Nobody knows how it actually forms but municipal water pipe, railroad wheels, and Diesel engines all make extensive use of this advanced material. Crap heat treatments are similar and if you see “nitro” or “crap” that’s what they are talking about. Read up on liquid nitrogen heat treatment and what you will find is mad scientist stuff, that somehow works but again, we don’t know exactly why.
I didn’t use TEMs too often – one was very old but relatively easy to use, and the other was cutting edge but incredibly complicated and fickle. Both machines were frequently down. The cutting edge machine produced great data, but required a lot of training and practice to master and I wasn’t anywhere close to that. I never used a STEM. I trained on and used a couple of different SEMs, ranging from an old Hitachi to a modern Zeiss. Operating the Zeiss FESEM was by far my favorite part of investigative lab work. “What am I look at, and WHY does it look like this?” provide the most fun. Cryo heat treatment has been on my list of “ooh, I need to read up on that” list. There are actually a lot of fields where we can see something works but the mechanisms remain unclear. Around 15 years ago, I was surprised to learn that there wasn’t any consensus as to how fluoride works to protect teeth against decay. Maybe that has changed since then, but I had assumed it was established science and it wasn’t.
I’ve been curious but they won’t divulge much anymore. Kind of assumed it was a nitrocarburizing treatment, which is basically a different kind of case hardening technique that can actually form iron carbides on the surface. That seemed to get a lot of interest a half dozen years ago or so, but that was all with steel as far as I know. If that’s what Milwaukee’s up to it’d be interesting to learn how that works with carbide products as they seem to indicate with the teeth on their blades.
Hm, that’s an interesting thought. Another possibility is they are playing with the binder and/or the size of the carbide particles. I know “carbide” is actually a composite of tungsten carbide or titanium carbide particles in a binder, typically a cobalt alloy. (I don’t know about other carbides.) I recall some years ago a manufacturer claimed to have improved the toughness of the carbide teeth on their saw blades, apparently by playing with the particle size and maybe the composition of the binder. Improved toughness would mean the blade lasts longer, even if the new “carbide” isn’t much harder.
Maybe so but I don’t know what all there is left to do in that area. We’ve had micrograin carbides for many many years now and refinement in area as well. Some of those get quite expensive and to my knowledge are limited to machine tooling and specialized heavy industry applications, where the cost can be offset by increased tool life/reduced downtime in production (or in sharpening time/service costs). The way Milwaukee and most others have gone with BS marketing, I wouldn’t be surprised if they’ve just put a verbal spin on something normal, but who knows. I think it may have been Freud that brought micrograin to the masses in the mid 90s or so, and it wasn’t long after that DeWALT introduced that into their planer blades, and Delta did as well…then it crept into router bits. All of that was well behind the curve in terms of development and what was available on the consumer/retail level. Improvements in seating/brazing followed at the same pace and for the most part that seems pretty great these days. Maybe Milwaukee will let some of this leak or someone can pry it away from a good rep or service tech.
I should add that some of this tech isn’t necessarily beneficial for typical handheld tool use. I think that’s especially true with recip saws and also circular saws to a degree. All carbides are still friable, even the best ones these days, and when the tool or the work cannot be fixed in place with some degree of control or rigidity that approaches a shop situation (or worse…neither is well secured) then reduced performance and accelerated edge wear (or breakage) gets more common. So upping the tech in situations like that just increases the price and/or frustration maybe without delivering the real benefits.
I tend to ask “what, how, why?,” and this usually crosses into proprietary “we can’t talk about it” territory.
I think one thing that’s worth pointing out about carbide blades, at least in my experience, is that while they do last longer generally speaking, they are also less tolerant of abuse. If you try to use too coarse of a carbide blade for the size of your work you can expect to break teeth off long before you actually wear the blade down.
I’ve used the Torch carbide cast iron-cutting blades recently. They were good probably worth the extra cost. But in all honesty, I also tried the Diablo specialty cast iron blades; they were better! I will keep one Diablo blade in the toolbox for this specific purpose.
