Cutting styrofoam at home
Ways to cut styrofoam at home
For self-processing of foam plates, various improvised tools and devices are often used. The most common home cutting methods are:
- Open with a boot knife. The blade of the tool must have a special sharpening. the tip is blunt, and the wide part is perfectly sharp. When cutting with such a knife, unpleasant sounds are created.
- Soldering iron material processing. It is recommended to flatten the end of the working part of the soldering iron to increase its thickness. The tool allows you to quickly and smoothly cut small pieces of foam. You can also create rounded shapes using a soldering iron.
- Nichrome wire cutting. This option is considered the most popular when cutting foam at home. Its main advantage is the accuracy and speed of product processing. For cutting the material with a wire, a stationary installation is made, which significantly increases the productivity of the process.
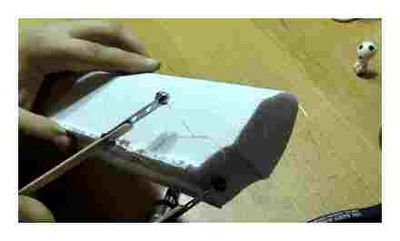
A boot knife. a device for cutting foam at home
If necessary, a nichrome device for cutting foam can be made by hand.
Manufacturing process
Having collected all the necessary parts, you can start assembling the cutter structure:
- At each end of the wooden block, make one hole corresponding to the diameter of the matched pencil. Its depth should reach half of the wooden plank. From the edge of the plank you need to indent 1.5 centimeters.
- In the lower part of the pencils, form a hole for installing copper wire, the ends of which should be rolled up in a ring.
- Place the plastic battery box on top of the bar with glue. Fix the pencils with the same composition in the previously made holes.
- To adjust the current to the string, install a switch on a wooden plank.
- The two wires should be soldered to the connector located in the battery container. From there, bring the current conductor to the switch, and then strip the ends from the braid and use a soldering iron to fix it to the copper wire on each separate pencil. Isolate the connection points.
- Pull the nichrome string tight, threading and fixing well between the copper rings.
Batteries should be inserted into the finished cutter and you can start working. Such a tool is capable of cutting styrofoam up to 4 centimeters thick. At the same time, with its help, you can cut out simple shapes.
Devices and methods for cutting foam
Polyfoam used to insulate various structures of a building has a rather loose structure. The cellular material easily crumbles and breaks under mechanical stress. To ensure the smooth edges of the cut of the heat-insulating product, special devices are used:
- Stationery knife. This method is the most affordable and simplest and is most often used when working with foam at home. The tool is effective only for cutting small-sized cellular products with a thickness of no more than 5 centimeters. The main condition for high-quality cutting with a clerical knife is the presence of a new and sharp blade.
- Thermal knife. This tool is specially designed for processing foam. The knife is capable of instantly heating up to 600 degrees. It is used for products of small thickness. In order to cut the foam sheet, you should smoothly move the tool along the intended mowing line. In the process of melting the material, fairly smooth edges are formed.
- Hacksaw for wood. Such a device is used if it is necessary to cut cellular heat-insulating material, the thickness of which exceeds 80 centimeters. For work, a saw is used only with fine teeth. With the help of such a tool, you can provide the product with smooth edges only with a straight cut.
Thermal knife. foam cutter
Builders sometimes use an angle grinder to cut the styrofoam and the required parts. This uses a disc with a minimum thickness.
On an industrial scale, cutting of porous material is carried out using special CNC machines. The cutting process on machines is carried out using various types of cutting tools:
- cutter;
- sharpened hacksaw blades;
- carbide discs;
- laser radiation;
- thin nichrome strings.
Most often, the industry uses the option of cutting by means of strings fixed in the required position. Many CNC machines are equipped with a computer program, and the process is controlled remotely.
Shaped cutting of foam
Polyfoam is quite one of the most popular finishing products. Various figures cut from such material are especially popular. Volumetric foam compositions are used as an architectural decoration, to create advertising elements, various design structures for interior decoration.
Shape cutting is carried out using laser systems and special CNC machines. Each device has its own advantages and features of use:
How to cut foam without using a wire cutter, quick cheap and effective (Tips & Talk Ep11)
- Laser cutting. The processing of foam by means of radiation allows the creation of 2D and 3D shapes of various shapes. This method of cutting provides the smallest cut thickness, contributing to increased detail of products. The whole process on laser CNC equipment is fully automated. Therefore, in the process of cutting the material, defects and errors are excluded.
