Exit | the | Fast | Lane |. Table saw extension rails
Jobsite Table Saw Router Extension
The same basic principles outlined here can be applied to a cabinet saw as well, but this post focuses on the portable jobsite variety. That tenet, portability, is largely why a table saw router insert makes so much sense here. I really don’t want to take up even more precious space with a dedicated router table, plus this way I can easily move and deploy two important tool stations with one action. Ah, the life of the driveway wood worker! My table saw and router are both Bosch models which happen to be best-in-class contenders for these particular tools. Just about everything else in my tool chest is DeWALT but these Bosch models were very deliberate purchases based on overwhelmingly positive community feedback. I can personally attest, the hype is real.
Core Components
The jobsite saw I’ll be modifying here is the Bosch 4100-10 (10” Gravity-Rise Worksite Table Saw). My plan is to remove the right side extension table and replace with a custom router insert: Link
Best Circular Saw Guide Rails 2023 || Top 5 Circular Saw Guide Rail Review
The only non-standard feature I added to this saw initially is the Bosch Outfeed Support Assembly which doesn’t interfere at all with my router extension insert. There is also a left side outfeed assembly which I may add at some point later: Link. My general feedback on the outfeed quality and functionality is very good, although you waste a bit of the shipped components since Bosch packs parts for two different saws: Link
My router is the Bosch 1617EVS which is a variable speed model generating 2.25 HP @ 12 amps. I purchased as a kit that includes both a plunge and a fixed base, along with collets for both 1/4” and 1/2” bits. The fixed base is what I used to attach the router to the insert: Link
Here is the end result, want to see how I built it? Keep reading:
Parts List
- 3/4” MDF half sheet: Link
- Rockler Pro Plate (Model A): Link
- Amana 5/8” straight cut bit: Link
- PowerTec T-Track (2 x 24”): Link
- PowerTec 5/16″ T-Bolt kit: Link
- 4 x 5/16″ zinc carriage bolts washers
- 2 x 5/16″ 3-prong T nuts (for plate)
- 12 x stainless flat head screws
- 1 x 1/8″ x 2″ steel bar
- Minwax fast-drying oil-based poly: Link
- Minwax Past Wax: Link
- 3M Rugged Comfort Quick Latch Respirator 6503QL: Link
- 3M 2097 P100 Particulate Filter Pair: Link
- Titebond III wood glue: Link
- Dasco Pro Cold Chisel kit: Link
Cuts and Prep
Why MDF you may be asking? A couple of reasons, first it’s relatively cheap, it’s super easy to work with having no grain pattern as it can be cut in any direction, it glues up strong very nicely without need for fasteners and lastly it’s dead flat which is important for this particular use case. The image below shows the 5 parts for the fence which will attach to the stock Bosch table fence directly. Plus the triangular supports and the support plate to round out the cut list. The general idea here was to create an insert that sits between the table slide rails and a fence slightly larger than the width of the table. This is 100% custom and can be applied to any other similar jobsite saw.
One quick note on working with MDF. Unless you have a stellar air filtration system you really need to wear a respirator. The MDF fiber particles are extremely fine, much like powder and will get everywhere, especially into your nose and lungs. I linked the 3M gear I use above which works incredibly well for me on all woodworking projects.
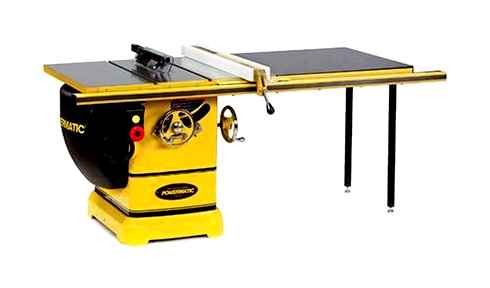
The cut image for the router plate got corrupted so sorry that’s missing, but you’ll be able to see in later photos what I did there. The length of the piece is from table rail to rail and I made it wide enough to house the plate, a handle cutout and a T-track rail.I used 6 support pieces on the underside which I’ll show a bit later.
Router Plate Insert
I chose the Rockler Pro Plate as its aluminum which is a strength upgrade from many of the molded phenolic you will find for sale. I read several anecdotal accounts that these molded plates will sag and warp over time due to the weight of the router. No thanks, do it right with a metal plate!
Once the basic shape of the insert is cut, I created a simple template to cut the indention for the Pro Plate. Find the location on the board you want to the plate to sit, then surround with identical height scrap, hold down with double-sided tape. You want these pieces tight as possible to the edges of the plate. In hindsight using MDF around all 4 edges would have been better but what I did worked out ok.