I used 1 torch carbide toothed blade and did a substantial amount of cutting on 8 10 inch “I” beams and thick-walled pipe. It cut it quite easily and I was very impressed, I was also using Milwaukee’s “super” sawzall which had absolutely no issues tackling the large task. The blade was shot when I finished but it did a substantial amount of work so I really liked the performance.
I recently bought some Diablo and Milwaukee carbide-tooth reciprocating saw blades, both for “thick metal”. I have a piece of railroad track I was going to shape into a small anvil and I was curious whether a reciprocating saw could make any headway on it. I realize that’s not a reciprocating-saw type task, but I was thinking of that video posted here of that fellow cutting through a tri-ball trailer hitch. I was surprised to read that “thick metal” only means up to 1/2″. Considering the Diablo blades are 9-inches long, I assumed they could cut something thicker than that. So far, neither blade has been very good. I would give the nod to the Milwaukee, but that doesn’t mean its the right tool for the job. The saw certainly is no quicker than a cutoff disc and it’s easy to ruin the teeth. This comment is kind of apropos of nothing – except I happened to be using carbide recip blades recently. Is there a reason the carbide blades have larger, more widely-spread teeth than traditional metal-cutting blades? I noticed that right away. They almost look like wood-cutting blades.
Goodness…track is some tough stuff to cut!! They generally do it with a special shear, but in the field they sometimes use very specialized abrasive blades (expensive and large). Used track is way worse to deal with than new track. I suspect the spacing on the carbide teeth might have more to do with machinery/manufacturing restraints but it’s possible that maintaining a durable tooth geometry needs a little more space (plus chip clearance). I noticed that Diablo’s 20t carbide blade is strip welded pretty much the way bi-metal is…thought that was interesting and then realized how difficult it would be to try and weld carbide so small and confined like that.
It’s been tough slogging! Kind of a silly project for me – I’m just not equipped to deal with metal that thick. I’m sure the best approach is just to mill it. I quickly abandoned my attempt to cut through the top horizontally to flatten it (what’s that, like 4″ of steel or so?). Cutting it from each side with a 7″ disc works ok. I don’t have any high-quality large angle grinders though, so it bogs down. Once there’s only about a 1″strip down the middle, the reciprocating saw CAN actually cut it. Still slow and I have to add oil to keep things cool – but it works.
If you dont already, try keeping the speed slower with your recip while cutting thicker metal. Sounds like a job for a bandsaw or cutting torch to me. Honestly though If i had that to cut ID take it to a machine shop I used to work at, probably a waterjet or industrial bandsaw.
Here’s a fun nugget that shows a little. If you search YouTube for “milling railroad track” or “railroad anvil” you can see a lot of things not to bother trying and the troubles most people suffer through. Ha. https://www.YouTube.com/watch?v=q-PUu509LME If a machine shop is willing to take this on, they’re likely to charge you out the wazoo and either include or tack on replacement tooling costs. A bandsaw would be far better than anything toothed with reciprocating action, but abrasives are probably where it’s at for the biggest convenience. To flatten it, I’d pick up several good ceramic wheels. In this case, 3M and Norton are worth the cost…maybe Pearl if you have those around. The USA brands who have ceramics will be the good stuff…in general China abrasives are a much poorer value despite the lower cost, and some of their “ceramic” is, shall we say, suspect. Use them with moderate pressure and steady long strokes (keep the hot spot moving). Final smoothing and polishing will be a chore of patience. I’m not sure I’d waste any scotchbrite discs on this but they might work.
I’m not sure what I just watched, but the piece of rail he’s working with is the twin of mine – including the work-hardened rounded-over edge. I’m in Canada so I’m sure mine is from CN too. It’s a substantial piece of rail. The piece I’ve got is pretty long too. Guess I’m not alone in the struggle to work with it.
When I think of finish cutting large sectional steel – I think about one of the do-all Band saws that we had in the shop. We also had a big Marvel plate saw – but that would have been overkill. For cutting a large piece down to manageable size – perhaps you might start with a torch then move to abrasive wheel cutting and grinding with an angle grinder. There are YouTube videos on making anvils from a hunk of track.