- String processing. The formation of volumetric products occurs using the thermal effect of strings made of nickel-chromium. This method of cutting the foam ensures the accuracy of the cuts according to the given sketches. The cost of stringing cellular material is much cheaper than laser cutting. All actions on the machines are controlled by a special computer program.
With the help of modern 3D equipment for cutting foam plastic, you can make shapes of varying complexity in a short time.
DIY Styrofoam Cutter
In the process of manufacturing a cutting device, it is necessary to use the following materials and tools:
- screwdriver or hammer drill with a drill;
- soldering device;
- two identical pencils;
- pliers with a rounded section at the ends;
- PVA glue or other heat-resistant adhesive;
- nichrome thread;
- two copper wires;
- a wooden block 10 centimeters long;
- insulating tape;
- double battery box;
- wires. one meter;
- switch.
To power such a portable cutter, two conventional AA batteries are used.
Homemade machine
A stationary installation for cutting foam plastic allows you to more accurately cut the cellular product along the intended lines. In the process of processing, you do not need to make movements with the tool, but simply move the material itself. You can make a machine with your own hands.
Homemade foam cutting machine
For the manufacture of a stationary cutter, it is necessary to prepare the following devices:
- two long self-tapping screws with wide heads.
- nichrome string;
- wires for connecting current;
- rheostat for adjusting the charge strength;
- 12-volt step-down transformer.
A table is used as a basis. The supporting part can be made by yourself. The main condition for its manufacture is the presence of a flat smooth surface. Table sizes are selected arbitrarily.
Self-made cutter technology
There are many options for constructing effective foam cutters from improvised means. Two of them are especially popular. a cutter and a machine with nichrome thread. Each tool is quite simple to use and is able to provide an even and high-quality cutting of cellular material.
Required tools and materials
To make a cutter with nichrome wire for cutting foam, you will need the following tools and materials:
- small wooden block;
- screwdriver and drill;
- 2 pencils;
- 2 pieces of copper wire;
- round nose pliers;
- hot glue or PVA;
- insulating tape;
- battery connector;
- switch;
- 1 m of wires;
- soldering iron;
- nichrome thread.
How the foam is cut?
DIY Styrofoam Cutting Machine
Cutting machines are more convenient because the cutting thread is fixed in them and you only need to move the foam. This improves the accuracy of the movements. In the manufacture, you will need the same tools and equipment as in the previous case.
First you need to make a table, which is a wooden base with small legs. The table must be level and smooth to prevent deformation of the foam. The dimensions of the base can be chosen arbitrarily. A bar is screwed perpendicular to the tabletop, and a wooden crossbar is attached to it at an angle of 90 °. Then it is necessary to strengthen the structure with a jumper.
The corner ruler marks the place where the filament will go. If the surface is level enough, this can be done with a plumb line. To do this, a self-tapping screw with a wide head is screwed into the end, and a thread with a load is screwed onto it. A hole with a diameter of 6 mm is drilled in the selected place. To prevent the string from burning the wood, a plate of textolite or metal is installed. Place the material flush with the surface.
A wire is threaded into the hole, the lower end of which is put on a self-tapping screw. The screw is screwed in next to the hole. The length of the spiral should be such that it turns red when heated. Since the wire lengthens at high temperatures, a compensating spring must be used to avoid sagging. A spring is put on the upper self-tapping screw, and a nichrome thread is attached to it.
An energy source is connected to the ends of the filament, which can be a battery with a voltage of 11.7-12.4 V. To regulate this indicator, a thyristor regulator circuit is used. The regulator can be taken from an electric angle grinder. You can also control the voltage using a spiral on a polystyrene foam cutting machine.
This coil is mounted on a wooden block to which the upper edge of the filament is attached. Connects to the wire in series. Its function is to lengthen the nichrome thread and, accordingly, reduce the stress. This can be achieved by changing the place of connection to the nichrome spiral. The smaller the distance, the more the thread heats up and the more the foam melts.
If a transformer is connected to the machine, it must be galvanically isolated. In this case, a transformer with taps must be used.
For smooth and even cuts, you need to make a guide rail. It is made from a bar or any other even material.
With the help of such a simple machine, the foam is cut with your own hands. Additionally, you can make various devices. You can make a miter box during the repair with your own hands or a tray that will help you cut the material evenly at the right angles.