Remove the plate and insert a center square piece which will be used by the router to rest on as it completes its task. Some people leave only a very tiny lip around the edge when doing these. A bigger lip equals more strength but also you really only need enough clearance for the router and base itself. I’ll explain further just ahead. Set your plunge router at the exact depth of with width of your plate and route out the lip. Once the lip has been created, remove the center square and cut out the center piece of the board with a jig saw.
For the front T-track slot I used the plunge base with the Bosch Deluxe Router Guide. I HIGHLY recommend this part as a worthy addition to the tool box. The edge the guide glides on needs to be straight and true, if it isn’t, your cuts will be mirrored imperfections. For this step, I marked the depth I needed for my rails on the side of the work piece, then plunged the bit real-time to the proper depth.
I needed to do a little flattening of my lip to get the plate to sit perfectly flush. I really don’t want to mess with leveling screws in the corners but that’s ok if you want to. I found that hand scraping with a chisel was a good way to remove material. Sanding just doesn’t work very well with MDF and takes way too long. Check your level by using an MDF scrap sliding from the board surface over the router plate. If the plate is too high the scrap piece will knock on the edges. Keep scraping until perfectly flush.
Next I cut out the handle and pop-up notch to match the original extension wing that I removed from the table. Mark carefully, then cut out with the jig saw. I then softened the edges a bit with the rotary sander. This is similar to factory finish on the metal table edges.
Moving on to the underside. Next, I drilled holes in the side support pieces that will ultimately mate up with the bars to slide into the table rails. I don’t have a drill press yet so used a block of maple and walnut with a true 90 junction that I used to drill straight holes. In lieu of a proper drill press this works well.
Here is a look at the underside and how I did the support pieces. 2 for each of the long runs, 1 on each end drilled for the metal bar that will slide into the table rails with a bit of overlapping between the ends and side pieces. I used no fasteners here at all, just glue and clamps which worked extremely well with Titebond 3. One thing to keep in mind here is that MDF is highly absorbent, especially on the ends, so any glue cleanup that you would normally do with a wood glue up won’t work as well here. Some of the glue is going to get absorbed and won’t wipe up well. I had no issues with adhesion on the ends either. You will read that some people go to careful lengths via multiple glue coats to maximize adhesion when attaching MDF end pieces. I really had no need to do that.
Using my trusty router guide, I cut a clean edge on the 2 sides to match the cuts in the metal table top. Now the tricky part, lining up the bars to attach this thing to the table. With the insert in place and leveled, I slid the bars into the table rails and marked the holes from the underside for drilling. I also marked the bar length for cutting at this step which I did with my jig saw and a metal cutting blade.
With the holes marked I used my “drill press” and a drop of oil for the bit to drill holes. Make sure your bits can be used to drill metal!
Because I intend to attach the bar to the insert using carriage bolts, I need the holes in the bar to be square so they will sit flush. This part is rather crude but it worked. Using a cold chisel, I flared the corners on each side of the holes, then with the bar securely clamped in my vise I knocked each side flat with a 3lb hammer. The best way to do this is to line up the edge you want to remove flat just above the vise jaw. Good work out on this step. Be careful here because the cold chisel will put gouges in your vise!
Ok so I’m finally done making changes to the insert piece and can start on finishing. Using a 50/50 mix of mineral spirits and oil based poly, I saturated the entire piece as much as I could using an old sock, 7 or 8 coats at least. This thinning will cause the poly to soak deep into the fibers adding strength and resiliency. After this dries a few hours I’ll add several more coats then finish with a full strength coat a day later. Make sure to do some light sanding between coat sessions, 400 grit will do.
If you have the Bosch 1617EVS like me and want to use the Rockler Pro Plate, one small adjustment needs to be made to the plate. One of the cool things about this router is that the static base includes a height adjustment capability, built in. No need to buy one of the expensive (but awesome) JessEm router lift kits. But, unfortunately, the Pro plate doesn’t have a hole for the adjustment key, so you will need to drill one. Luckily this is aluminum which is easy as butter to work with. Here’s what I did to figure out where to drill the adjustment screw hole. I inserted screws into the 3 holes of the static base that will ultimately attach to the Pro plate. I then found a random screw of similar height for the adjustment screw and inserted that into the adjustment hole. Lining up the 3 pre-drilled holes on the plate, I was able to mark where the adjustment hole needed to go. Pencil around the screw head is all that’s needed here.