I love the older DoAll bandsaws, I have two in my shop. One is a rather normal 3hp 36″ throat model which I usually keep a wood blade on, the other is a very special beast: It is only a 24″ throat but it has a whopping 7.5hp motor for the blade and a separate 2hp motor for hydraulic table tilt feed. It will also run up to over 10,000 feet per minute blade speed for friction cutting. It was previously property of the US Air Force. The table has T-slots like those on a milling machine so the workpiece can be secured to the table as it feeds into the blade. I use it exclusively for metal, but it has very neat “dial” feature which tells you what blade speed to use for what material, many of which are rather interesting. It has settings for cutting babbitt, asbestos board, armor plate, among more mundane things. The main thing I love about those DoAll saws is that they have a mechanical transmission with a gearshift just like in automobile. Thus when you run them at low speed they generate considerable torque. Many of the newer saws with variable-frequency drives are convenient to use but they lack power at low blade speeds. That’s fine if you’re just cutting wood, but thick pieces of plastic or metal can easily bog down those kinds of saws….not the case with the DoAll in low range.
There are lots of options for cutting metal these days – but when we acquired the pipe and metal fabrication business – the shop came with much old machinery – some dating back to WWII when the shop serviced aircraft manufacturers and the Navy. The old beasts form Armstrong Blum (Marvel), DoAll, Bridgeport, Baileigh, Walker-Turner and others required some TLC – but they were old-school heavy-metal machines built to last several lifetimes. I suspect that some of the newer machinery that we bought – may get retired/replaced sooner than the old. But laser, plasma and water jet cutting were not “things” during WWII and computers (primitive as they were) were given over to academic and military tasks not running CNC machines.
There are many more options these days but I feel that it’s hard to say that one is “better” than another. If I have to notch out a truck frame for 4×4 modifications you bet I’ll take the plasma cutter, it handles curves and strange angles no problem, and the fairly rough surface it leaves is moot since I’ll be welding onto it anyway. On the other hand if I have to cut out a blank before doing any machining I want to avoid anything which puts excess heat into the part (laser, torch, or plasma) because the rough flame-cut surface is incredibly hard on tooling, so something like a bandsaw, rotary “cold saw”, or a big slitting cutter on a horizontal mill makes a lot more sense. Modern CNC machines can do some amazing things but at the same time they are pound-for-pound weaker in my experience than an old school manual mill. Back when I had my machining business we had multiple CNC mills, but none of them could match the sheer metal removal rate of an old Kearney Trecker TF series vertical mill despite being roughly the same weight. The reason, as with the Doall saw mentioned above, was the old machines had serious gear reduction and could send a lot more torque to the cutter. They were heavier built as well. For example, my CNC mills had ballscrews about an inch and a quarter in diameter driven by servo motors; that Kearney Trecker had twin counter-rotating 2″ acme screws on each axis, with a 7.5hp feed motor connected to a manual gearbox for speed control. We had a Cincinnati Vercipower mill (Ex-Boeing) as well which was built to similar standards. It’s like comparing a bulldozer to a Corvette, totally different tools for totally different jobs. We used the manual machines for bulk metal removal so there was less work for the CNCs to do.
I would buy a cheap “deep cut” portable Band saw with good blades. 5″ x 5″ capacity. You’ll be amazed at the ease and safety with which you can cut thick steel, your railroad track should take less than 5 drama free minutes for a full cut. Most people also make a simple stand/ mount to use as a vertical bandsaw. VERY CONVENIENT. I use simple hooks to hang tool by the handle with spacers to keep tool level. Bandsaw – Harbor Freight and Wen have models that are often priced below 100usd. I personally have 3 used and ABUSED harbor freight models and have had zero problems, can’t speak for the wen but reviews seem very positive. Blades – I like the Bauer brand at Harbor freight, it’s USA made (I highly highly suspect made by morse), Lennox is another great option. Milwaukee blades, though still good, fall just below the above brands in my experience.
I have found that in general carbide blades last enough longer to more than justify the extra cost. I always keep some standard blades on hand though, for situations that might bend a blade or otherwise damage it. I’d much rather use a cheap blade in a sacrificial situation.