Homemade Styrofoam Cutter
A homemade cutter is intended for minor jobs. It is not possible to cut the entire sheet of expanded polystyrene for them. To cut styrofoam at home, you must:
- Make 2 holes in a wooden block 10-11 cm long. They should match the diameter of the pencils. You need to step back from the edge by 1-1.5 cm. The depression should be slightly deeper than half of the bar in order to fix the pencils. Thanks to this distance, you can cut foam sheets of almost any thickness.
- Glue both pencils into the holes with hot glue or PVA.
- In each of the pencils, make a small hole on top for the copper wire.
- Bend the copper wire with round-nose pliers so that small rings are formed at its ends. Then install in the holes in the pencils.
- Glue the battery connector perpendicular to a wooden block. Additionally, it will act as a handle.
- Stick the switch on the block so that you can de-energize the string.
- Then connect 2 wires to the connector. After that, connect to the switch, and then bring each one to a separate pencil. To prevent the wire from sagging and interfering with work, it is fixed with electrical tape. To ensure a reliable connection quality, you need to solder the wires to the connector. The joints must be insulated with heat shrink tubing or electrical tape.
- Remove the braid from the other end of each wire and screw it to the copper wire. Solder connection.
- Thread the nichrome thread into the copper wire rings and fasten to them. The string should be tight between the pencils. When heated, it stretches and sags a little. The tighter the tension, the less sag.
- Insert the batteries into the connector and start cutting the foam sheets.
Thus, you can make a simple device for cutting foam with your own hands. And another option for making a machine, look at
DIY nichrome cutter
The foam is cut with a string heated to 120. 150 ° C and melting material. Thanks to this, the cut is even, and the foam does not crumble. On such devices, a nichrome thread is installed through which electricity is passed. You can make a simple cutter with your own hands. It differs from the machine in portability and compactness, therefore, the heating temperature of the nichrome wire on it cannot be adjusted.
3D foam cutting technology
Expanded polystyrene products began to be widely used for marketing and decorative purposes. They make company logos from expanded polystyrene, cut out names, various figures, decorative elements, etc. Therefore, 3D cutting has gained wide popularity. The use of foam allows you to save money and at the same time get a high-quality and durable product.
Volumetric cutting is carried out on special machines. They cut the material using long strings or a laser and allow you to shape the foam into any shape.
Shaped cutting of foam
Figured cutting of expanded polystyrene is carried out on special machines. Some of them are equipped with CNC. When working on a machine, the thickness of the foam sheets does not matter. However, for simple cutting, you can use a simple DIY cutter.
Cutting styrofoam with a string at home
Diagram of a foam cutter: 1. nichrome wire (spiral from an electric stove), 2. screw with nut and washer, 3. handle (textolite S 4 mm), 4. power cord, 5. plug, 6. rubber or PVC tube.
You can cut this material at home in different ways. some use a knife for this, but this tool is not effective, since the foam crumbles heavily. You can use a heated nichrome wire, it cuts the material perfectly, only you need to select the recoil, you need to take into account the temperature of the threads and the temperature of the foam. At home, you can design a special apparatus, for this you will need: a step-down transformer, springs for string tension, a pipe lining, the pipe thickness should be at least 20 mm, and the thickness of the foam sheet should be at least 2 cm. The string itself will also be needed.. with the help of which the material will be cut.
In order to make a tabletop for such a device, you will need a board, a table and a sheet of corrugated board. Making such a device with your own hands does not seem to be a difficult matter, the main thing is to be careful. In recent years, curly cutting of such material has been very popular, and if curly cutting of foam is planned, then a thermal cutter will be needed. As for the cutting part, it is a piece of nichrome wire that is attached to a handle made of insulating material. With the help of a thermal cutter, you can make indentations, cut cavities in the thickness of the material, with such a tool you can work with foam in the same way as a sculptor works with clay. After such a treatment has been carried out, a thin melted crust appears on the surface, which increases the rigidity and strength of the foam, it also closes its pores. And the step-down transformer can be made by hand.
In order to make a step-down transformer with your own hands, you need transformer iron. To select the magnitude of the current, you need to make a rheostat (a pre-stretched spiral from an electric stove is perfect for this). For the construction of the winding frame, you can use an asbestos-cement pipe or a ceramic pipe about 80 mm long and 15-20 mm thick. Winding wire from nichrome must be done until the frame is filled.