Mark the center of the hole with an auto center punch and drill the hole using a bit of the same diameter as the height adjustment tool that came with the Bosch kit. Aluminum is so soft you don’t even need to use oil to drill, but it won’t hurt anything if you do. That small lone hole below is mine.
Next I secured the Pro Plate to the insert using my pronged T nuts. Mark the location with the plate in the insert and drill to match the diameter of the nut. Insert from the bottom.
The plate will come with the right size screws in black for the corners. Screwing these in will tighten the pronged T nut from the bottom. I also cut to the T-track to length and screwed down with stainless flat head screws. I cut the track in a way to ensure the screw holes were as close to the edges as possible to secure a tight fit. Amazon Prime boxes make great work surfaces. 🙂
With the plate securely in place, I screwed on the slide bars to each end of the insert. You don’t want this fully tight yet, slide the insert on to the table first and square the rails.
Now, tighten the bolts of the new insert to the table rails. You can see that my insert deepened in color a bit after the poly coats. I also finished the piece with a coat of paste wax at the very end. What do you think?
Router Fence
On to the router fence, for which the pieces I already cut out. There are a lot of variations on this piece but what I wanted for sure was something adjustable that I could later add a feather board via T-track. The first step is to mock up the assembly and plan the slots that allow the front faces to slide. This needs to be done in conjunction with where you intend to place the supports, since your knobs that hold the front faces will come in contact with the supports. Find 2 spots on the front faces to drill holes, then with bolts inserted, plan how you want the slots to lay out and mark. Here I cut the slots already but hopefully you can see what I mean.
Once the slots are cut and support locations planned, countersink the bolt holes of the front faces so they won’t interfere with any future work pieces.
Next I dealt with how to attach the custom router fence to the Bosch saw fence. Unfortunately the side slot on the Bosch fence is not a standard T track slot and I couldn’t be bothered to run to the blue/orange store, so I cut two of my T track bolts down to size. Dremel cut off wheel to the rescue.
With the head squared a bit I was able to fit into the side slot. From here you just need to decide where to punch the holes in the MDF piece that will sit adjacent. I centered my piece and marked for holes near the quarter-mid of each side. 2 bolts is good enough for this.
Due to the height of the slot in the Bosch fence in relation to the table, I really had no choice but to cut a notch to clear the adjustment knobs. I got the smallest I could find so to limit the depth of the notch I’d have to cut. A few bangs of the chisel and presto.
With slots cut and holes drilled I felt good enough for another glue up. Both of the vertical pieces sit on top of the bottom piece which will ultimately sit flat on the saw table. You can also see how I marked the holes to center the bolts from the Bosch fence to my rear piece.
While I glued on the fence face T-track carrier (upper portion of front fence face) I measured and cut supports. I wanted the triangular parts of these as flat as possible for the middle supports just in case I ever want to add a dust collection port.
With the supports cut, time for more glue, more clamps.
I let the glue harden overnight then moved on to another 50/50 poly/mineral spirits soaking. I honestly lost count of how many coats I did, I just kept soaking until my mix was gone, hitting the exposed edges especially hard.
I let this cure overnight again then did one last pure strength poly coat following a light sanding. After one last overnight curing I bolted on the front faces and screwed on the upper T-track.
Here’s a look at the “knob chamber” so you can see each in relation to the slots and the supports. It’s a little tight but plenty of room to move things around without collision.
There you have it! The project before the “project”. Let me know what you think or if I can answer any questions. Thanks for stopping by!
Table saw extension rails
Harvey Industries International
10832 Ada Ave.Montclair California91763 United States
Follow us
- American Express
- Apple Pay
- Diners Club
- Discover
- Meta Pay
- Google Pay
- Mastercard
- PayPal
- Shop Pay
- Venmo
- Visa
- Choosing a selection results in a full page refresh.
- Press the space key then arrow keys to make a selection.
- Use left/right arrows to navigate the slideshow or swipe left/right if using a mobile device
Let customers speak for us
I was very pleased with my purchase of 4 Harvey machines. Everything arrived without a scratch, the packaging is well engineered. All the assembly was straightforward and the quality of the parts, assemblies and accessories is first rate. I configured the tablesaw the way I wanted with an overhead guard and dust system (the shark), sliding table and rear table. I was pleasantly surprised to see that all the mounting holes were already there for my accessories. Even the fence rails came drilled for my choice of configuration. No drilling required. The miter gauge is the best I’ve ever owned. The bandsaw works great, even resawing thin strips from 5″ stock. The shaper is a great buy as well, all accessories included for shaper cutters, router bits, etc. The fence and the guards are easy to precisely adjust and my G700 dust processor is amazing. No more all day clean-ups! I’m picking up my lumber to start my boatbuilding project next week. Can’t wait to get started!