I liked the older Milwaukee blades pretty well but haven’t been so pleased with what they’ve had in the last few years. Their Axe carbide is good and those Wrecker blades will tear stuff up quickly, but the Diablo blades have proven to be both quicker and cleaner cutting, and seem to last longer for me in plastics and metals (generally using bi-metal….which I assume is what is being referred to above as “standard”). The only carbide ones that are worth a hoot to me are those for wood cutting….mostly poor results with anyone’s metal-cutting carbide except the one 20t carbide model from Diablo which did very nicely in cast iron pipe and seemed none the worse for wear after eight cuts. I’ve been gravitating toward Morse and Diablo for most toothed cutting since frankly the quality of all the big brands has suffered a lot. I have one Bosch recip blade (a wide 10/14 or something like that) but haven’t used that yet. They all get the job done for the most part. After Fred’s comment above I think I’ll have to pick up some packs of the Morse blades next time…still have a couple suppliers around here that stock only those and Lenox.
For years the “Ax” and the “Torch” blades were my go-tos but I agree the new Diablos are flat-out better. I still have a bunch of Milwaukee and DeWALT blades scattered around here and there, I’m still going to use them up but going forward the Diablos are going to be my choice.
I might try the ax pruning blade but as far as carbide on recip blades I don’t see the point other than excessive cost. Now I may also use my recip differently than most. but it mostly only comes out for demo work which leads to blade flex – carbide blades don’t like that. and they don’t work as well for me in the long run. put another way If I used 2 basic blades in the same task as I would work one carbide blade I’ve still come out money ahead. and changing blades out is not a tiresome task. I could see a case where if you did hard pipe or rebar daily all the time – a strong back carbide blade might live up to the hype but I don’t do that much. so when I do cut pipe again it’s a general metal blade usually
Good article. I wish the manufacturer’s would have guides posted in the tool areas to inform consumers which blade does what. I have learned through trial and error but I have also used guides for number of teeth on a blade and cutting what type of material. Just when your think you are well educated about the blades your using companies like Milwaukee come out with a new lineup that provides confusion. It is consumables so from a marketing standpoint “New” always keeps your foot in the door so it’s hard to blame the companies for that. I still struggle with Jigsaw blades occasionally especially since I seem to be always finding new projects to use the Jigsaw on for a more controlled or even a cleaner cut.
I would say Bosch does a decent job with their jigsaw blades. I’ve oddly never considered Bosch for a recip blade.
Reciprocating saw blades
Bi-metal unique reciprocating blades provide a comprehensive set of sawing solutions to professional trades people and do-it-yourselfers. The Starrett line includes straight and tapered.
high-speed steel saw blade Gleason, Heidenreich, Harbeck
Type: GLEASON HEIDENREICH UND HARBECK DESCRIPTION TYPE FEATUREN° PCS.CODEMATERIAL Spare blades for reciprocating motion gear cutters Gleason, Minganti, Heidenreich und Harbeck For roughing or.
jig saw blade 532300
Blade width: 8 cmBlade length: 19 cmBlade thickness: 4 mm. 30 mm
Cutting of hard wood, soft wood, plywood, plastic materials “Straight cut 5-blade blister pack Materials Hard wood, soft wood, plywood, plastic materials
sabre saw blade 22 2965 series
Blade width: 27 mmBlade thickness: 1.6, 2 mm
pull cutting upwards or downwards soft steels, steel profiles plastics chipboard Characteristic: hack saws produced of high efficient Swedish high speed steel, hardened and tempered to enable perfect.
jig saw blade 588400
Jigsaw blades set Version: Jigsaw blades for metal. For mounting on a single-cam shank.
jig saw blade HM 75/4,5
Functions carbide, cross-set teeth for abrasive materials Usage Main applications With carbide for longest service life even with abrasive materials Building materials Abrasive materials. For plaster- and cement-bonded.
jig saw blade BCH
composite material blocks can be cut into slabs with different thicknesses or into square blocks using the diamond gang saw blades. TYROLIT engineers advise customers on the correct installation of the.