However, in some cases, such as with expanded polystyrene and polystyrene foam for floor and ceiling insulation, it is not at all necessary to use a special device for cutting the material.
You will only need to purchase the following tools:
- metal ruler (over 100 cm);
- pencil;
- painting knife.
The process of cutting slabs in this way is rather simplified. So, first you need to mark with a pencil where the cut will be made.
Now attach a ruler along the basting, pinch and gently, firmly draw with a paint knife along the mowing line of the notch.
Please note that it is not at all necessary for the knife to completely cut off the plate.!
Now turn the slab over, and on the other side, parallel to the cut just made, repeat all the above steps.
Thus, it turned out that the surface of the expanded polystyrene is notched on both sides. All that remains is to take the slab and break it in two along the mowing line. Due to the fact that you made an incision, the expanded polystyrene “breaks” exactly as it was needed.
Methods for cutting styrofoam yourself
Polyfoam is by far one of the most popular materials that are used in various fields. When working with Styrofoam, it is often necessary to cut it and this becomes a problem. However, there is nothing complicated in this, you can cut such material with your own hands, you just need to adhere to the instructions.
Diagram of a homemade foam cutting machine.
In order to cut the foam with your own hands, you can use a variety of household utensils, or you can make a machine for cutting this material.
How to cut styrofoam yourself?
DIY Styrofoam Cutting Machine
Diagram of the electronic part of the foam cutting machine.
Polyfoam is not only a high-quality insulation, but also a very good raw material for the manufacture of decorative products. And you can make such beautiful products with your own hands, a special machine is made for this. Such equipment can be very different, it all depends on what kind of product needs to be made.
Cutting can be carried out with a tungsten thread, it should be noted that such a thread is hot and initially it is possible to regulate its temperature, with its help you can cut not only expanded polystyrene, but also other materials. This is especially true when various elements for stucco molding are made. Any stencil is applied to the foam sheet, and a product is formed by means of a thread. All this is done quickly, efficiently and, most importantly, conveniently.
For the cutting machine, you can use a cutter and a construction blade. The design of the machines can be different, but they have the same principle. the use of a tungsten filament, it is connected to the electrical network. With the help of such a design, you can make a product of any complexity with your own hands. In order to cut the foam sheet with your own hands, you will need the following tools:
- thermal cutter;
- string;
- tungsten filament.
If everything is done correctly, then there is nothing complicated in the process. The main thing is to use only high-quality tools and to make maximum care and effort. There is absolutely no need to contact a specialist to cut the foam. All this work can be done independently and there is no doubt that the result will exceed all expectations. In this regard, when choosing a material such as expanded polystyrene for various works, there is no doubt that the work associated with cutting will be done quickly and efficiently.
Cutting styrofoam at home
Fishermen often need to cut foam at home into thin sheets. This is due to the manufacture of some kind of fishing foam crafts.
For small items such as fishing floats, homemade bloodworms, reels, a thick sheet of foam can be cut at home with a hacksaw by hand.
over, without the release of poisonous vapors, as when running a foam sheet in a homemade machine through a heated nichrome wire with a transformer that lowers the electrical voltage.
But cutting thin sheets of the same thickness from foam plastic, for example, to make a foam box for winter fishing without a special home-made machine, adapted for cutting foam at home with a heated nichrome wire. becomes an impossible task.
The site contains a do-it-yourself manufacturing process for a box for winter fishing. But before cutting and gluing the box, I had to first cut a thick sheet of polystyrene according to the technology proposed in the topic with nichrome wire on a homemade electric machine into relatively thin sheets of the same thickness.
The homemade floats and foam reels shown in the photo above are also made at home from foam, which was first cut through thickness.
There are also four windings of nichrome wire of different thicknesses, which are necessary in the manufacture of a home-made machine with a cutting heated filament.
True, to heat the nichrome wire, you need some kind of lowering the voltage of the network, an electrical device, which includes a transformer, a LATR or a rheostat with a powerful winding, which may also be a nichrome wire.
For cutting foam at home, a home-made machine for one-time or stationary use is assembled (completed), on which, as a rule, foam sheets of the same thickness are cut (with an exhaust).
The first version of the machine. mine, in view of the fact that I cut polystyrene into thin blanks very rarely. In addition, I always have a stock of the required thickness of foam sheets of different thicknesses, stored just in case.
He, if desired, can cut sheets with a red-hot nichrome wire of a standard size into thin blanks for making a fishing box.