Bandsaw seems well built. Like the coated. Table adj screws are a bit of a pain as levers can’t rotate 360,knobs might be better choice. Time will tell after getting setup. Customer service has been great. No long hold and you talk to a person.
Over all, this is truly a fine saw. Solid as a rock and powerful. Two issues that have risen. There is no place on the saw to store the wonderful crosscut tool. It is large and very well made but I am going to have to make a storage rack for it on my wall. Additionally, the attachment with the line to establish rip width won’t lock and keeps moving. I am sure this can be replaced by the company although I haven’t called them yet. So far their customer service has been excellent so I expect this will be solved rapidly with minimal stress.
this is an excellent dust system! Much better fit and finish than expected. I’m very satisfied with the performance. Two improvements would make this outstanding. Put the power switch on the same side as the controls and make the remote able to adjust the fan speed. Thanks for a fine product. Wayne
As usual the Harvey Woodworking equipment is well thought out, well made and priced to sell. The features and function of this miter guage are far above any other miter guage available. Stock guages from Powermatic, Jet or others are far below the quality, utility and function of Harvey Woodworking tools. Across the board.
This tool is of supreme quality. All parts are manufactured well and of very heavy grade materials. Above and beyond the likes of powermatic, jet, laguna etc. I have a full compliment of excellent equipment from those makers and the Harvey brand stands out among them as being above and beyond. Next stop- Harvey Alpha tablesaws.
The SHARK S-12S is a sturdy and impressive tool that effectively reduces dust accumulation. Its swiveling feature and movable guard unit make it user-friendly, although the frame and wheel may limit visibility under the dust shroud. However, this is not a deal-breaker, as you can adjust to viewing from the side of the transparent shield. Speaking of the shield, it has saved me during one of my projects when a kickback occurred while cutting maple. The Shark S-12S took the brunt of it, and I wasn’t injured. Upon close inspection, there was no noticeable damage to the Shark S-12S from the kickback.
I have an older 2hp dust collector that efficiently handles the dust produced by my table saw. However, I hope to upgrade to the Harvey GYRO AIR G-700 someday to complement the Shark S-12S system.
I also own a Harvey Alpha Table Saw equipped with a 32″ INCRA TS-LS Rip Fence System. To mount the Shark S-12S onto the fence, I had to devise a secure and functional mounting solution that did not require drilling into the Incra. Fortunately, I found an alternative solution that did not compromise the integrity of the Incra.
Despite its limitations, the Shark S-12S is an excellent investment that outperforms the original dust guard. It reduces the amount of dust in the air and protects against kickbacks, making it a worthwhile purchase.
The slide saw attachment works amazing. It makes your table saw so much more versatile. Well worth the price. Just wish I bought it sooner.
The table saw is a most welcome upgrade and I wish I’d done it sooner. Some particular features I like is this effortless nature of the motor, cutting through oak and walnut with no strain. The fence. for me. is an exceptionally important part of any table saw and the ability to adjust it, and to be certain it isn’t moving under the stress of forces is critical. This saw was clearly made with delicate as well thick lumber in mind. The fence moves back also to allow for larger pieces and it has a view finder measurement for the fence in the high or low position which is exquisite. Having a machine that allows calibration every now and then on almost all aspects from the fence to the riving knife is very welcome. Precision means saving time and not wasting material. For the work I do precision is critical and this saw saves me wasted material and gives precision cuts the first time. I’ll probably buy another one next year. When dealing with materials in excess of 8 feet, only precision is acceptable.
After doing a lot of research and saving, I decided to go with Harvey. I waited for a sale and have no regrets. This saw has power, is accurate, and has a great fence. Super easy to set up. Thanks for a great product!
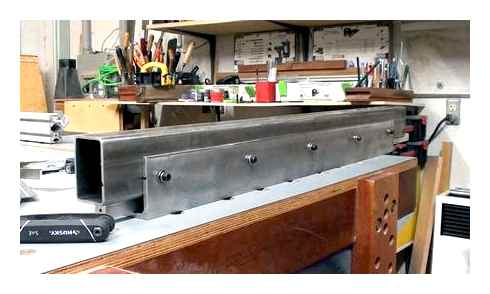
Table Saw Fence
Through the years I’ve worked with a number of table saws, from my dad’s venerable Craftsman to a Delta Unisaw to the portable tablesaw I used when I was in construction. The one thing I learned through all this, is that the fence is the most important part of any table saw.