jig saw blade 91-W
flexibility of carbon steel The sawblades are shatterproof and suitable for cutting through all types of material 5 blades packed on informative card
cutting saw blade Arix
Circular saw blade diameter: 115, 125, 150, 180, 230 mmBlade width: 2 mm
Arix Blue Sabre Blades This hybrid of the successful Blue Sabre Blade now has a new Arix style segment to give a fast cutting action togtether with an extended life. Dry cutting of Granite and Engineered.
reciprocating saw blade DT13
A reciprocating saw blade for cutting soft brick, lightweight concrete blocks, aerated concrete (AAC) and plasterboard. Tooth design: Tungsten carbide cylindrical teeth. Tooth pitch:.
jig saw blade 2315
Very suitable. Hardwood, Terrace wood, Wood core chipboard, Kitchen worktop, Plastic Shank version. T-shank Material. HSS Tooth shapes. conically ground Tooth spacing. 2.5 mm Cutting depth. 5. 30 mm Working lengths.
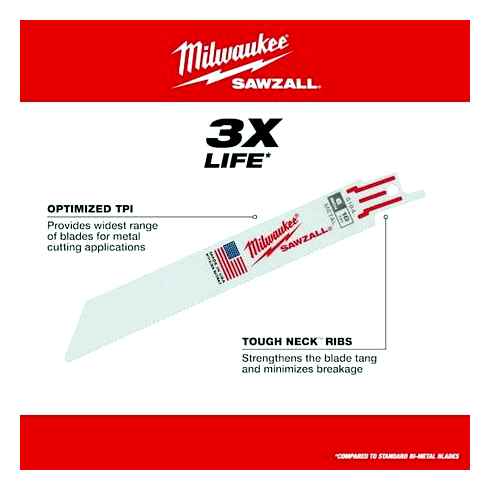
jig saw blade 7202 series
XTREME RECIPROCATING SAW BLADES Bi-Metal with Cobalt Demolition Saw Blades are extra thick for heavy duty cutting and long life.
jig saw blade L000M
Blade width: 8 mmBlade thickness: 1 mm
Features Milled and wavy set teeth. Flexible blade. Steel sheets, steel profiles, stainless steel (1,2-2 mm). Materials Sheet, steel, shaped, tube
sabre saw blade GOLD /h3>
Blade width: 11, 19, 25, 22 mmBlade thickness: 1.3, 0.9, 1.07, 1.6 mm
extending the life of the blades. The LENOX Gold Power Arc Curved Blades are available for a wide range of applications. LENOX GOLD POWER ARC CURVED WOOD RECIPROCATING SAW.
jig saw blade JT119BO
Blade thickness: 2 mm. 15 mm
Curve cut on softwood from 2mm to 15mm (5/64″~19/32″), plywood, OSB.
sabre saw blade
REMS special saw blade – for right angle sawing and for fast dismantling of steel pipes with power transmitting guide support. Special saw blades.
sabre saw blade Real McRipper
The Real McRipper Demolition Recip Blades Another Morse original. Specially designed for the toughest demolition jobs. Cuts all wood, nail-embedded wood and metals. Extra wide, extra thick blades for.
hack saw blade
pneumatic and electrical machines for cutting steel profiles, plastics and chipboards. SPECIFICATION TYPE Sabre hacksaw blade BLADE TYPE one-sided MATERIAL HSS TEETH PER INCH 8,10,14,16 PIECES.
reciprocating saw blade 33189 series
Blade length: 152 mm. 305 mmBlade thickness: 1, 0.9, 1.6 mm
Height 18.0 mm Net weight 0.28 kg Technical data Coating. uncoated Tooth type. crossed and milled
jig saw blade 32188 series
Height 12.7 mm Net weight 0.026 kg Technical data Coating. Black surface
jig saw blade 32 series
Blade length: 100, 117, 132 mmBlade thickness: 1.3, 1, 1.5 mm
Height 6.4 mm Net weight 0.032 kg Technical data Coating. uncoated Material. HCS Tooth type. ground
reach your clients in one place, all year round
Filters: find the right products faster. Terminology: use the most common industry terms. Brands: a wider selection. Products: to improve the relevance of the collection. Other
Receive updates on this section every two weeks.