As you can see, cutting foam at home can also bring material benefits.
Homemade Foam Cutting Machine
A homemade machine for home cutting of foam plastic with a heated nichrome wire is shown in the drawing. Let it be an undervoltage electrical wood burning device.
Then the components of a homemade machine designed for cutting foam at home include the following main elements:
Power cord for connecting the electrical circuits of the transformer to a household alternating voltage network.
A transformer that can be installed at home either directly on the tabletop of a homemade foam cutting machine, or lowered on the floor or fixed with brackets under the device’s table.
On the front panel, an electrical voltage is removed from two terminals of the power step-down transformer, which, using two mounting wires (3), is fed to a nichrome filament (9) stretched approximately in the middle of the tabletop.
The red color on the machine for cutting foam at home shows a section of nichrome wire (9), which will be heated in this scheme. The same section is a working area when cutting foam.
4 shows the tabletop of a foam cutting machine. It is possible to adapt a fiberboard for a homemade table at home.
one of the electrical insulators. rollers. The racks during the operation of the device will heat up, so it is advisable to use glass or ceramic insulators.
Number 6 shows the second roller and an aluminum hinge fixed in its groove. A nichrome wire is passed through the loop. This place of a homemade machine is shown in an enlarged view in the upper left corner of the figure.
By adjusting the bend of the loop (up and down), you can align the position of the heated filament above the table surface. Due to this, the thickness of the cut sheet after running along the surface of a self-made machine for cutting foam throughout the entire area will be the same.
By simultaneously raising or lowering the electrical insulators above the tabletop of the foam cutting machine (unscrewing or tightening the nuts on the bolt), you can adjust the thickness of the cut sheets.
The weight 7 regulates the tension of the heated nichrome wire 9. The wire lowered to the load will hardly heat up, since no current will pass through it.
A sheet of thick foam prepared for cutting at home on a homemade machine.
Cutting Styrofoam Into Thin Sheets
Foam plates of standard thickness are cut by fishermen into relatively thin sheets for making at home fishing tackle, crafts and accessories.
It can be homemade, glued from relatively thin foam sheets for storing fry. The porous material will prevent the water from freezing in winter and the fish overheating in summer.
Some fishermen at home cut foam sheets lengthwise to make lightweight heat-resistant boxes for winter fishing, from the remains of which you can make boxes for storing baits, reels of lines and leashes that do not sink in the water, and many more needed for summer fishing. winter fishing fixtures.
We cut at home (in the garage) thin sheets for the walls of fishing boxes from very dense foam with side dimensions 1000x1000x60 mm with a hot nichrome wire 0.5 mm thick. When cutting foam plastic with such a thick heated wire, cut thin sheets get a strong melted surface that does not require finishing machining.
To slit a smaller foam sheet over the tabletop of a homemade electric machine, it is better to stretch the nichrome wire thinner. This saves consumables and makes it easier to handle the melted sides.
And, of course, when cutting foam with a heated nichrome wire at home, you definitely need (I repeat) exhaust ventilation.
Foam Cutting Wire
The most common heating thread used when cutting foam at home is nichrome wire. Coils of different diameters of wire made of nichrome are shown in the picture.
But if a short piece of nichrome wire, even if it has a high resistivity to the electric current passing through it, is connected directly to the network, then even before we start cutting the foam, the wire will burn.
Therefore, the cutting part of a homemade machine. nichrome wire. they are connected to the user’s AC network through various voltage-reducing devices, thereby regulating the heating of the filament, with the help of which the foam is cut at home.
A massive sheet of foam can be cut lengthwise with a heated nichrome wire into thin plates.
True, the thermal method of cutting foam plastic has one drawback, which is especially evident at home. When melted with a red-hot nichrome wire, foam materials release caustic vapors that are not very pleasant in smell and are not entirely beneficial to health.
Therefore, when carrying out this kind of work, it is desirable to connect exhaust or through ventilation, which is almost impossible to carry out at home.
How to Cut Polystyrene Foam
Aligning the filament of the machine
Aligning the filament over the tabletop of a home-made electric foam cutting machine at home is carried out by running the nuts on the insulating roller racks along the threads. The same rollers lift the filament above the tabletop.
But it can happen that the filament of the foam cutting machine is too high above the table surface.