Now, I know that there are people who will disagree with me, and I’m not talking about safety measures such as using the push stick. Most of them will say that the blade and the blade drive are the most important part. But, while I agree that they are important, I don’t think they are more important than the fence. If there’s a little bit of wobble in the blade, due to a poorly designed or aligned drive, it will mar the finish of the cut. But if the fence is off, the cut will be crooked. That’s a bigger problem to deal with.
But not all fences are created equal. Far from it. If there’s one thing I’ve seen through all the table saws I’ve used, it’s that there are a lot of poorly made table saw fences out there. If you’ve got a saw with one of the bad ones, it’s going to affect every cut you make.
There are two things you can do, besides just putting up with it. The first is to buy another table saw; and the second is to build yourself another fence. While there are some fairly complex fence designs out there, you can actually make one fairly easily, which will provide you with excellent service. But first, there are a few key things that you need to keep in mind, when designing and building any table saw fence:
- Perpendicularity – The key thing that any fence has to be able to do is maintain perpendicularity with the saw’s table. Another way of looking at this is that it has to remain parallel to the saw blade. Poorly designed table saw fences don’t have enough of a crossbar for the “T” portion of the fence, causing it to have a tendency to wobble.
- Rigidity – Any table saw fence is only going to work if it can maintain rigidity. It can’t flex under the pressure of material being wedged between it and the saw blade, especially if the cut starts to go crooked.
- Security – When you clamp the fence in place, it has to stay there, no matter what. Just as with rigidity, there are times when the material between the fence and the sawblade will push against the side of the fence, trying to move it. That can’t be allowed to happen.
- Ease of Use – Any fence which is hard to move and clamp in place is not going to be used. This is why commercially manufactured fences have an over-the-center clamp. That’s fine, if you’re making it out of metal, but a wood over-the-center clamp is only going to last so long. Therefore, I’ve chosen another design.
For this design, I’m using a combination of wood and aluminum extrusions. The fence itself, the part that guides the wood, is made of wood, but the “T” head and the rail are made of aluminum. That allows me to take advantage of the strengths of the two materials, applying them where they will do best.
Making the Fence Rail
For the fence rail, I’ve chosen a 12 gauge piece of 1-1/2” square “C” channel. This is the same sort of channel that you might see used for the rail on a horizontal sliding door in a factory or a gate. Normally, these are made of steel, rather than aluminum, but I’ve gone with aluminum for weight. If you can’t find this material in aluminum, you can just as easily make it out of roll-formed steel.
Typically, a fence rail is the width of the table, but I’ve extended it six inches beyond the edges of the table on both sides. This ensures that my fence will still maintain perpendicularity, even when at the extreme edges of the table. If you were planning on building extensions onto your table saw table, I’d do that, before building the fence, or make your fence long enough to accommodate those, while still extending past the edges of the table.
The saw’s table should already have holes drilled and tapped into the front edge, from the original fence rail. You should be able to use these same holes, if you remove the existing fence rail. If there are not enough, you may need to drill some additional holes. As the table top is probably made of cast aluminum, this should not be a problem.
Table Saw Fence: 5 Best Cheapest Table Saw Fence Reviews | Top Table Saw Fence (Buying Guide)
Be sure to mount the guide rail so that it is slightly below the surface of the table, to ensure that it will not hold the fence off the surface of the table. Also ensure that it is perfectly level or parallel to the surface of the table, so that the fence doesn’t ride up and down, vertically, as it moves across the table.
Building the Fence
I’ve chosen to use MDF (medium-density fiberboard) for the fence itself. Another good option would be applewood plywood if you can find it. The thin plies of the applewood are perfect for this sort of project, and it is extremely stable. That stability is why I chose MDF, which is easier for me to get.
The fence itself is made of four, Âľ” thick strips of MDF. all 3” wide. Because I am working with a fence that is not all that reliable (the one I’m trying to replace), rather than count on the fence’s clamping system for perpendicularity and security, I clamped the existing fence in place with two C clamps, one at each end, after checking the distance and the perpendicularity with a square.
In the diagram above, you can see how the four strips of MDF are connected together, to form the fence. These were glued together and nailed, with brads and then screwed for extra strength. To ensure that the screw heads would not protrude from the surface of the fence, the pieces were drilled (clearance holes only) and countersunk before assembly. Once glued and nailed. The pilot holes for the screws could then be drilled and the screws driven home.
I chose to make both sides of the fence equal, so that it could be used either right-handed or left-handed, although I do most of my cutting with the fence to the right of the blade. I could have also done basically the same thing, using a 2” x 4” aluminum C channel, rather than the two middle strips of MDF, but this would have required buying one more type of aluminum extrusion, adding to the project cost.