Please refer to our Privacy Policy for details on how DirectIndustry processes your personal data.
With DirectIndustry you can: Find the product, subcontractor or service provider you need | Find a nearby distributor or reseller| Contact the manufacturer to get a quote or a price | Examine product characteristics and technical specifications for major brands | View PDF catalogues and other online documentation
are pre-tax. They exclude delivery charges and customs duties and do not include additional charges for installation or activation options. are indicative only and may vary by country, with changes to the cost of raw materials and exchange rates.
Reciprocating Saw Pruning Blade – How to Choose the Most Suitable
It does not matter if you are a seasoned professional or a lowkey DIYer.
Your knowledge ranges from selecting, operating, and maintaining it. When it comes to reciprocating saw pruning blades, it’s not just about pruning flowers or the landscape right? Well, it is certainly more than that. The various types you can choose from ranges depend on their applications. Be it wood, metals, PVC piping, and bushes. There is always a specialized blade.
So knowing all there is about your reciprocating saw pruning blade is key to getting the most out of it.
Chapter 1: What are the Reciprocating Saw Pruning Blade and its Type?
You have a Reciprocating saw. It is an essential tool to have because it cuts through anything, sometimes it is called “Demolition Saw” as it cuts through any material, hard and tough.
However, with the ranges of things it can cut through, you can not do it without a blade. No matter how expensive the reciprocating saw is, there is no good blade, and it is useless. Its blades are reciprocating saw blades. The reciprocating saw trim blade can also have a rubber handle. And it can be trimmed without a reciprocating saw.
Generally, there are two types of reciprocating saw blades: The toothed blades and the abrasive blades. They both serve different functions. Toothed blades can cut through soft materials, like wood and plastic, which makes it your ideal blade for pruning whereas. The abrasive blades grind through hard materials like stones, concrete.
However, finding the best blades for pruning trees does not end with just choosing a toothed blade reciprocating saw pruning blades. It also includes you doing blades attribute comparison. These attributes include size, coating, and more.
So when picking a reciprocating saw pruning blade, choose a specialty blade that has deep gullets and with a tooth configuration that allows it to cuts on both push and pulls strokes. This property allows the pruning blade to leave a clean cut in greenwood.
However, choosing is not something you master in a day. You only become good at it by constantly doing it.
Chapter 3 : Why Reciprocating Saw Pruning Blade Best Suited to Trim?
Pruning or cutting trees is some easier task than cutting metals or other materials. There are various other pruning tools you can work with, but none offers the top quality level of the reciprocating saw pruning blade.
Sometimes, it’s not always about you just finding any pruning tools. It is about you getting the right one that fulfills your tasks to with the quality you so desired.
It is why you need the reciprocating saw pruning blade. It allows you to cut through thicker tree branches with very little effort, unlike any other pruning blades.
There is another factor that makes a reciprocating saw pruning blade ideal. It should allow you to cut on both push and pull stroke. It should be quite efficient that other pruning tools and allows you to get the job done in lesser time.
For clean wood cutting, your choice of reciprocating saw pruning blade should have the most aggressive TPI. It could be as low as three teeth per inch. It comes with an aggressive tooth geometry that allows you to go through wood quicker than any other blade.
Also, it is very helpful when trimming shrubs. However, when working on nail-embedded wood, ensure that the reciprocating saw trim blade has a 5-7 TPI. It ensures that the nail does not enter the groove that can tear the blade teeth.
Another ideal factor that makes reciprocating saw pruning blade good for pruning is its length. Long blades can trim trees or cut wood for easier landscaping.
Chapter 5 :Why You Should Buy From Us?
We are trailblazers in the saw blades industry. And provide a full range line of reciprocating saw pruning blades each allowing you to prune trees, trim bushes, and shrubs.