Then on the table before cutting the foam, we put the required thickness of a board or two parallel bars of the same height. We put a sheet of polystyrene prepared for cutting on the board and push through it an electrically heated filament.
Of course, the heated nichrome will always be in a position rigidly fixed above the table for cutting foam. We will be moving away from ourselves.
Electrical diagram of the foam cutting machine
The adjacent figure shows the electrical diagram of a homemade foam cutting machine at home, where the primary winding of the transformer is connected to the AC mains.
Tr. it is a voltage step-down power transformer. The taps from its secondary winding are connected to any electrical switch. It can also be regular contact sockets.
From the common terminal of the switch, we start a wire to one of the extreme contacts of the rheostat R. As the device regulating the current in the electric circuit, we use a school rheostat or a powerful wire potentiometer, which we attach to the front panel of the box.
Before connecting a homemade foam cutting machine to a household electrical network, the slider on the rheostat must be set to maximum resistance.
One output terminal of the power supply of the foam cutting machine at home starts from the beginning of the secondary winding of the transformer. Connect the wire from the potentiometer slider to the other output terminal.
Perhaps, in your electrical circuit of the electric foam cutting machine, the rheostat will be superfluous. Try first to select the voltage required for heating the wire with various combinations of connections of both supply wires to different sockets.
I don’t know how it is now, but earlier devices with output voltages up to 36 volts were considered safe to work in rooms with non-aggressive environments.
So you have to find some kind of electrical device for your homemade foam cutting machine at home and connect it according to the scheme suggested above.
Electrical battery chargers and transformers for low power welders may be suitable. The main thing is that they have the ability to smoothly (or stepwise) change the output voltage (current).
In addition, you don’t always need to cut very large sheets of Styrofoam on your machine. They can first be cut along the length and width with a hacksaw, then flattened along a heated nichrome wire.
material.
The heating of a filament with a high resistance to the current passing through it, included in the electrical circuit of the machine for cutting foam plastic, depends on the thickness of the wire, the most common diameters of which are in the range of 0.2-0.5 mm. An increase in the diameter of the nichrome wire will lead to more intense heating of the entire electrical circuit.
Fastening the insulators of the foam cutting machine
I propose this method of attaching electrical insulators on the tabletop of a homemade foam cutting machine at home.
In the place where the ceramic insulators are attached, through the opposite edges of the table, drill two holes for the long bolts. The bolt threads must pass through the holes in the insulating rollers.
We put wide metal washers on the bolts, put them into the drilled holes from below, press them tightly to the upper surface of the table, screwing the nuts on them all the way. It is better to sink the nuts flush with the table surface in the blind holes drilled for this.
Further, for a more reliable fastening of electrical insulators, we screw one more lock nut onto both bolts, driving them to the upper plane of a homemade table for cutting foam. Then we put on the insulators and, if they are not firmly seated on the thread of the bolts, then we press them from above with the nuts screwed onto the bolt.
With this arrangement of electrical insulators on a homemade foam cutting machine at home, there is a good opportunity to adjust the height and parallelism of the filament above the table.
The best way to cut styrofoam at home: choosing the right tool
To find out the best way to cut polystyrene at home, you need to consider in more detail the available options with which these works are performed, thanks to which it will be possible to choose the most practical tool for this task, which will make it possible to efficiently cut the insulation with your own hands and exclude its damage.
Cutting foam with a knife
For cutting sheets up to 5 cm thick, it is optimal to use a construction or office knife, in which the length of the blade allows you to cut through the insulation from one pass. A suitable option is to use a tool with a retractable cutting element. The cutting process itself should be performed when laying the sheet on the edge of a table or other similar work surface. When carrying out work, the cutting edge of the tool should be located as close as possible to the reference plane. Before cutting, the blade should be sharpened with a buffing wheel or, if possible, replaced with a new one, if necessary.
The cut off part of the foam board must be held without fail so that the insulation does not damage under load. To obtain an ideally high-quality cut during work, the tool needs to be moved with a slight force in the direction away from you, and during the return stroke, the movement of the cutting element must be done “idle”. If the slab is cut on a work table using a boot knife, then the blade should move in the opposite direction so that it moves from the far edge of the sheet towards itself.