I also chose to make the fence overly-long, just as I made the rail overly wide. My table saw has a support extension behind the table, so I made the fence long enough to reach this support, even at its longest extension. This increases the surface I have available for the workpiece to ride against, helping to ensure that I run it through the saw straight and evenly.
The aluminum angle, shown in the drawing above, forms the “T” head of the fence and is bolted to the bottom of the fence. I would recommend using three to four bolts, for security, along with nylon insert locknuts. After all, this is the most critical part of the assembly, as it needs to be exactly perpendicular to the fence.
To check perpendicularity, use the fence, with the T head attached, as a square to mark a line on a piece of sheetrock or plywood. Then flip the fence around, putting it on the other way. If it is exactly square, when you mark the line from the other side, it should exactly overlap your original line.
Making the Locking Mechanism
In order to make the fence easier to build, I’m using a knob and screw as a lock, rather than an over-the-center lever mechanism. Not only are those harder to build, they must be extremely precise to work properly. A screw and knob on the other hand is something easily accomplished in a home workshop.
Before we look at the locking mechanism itself, we need to talk about the “T” head for the fence. Opinions differ, but most good fences have a head that is about 1/3 the length of the fence. I would modify this by saying that your head should be at least eight inches long. However, unless you have a huge saw table, any longer than a foot will be difficult to work with. Be sure to radius or chamfer the corners of the aluminum angle you use for the “T,” so that you don’t injure yourself when you run into it.
The locking bar, which goes inside the fence rail, should be roughly the same length as the fence “T.” You can make it out of whatever material you have available, but it should be at least ÂĽ” thick and able to support being threaded, without the threads pulling out. This pretty much limits us to aluminum or steel.
As you can see in the diagram above, the locking mechanism consists of nothing more than a bolt with a knob attached, running through the T head and into the fence rail. On the inside, the bolt goes through the locking bar. To lock the fence in place, all that is needed is to tighten the knob, once the fence is positioned.
You need to be sure that you use a good knob or knob/screw combination; one that won’t come apart as torque is applied to it. I would also go for the largest thread size that you can reasonably fit through the opening in your frame rail. If you can get it, use fine threads, as that will be easier to work with. You can buy these through industrial supply companies, rather than trying to buy one at your local hardware store or home improvement center.
You will need to drill and tap the locking bar to match the thread of your knob/screw. If necessary, cut the knob/screw to length, and grind a chamfer at the end of the bolt. You want it to go all the way through the locking bar, but you don’t want it to be able to hit the bolts that are holding the fence rail to the table saw table.
One last item that is needs is a spacer for the knob head to press up against, when it is tightened. This must be made of some sort of metal, as the tightening of the knob will try to compress it. If you use plastic, for example, it will crush and your fence won’t be secure. Placing a washer between the knob head and this spacer, to act as a thrust washer, will help it to tighten and loosen a bit smoother.
s:
- Wooden Fence with Metal Post by Admin November 25, 2020 DIY Most home fences are either wood or metal. Wood fences, often called “privacy fences” are usually made of cedar pickets, attached to 2”x 4” rails,…
- Amish Fence Puller by Admin May 4, 2021 DIY Installing any fence can be a lot of work. Many people avoid it, because of that. Even more, they’ll avoid putting in wire fences, whether…
- Pressure Treated Fence Posts by Admin July 29, 2021 Installing Building any style of wood fence pretty much requires using wood fence posts. These are usually pressure-treated 4”x 4”s, sunk into the ground and often…
Table Saw Router Table Tops
All INCRA Router Tables are shipped with a 3/8″ solid aluminum router mounting plate, pre-drilled for your router, featuring the exclusive MagnaLOCK Magnetic Reducing Ring System. Changing any of the included throat plates is a snap with the MagnaLOCK System. Just drop in the selected ring and the high energy, rare-earth magnets hold it securely and perfectly flush every time. The rings have their own leveling system within the plate. All of our router mounting plates include 3 laser cut rings with 1″, 2-1/8″ and 3-5/8″ openings.