Our reciprocating saw pruning blades are specially designed and configured for specific pruning purposes. It provides greater flexibility, durability, and performance than many other pruning tools. These disruptive reciprocating saw pruning blades makes a seasoned pro achieve more productive results and non-pro achieve desirable results.
None of your pruning tasks is too big, all you require is a reciprocating saw. over, you can get a high-quality reciprocating saw pruning blades from us.
With our competence, we can provide a demanding market with high-performance reciprocating saw pruning blades that are far more productive and superior to many others.
Contact us today and let us know how to choose the right product for you.
Summary :
By now, you should be wary of the various tools available for pruning tasks.
If you are to pick a reciprocating saw pruning blade that is durable, flexible, and efficient, you need to consider factors like blade material.
While shopping for a reciprocating saw pruning blade, take your time and choose well.
However, to get quality reciprocating saw pruning blades that allow you to get the most of it and are affordable, please contact us.Let us make your pruning dreams come true.
Tool Box Buzz
Browse all brands »
Browse all categories »
Home » Latest Tool Reviews » Tool Accessories » Milwaukee Ax Carbide Sawzall Blade
Milwaukee Ax Reciprocating Blade
A reciprocating saw, used in construction and demolition work, achieves its cutting action through a push-and-pull (“reciprocating”) motion of the blade. This type of saw, is also known as a recip saw, or Sawzall.
65 years ago Milwaukee invented the reciprocating saw, and since then, SAWZALL is a name that has been synonymous with reciprocating saws. The name says it all, actually. “Sawz-All”
A tool and a blade meant to cut everything!
According to my friend Scott, a tool like a reciproacting saw, is just an expensive “accessory-holder.” Seriously though, there is truth in that a power tool is only as good as the accessory you’re using!
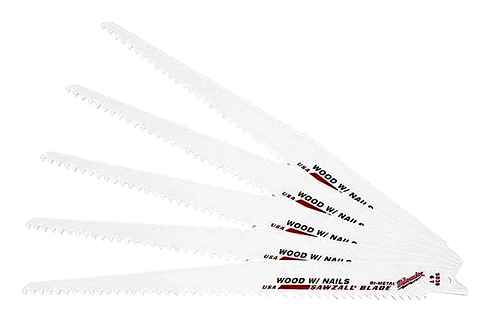
Reciprocating Saw Blades
That brings me to the topic of Sawzall Blades. A recip-saw blade may not have to work that hard in new construction, but on a remodeling site it undergoes a real-life torture test, cutting roofing, nail-embedded wood, pipes, stucco, plaster, fiberglass, drywall and anything else that needs to be removed or cut.
It’s relied on to be aggressive and fast cutting. We all know that when it comes to extreme cutting applications and versatility in a wide range of materials, carbide blades last longer.
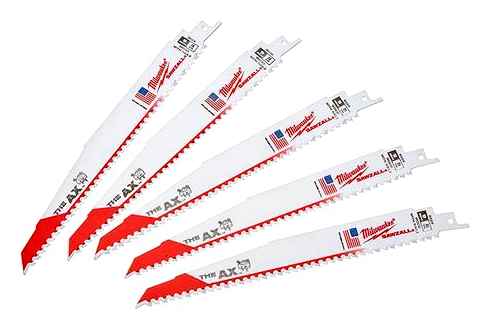
Milwaukee Ax Carbide Recip Blade
Reciprocating leadership, in my opinion, is defined by the performance in the recip saw blade. Milwaukee’s new Ax blade is “leading the pack,” with its cutting edge technology.
Milwaukee engineered a completely different process, material and technology to deliver a blade that could meet the very demanding requirements of the Sawzall.
The Ax Carbide Teeth Sawzall blades are engineered to be the longest-lasting, fastest cutting carbide-tipped recip saw blades on the market.
Milwaukee Nail Guard
The Blades feature a Nail Guard tooth design to prevent nails from fracturing the blade’s teeth upon impact and an aggressive 5 TPI design to deliver fast cuts. Blades with a low TPI deliver faster cuts with rougher edges and are ideal for cutting wood.
Milwaukee Fang Tip
This Fang Tip design bites into the wood on first contact to make the cut. A pair of unique, fang-like teeth and an extra-large gullet deliver a fast plunge cut.