Cutting styrofoam with a hacksaw and angle grinder
With the use of the first tool, it is much easier to cut the insulation, although the principle of the work carried out is no different from what happens when using a knife. She is often preferred when there is a need for cutting plates up to 8-10 cm.To cut foam sheets, you can use a hacksaw for metal or wood, but in any case, the blade must be of optimal length and have small teeth. In the presence of such cutting elements, the cut will be noticeably smoother, and the amount of debris that occurs is an order of magnitude less. It is possible to carry out work using this tool in almost any convenient position. When cutting, it is only important to make a smooth movement of the hacksaw, and not in jerks.
Cutting foam sheets can also be done using an angle grinder and an electric jigsaw, but in this case it must be borne in mind that a significant amount of debris is generated during the work. This is due to the fact that in the first situation the circle of the tool rotates at a high speed, and if the disk also has large teeth, then during the sawing process there will be a significant destruction of the structure of the insulation in the place of the cut. If you reduce the speed to a minimum value, then as a result, the foam will begin to burn and melt, which must be avoided in order to avoid damage to it.
In general, the angle grinder is excellent for cutting slabs up to 50 mm thick, but the quality of the cut will be an order of magnitude better than when using a knife, hacksaw or other electric tool. For optimal results, you need to use a thin diamond-coated wheel, which, after passing through, creates a better cutting place than when using a disc designed for working with metal.
When carrying out work, you can also use a jigsaw, but with its help it is not possible to achieve perfect evenness on the cut due to the vibration of the saw, and also a lot of small debris arises during the cutting process. A significant advantage of its use lies in the ability to make curly cuts, which turn out to be much more difficult to carry out using the other above tools.
Features and benefits of foam
The material is white, almost 95% air. Insulation, due to the absence of harmful substances in its composition, is environmentally friendly and is not capable of harming human health. Polyfoam is manufactured in slabs of different sizes and thicknesses, and is also used for many different tasks due to the huge number of the following positive qualities:
- Resistance to moisture, due to which the insulation is not adversely affected by various fungi and mold. In addition, due to its resistance to moisture, the insulation does not age and does not lend itself to destruction under its influence.
- Low weight, which allows you to easily transport and carry polystyrene, as well as use it when carrying out repair work and performing many other tasks that are conveniently carried out not only with someone, but even alone with your own hands. Due to its extraordinary ease when installing on the street, it must be borne in mind that its sheets can fly away even with a weak breath of wind.
- The material withstands low and high temperatures, as well as its drops, which is why it can be used not only for internal, but also external insulation of the house. In addition, polystyrene can be used for a number of other tasks, for example, it can insulate a metal entrance door.
- Ease of cutting. Thanks to this, you can cut the foam with your own hands at home without the help of specialists, using various tools.
- High thermal and sound insulation performance. In the first case, the insulation provides reliable protection of the premises, preventing the penetration of cold from the street, as well as retaining heat inside the buildings, thereby significantly reducing the cost of heating them. Good soundproofing qualities significantly reduce the amount of incoming and outgoing noise and allow, for example, when living in an apartment building, listen to music louder and not create any inconvenience to neighbors.
Taking into account all the above indicators, polystyrene is an excellent thermal insulation material, which, in addition to all of the above, also has a fairly long period of operation, without losing its positive qualities over time.
Thermal methods for cutting foam
Cutting the material with a thermal cutter is also a fairly popular method. The tool itself looks like a nichrome thread, which is laid on a frame in the form of a frame. When an electric current passes through a nichrome wire, the metal surface heats up, and the foam begins to melt. There are several torch designs available. The simplest option is in the form of a nichrome string stretched on ceramic insulators, which are fixed at the edges of a frame made of wood or metal.
With this tool, you can cut not only foam plates, but also wooden slats, plastic pipes, as well as any material that melts or decomposes at temperatures up to 270 ° C. If you need to cut sheets with a significant length of cut, then it is much more comfortable to use the machine, which looks like a thread stretched in a vertical position on a textolite stand.
If, in the process of working with foam, there is a need to cut off only small parts of the sheets, for example, when making a model and sculpture, then the best option is to use a nozzle for a powerful electric soldering iron.
In addition, a laser is used to cut this material. In some cases, they even use it at home. For this task, an ordinary LED laser with a power of 2-5 W is used, through which it is possible to cut foam plates along any required path. At the moment, with the help of such a tool, it is possible to cut paper and polystyrene for 10-15 minutes, which is why it is rather difficult to process a significant amount of material with it.
Having familiarized yourself with the different options, you can not only find out what is the best way to cut foam at home with your own hands, but also choose the most suitable method for use, through which it will be convenient to cut it.