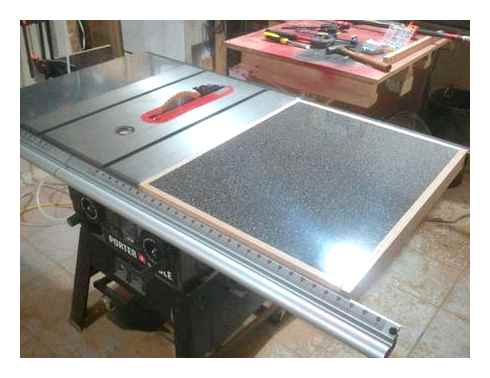
Rather than the typical router plate leveling set screws that dig into the table‘s recess requiring constant re-adjustment, INCRA’s plate leveling system puts 10 large flat head levelers into the table itself for excellent support. Convenient access to these levelers is through the 10 access holes located around the perimeter of the mounting plate, and after leveling, a simple quarter turn of the corner mounted Cam-Lock securely holds the plate in the router table‘s recess.
Available in 4 models designed specifically for the INCRA TS-LS and TS-III table saw fence systems. All table saw based router tables include the TS Router Table Support Kit with 4 brackets and 2 table stiffeners. The brackets can be positioned anywhere along the INCRA TS System’s rail length and are vertically adjustable.
INCRA 28″ x 21″ TS Router Table Top with Router Mounting Plate Hardware
INCRA 28″ x 21″ TS Router Table Top with TSRTHW Part Number: TSRT2821L more info
This 28″ x 21″ router table replaces the left-side extension wing on the saw. Its size is appropriate for saws measuring 27″-28″ deep along the miter slot, and it allows working at the more open left end of the saw for plenty of routing capacity and easy access around the router table.
Requires the use of an INCRA TS-LS or TS-III table saw fence system. Not compatible with cabinet saws that have motor housings on the left side of the saw. check the Compatibility Chart for more info.
Note. This table is not compatible with the unique Mast-R-Lift-II-R sold by Rockler, which uses a narrower 8-1/4″-wide top plate.
Router plate size: 9-1/4″ x 11-3/4″ x 3/8″
INCRA 28″ x 32″ TS Router Table Top with Router Mounting Plate Hardware
INCRA 28″ x 32″ TS Router Table Top with TSRTHW Part Number: TSRT2832R more info
The 28″ x 32″ Right-hand table serves double duty as a work surface extension and includes a full size 3/8″ x 3/4″ T-Slot Miter Channel. This table is for use with saws measuring 27″-28″ deep along the miter slot. This table allows 5″. 7″ of routing capacity without moving the TS system’s base assembly on the rails, and the fence system can be reversed if more capacity is needed.
Requires the use of an INCRA TS-LS or TS-III table saw fence system. Not compatible with cabinet saws that have motor housings on the right side of the saw when used with 72″ INCRA rail sets. check the Compatibility Chart for more info. TS Rail Support Legs highly recommended.
Note. This table is not compatible with the unique Mast-R-Lift-II-R sold by Rockler, which uses a narrower 8-1/4″-wide top plate.
Router plate size: 9-1/4″ x 11-3/4″ x 3/8″
INCRA 32″ x 21″ TS Router Table Top with Router Mounting Plate Hardware
INCRA 32″ x 21″ TS Router Table Top with TSRTHW Part Number: TSRT3221L more info
The 32″ x 21″ Left-side router table permits maximum fence system range and offers open access from the end of the table saw by sliding the INCRA positioner assembly down the rails. This table replaces the saw’s left side extension wing and is sized for saws with oversize cast iron tops measuring 30″. 31″ deep along the miter slot.
Requires the use of an INCRA TS-LS or TS-III table saw fence system. Not compatible with cabinet saws that have motor housings on the left side of the saw. check the Compatibility Chart for more info.
Note. This table is not compatible with the unique Mast-R-Lift-II-R sold by Rockler, which uses a narrower 8-1/4″-wide top plate.
Router plate size: 9-1/4″ x 11-3/4″ x 3/8″
INCRA 32″ x 32″ TS Router Table Top with Router Mounting Plate Hardware
INCRA 32″ x 32″ TS Router Table Top with TSRTHW Part Number: TSRT3232R more info
The 32″ x 32″ Right-hand table serves double duty as a work surface extension and includes a full size 3/8″ x 3/4″ T-Slot Miter Channel. This table is for use with saws measuring 27″-28″ deep along the miter slot. This table allows 5″. 7″ of routing capacity without moving the TS system’s base assembly on the rails, and the fence system can be reversed if more capacity is needed.
Requires the use of an INCRA TS-LS or TS-III table saw fence system. Not compatible with cabinet saws that have motor housings on the right side of the saw when used with 72″ INCRA rail sets. check the Compatibility Chart for more info. TS Rail Support Legs highly recommended.
Note. This table is not compatible with the unique Mast-R-Lift-II-R sold by Rockler, which uses a narrower 8-1/4″-wide top plate.