The combination of these features allows you to cut through a wide range of materials without sacrificing the life of the blade and with less blade changes.
Other wood-cutting carbide blades have had to sacrifice speed for durability, or durability for speed. Milwaukee has found a way to deliver both of these without having to make that compromise.
Testing The Milwaukee AX Blade
I wanted to be able to show you the long-lasting, fast cutting capabilities of this blade.
At the same time I wanted challenge the blade with a realistic test that would challenge every blade, not torture it.
I chose not to use stainless steel, hardened fasteners, or cement board, because those materials are not often cut during remodeling and demolition work.
Nail-embedded wood is key here, and what we cut the most of. I constructed two realistic test boards:
I sandwiched two 2x6s on edge, glued up with a layer of plywood in between and capped with outer layer each of drywall and plywood. This was to simulate a residential wall / window header construction.
This test board contained rows of nails, laid end-to-end in saw kerfs cut into the 2x6s: I embedded 16d commons, 10 D commons, and 8d common nails. By locating the nails along both sides of the center piece plywood, I was able to concentrate wear on a limited number of blade teeth. In order to simulate a residential wall detail I added a layer of 1/2-inch CDX plywood and 1/2-inch drywall.
p.s. – next time someone remind me that drywall makes dust. My shop was a mess!
Since cutting openings for skylights and vents is a common remodeling task, I designed a test to mimic that operation on a three-layer roof. The test consists of six asphalt shingles between two 6-inch rips of ½”-inch MDO plywood. The second layer of MDO was to hold the shingles in place.
Milwaukee AX Saw Blade Test Results
The Results Speak For Themselves. First of all, I was impressed by the longevity, toughness and variety of material that this blade can cut. If I could only buy one blade, this baby is one that could cover most of my needs.
I will note, that there was a point where I terminated the test. The blade continued to cut, and cut, but it was obvious to me that it was dulling and slowing down. If you follow my site ConcordCarpenter, you know I’m big on efficiency. I terminated the tests where I did, because this was the point where I would have changed the blade out.
There are a METRIC TON of guys out there that would continue to cut with this blade … and cut it WILL DO! Just much, much slower.
So How Did I Do With Just ONE Ax Blade?
On the simulated header / wall we made 45 cuts before the blade started slowing down. I also noticed 2 teeth broken.
- 90 2×6 cut
- 45 plywood cut
- 45 drywall cut
- 360 – 16d nails cut
- 90 – 10d nails cut
- 270 – 8d nails cut
- 30 cuts through 6 layers of 3-tab shingles
- 30 – 3/8″ rebar cuts
On the Simulated roof cutting we made 30 cuts and the blade continued to cut effortlessly, with no sign of slowing down. So we moved onto something a bit harder to cut. We pulled out some scrap 3/8” rebar proceeded to made 30 cuts. At this point due to my arms and shoulder aching, I terminated the test – the blade was significantly slower but still cutting.
Inspection of the blade at this point indicated 2 to 3 additional broken teeth. If I were in the field I’d have replaced the blade by now – but remember, some guys don’t!
Milwaukee AX Saw Blade – Overall Impression
Let’s Cut To The Chase, these reciprocating saw blades provide fast, aggressive cutting on a variety of materials!
Milwaukee claims that this blade can make more than 1500 cuts in nail-embedded wood, and I absolutely believe it, after putting it through my wall/header/nail cutting rig.
Not only that… they also claim that this blade, which is designed for wood-cutting, is also capable of cutting through a wide range of other materials if needed, like rebar, hardened fasteners and steel. I believe that as well, since I made 30 cuts in rebar with a dull blade.
I really like that Milwaukee continues to develop innovative ideas and designs with unparalleled performance reliability – it certainly makes a huge difference in what I do.
What Could This Mean?
The bottom line is these carbide teeth Ax blades will allow you to be more productive, work faster and smarter with cutting applications.
Sometimes it’s the small details that make a big difference, and this means that your sawzall will be better equipped to … SAW-ALL!