Router plate size: 9-1/4″ x 11-3/4″ x 3/8″
Note: Specify your router preference when placing an order with your INCRA dealer. (See PDF for compatibility chart).
A good fence is vital for accurate cutting on a table saw. Check out this range of potential upgrades.
We may earn revenue from the products available on this page and participate in affiliate programs.
One of the key accessories for a table saw is a sturdy fence. It is almost impossible to cut boards and sheet material accurately without one.
All table saws come with a fence included, but some lack the precision necessary for quality woodworking. Alternatively, if a fence has been damaged, it presents the opportunity to upgrade rather than simply finding a like-for-like replacement.
The following article looks at the important features that need to be considered and showcases our choices for the best table saw fences on the market right now.
- BEST OVERALL:Delta T3 30″ Fence System
- BEST BANG FOR THE BUCK:Woodstock International Shop Fox W1410 Fence
- BEST PRECISION:Vega U26 Table Saw Fence System
- MOST VERSATILE:Woodstock International Shop Fox W1716 Aluma-Classic
- BEST MAGNETIC:Carter Magfence II
What to Consider When Choosing Best Table Saw Fence
If a table saw isn’t delivering consistent accuracy, the fence may well be at fault. It may not be particularly well-made. If it doesn’t clamp securely or isn’t rigid, then it could deflect during the cut. To assess the quality of a table saw fence and its suitability for a particular saw, the following features should be considered.
Type
There are two types of table saw fence: standard (sometimes called sliding) and T-square. Sliding table saw fences are often those supplied with smaller, portable table saws. They run along rails fitted to the front and back of the saw table. On higher quality models, a rack-and-pinion drive allows for more precise positioning.
T-square table saw fences also run along a rail on the front of the table, usually with a three-point locking system. This provides strong support and holds the main part of the fence in place. As a result, this type doesn’t always need a rail on the far side of the table, though a rail is often supplied as an option. If the T-square fence requires fitting only on the front of the table, it doesn’t need to be a precise length. The fence can be shorter or longer than the table width and still function perfectly well.
Almost all aftermarket table saw fences—that is, those not made by a particular table saw manufacturer—are the T-square type.
Compatibility
Standard table saw fences need to be a specific length and cannot be modified, so their versatility is limited. Standard table saw fences are often brand specific, so a DeWALT fence, for example, will fit only DeWALT saws.
T-square table saw fences generally fit a wider range of saws. However, the mounting holes for their rails are not universal, so compatibility still needs to be checked.
Typically, the rails can be modified by drilling additional holes so it then suits the layout of a particular saw. This is fairly common practice, and several instructional videos are available for woodworkers who would rather make modifications than choose a different fence.
Rip Capacity
Rip (or ripping) capacity is the maximum cut that can be made. In other words, it’s the distance between the blade and the fence. Rip capacity is normally measured to both the left and right of the blade, and usually guide rails allow the fence to be mounted on either side. However, the right-hand side of the blade always has greater capacity, and that may be the only figure given.
Generally speaking, the rails should allow the fence to slide down to the far-right extremity of the saw table, therefore maximizing the cutting capacity. Rail extensions often can be purchased if those supplied are not long enough.
In some cases the opposite is true, and the rails extend beyond the table. Additional table and leg sections are available for many saws. However, rails that are too long can be awkward if shop space is limited.
Material
The main body of the table saw fence is made from either aluminum or steel, or a combination of both. Strictly speaking, steel is stronger while aluminum is lighter, though both provide equally good rigidity in the way they are formed for table saw use.
Some high-quality fences have laminated plywood faces. This material is intended to make the wood being sawed slide more easily across the surface. The downside is that the laminate eventually will wear and need to be replaced, and although it’s not difficult, it is time-consuming.
The mounting rails are almost always made of steel. They need to be strong to resist the clamping forces and the wear of the fence attachment running up and down them regularly.
Additional Features
Though table saw fence systems usually have a clear measuring scale, and some even have a small magnifying glass to make reading the scale very easy, positioning the table saw fence accurately can be a bit hit-and-miss. Microadjusters allow very precise placement by using thumbwheels to move the fence the last few fractions of an inch. Unfortunately, they are not always fitted, though several are available separately.
Digital readouts are another option, providing the user with a quick and precise visual display rather than the user having to check ruler markings. However, once again, these are usually an aftermarket extra rather than a feature that is included with the fence.
Our Top Picks
Having learned about the key features of table saw fences, it’s now time to look at some real-world examples. The following are what we consider to be the best table saw fences currently available and will fit a wide variety of saws.