How to change brushes in a screwdriver
Diagnostics
Do not rush to disassemble the screwdriver when the chuck does not rotate when you press the start button. Start simple. replace the battery with a known good and fully charged one. If there are no changes, remove the battery, unscrew the screws from the case and disassemble it. Measure the resistance between the brushes with a multimeter. With wear not exceeding the permissible level, they will have good contact with the collector, and the device will show a resistance close to 0. If the readings are more like an open circuit than a short circuit, knock on the brush holders with the handle of a screwdriver and turn the motor rotor by hand several times. A persistent tester reading will indicate that contact has not recovered and the instrument requires repair. Making such a check is easier than disassembling a motor, especially an unmaintained one. It should be noted that the symptoms of breakage of the armature windings and wear of the brushes are the same. But winding breakage is an extremely rare event, wear is much more common.
Replacement
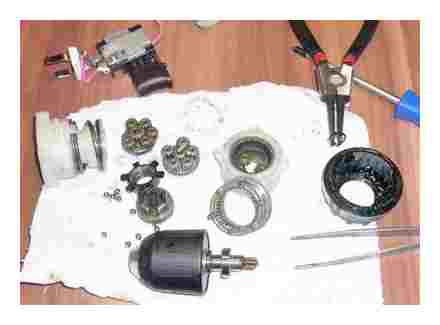
It’s simple on a serviced engine.
- Disassemble the case
- Take out the worn out kit
- Put a new one
- Assemble the case
The maintenance-free motor is distinguished by the rolling of the rear ends of the holders. Often the lid, on the inside of which they are located, inserted into the body, is fastened by rolling. Here, the process is somewhat more complicated.
- Use pliers to bend the flare that holds the cover
- On the perimeter of the cover and body, mark 3 points equidistant from each other
- Take out the cover
- Using soldering fat, solder and a powerful soldering iron, irradiate the marked points
- After cutting the stranded wires, replace the worn brushes with new ones.
- Solder the wires coming from them to the holders. Then, in order not to break the copper. graphite contacts when installing the lid, alternately drown them in the holders and fasten each in this position with a thread, tying it with a bow
- Leaving the ends of the threads outside, install the cover into the body
- Re-establish contact in the control room by undoing and pulling the threads
- Solder the cover to the motor housing
Replacing brushes on a screwdriver on your own
The reason that the screwdriver stopped working is often excessive wear of the brushes of its electric motor. It is not difficult to eliminate such a malfunction, but a minimum knowledge of the DC motor is required. Let’s start by defining what brushes are.
Brushes
Motor brushes are contacts through which current is supplied to the rotor windings. Since the rotor is designed to rotate, it is impossible to supply current to its windings through a fixed wire connection. For this, a collector-brush assembly (KShU) is used. The collector consists of copper plates attached to an insulated section of the armature shaft. The leads of the rotor windings are connected to them. The brushes are attached close to the collector. As the rotor rotates, they slide over the collector plates. Current flows alternately through these sliding contacts in the armature windings. The resulting alternating magnetic field is the force that rotates the rotor.
Knowing how the unit that feeds the armature windings works, it is easy to guess that its parts must wear out. The rotor is complex and expensive to manufacture. Therefore, in order to protect it from wear collector, the material for making the brushes is deliberately chosen to be less abrasion resistant. Otherwise, it would not be necessary to replace the brushes, but the anchor. Another essential property of brushes should be good electrical conductivity. Better than others, these conditions are met by a mixture of copper powder with graphite. Electric motors with a lower power or higher operating voltage than a screwdriver can be equipped with graphite brushes. And graphite is not suitable for a screwdriver motor with low operating voltage and high currents due to the electrical resistance that is too high for it.
About labor costs
Repairing a screwdriver with a serviceable motor can be done relatively quickly. The same cannot be said about restoring a device that cannot be repaired. Think, maybe, in the time it takes to repair, you can make money by doing what you do well enough to buy a new one. After all, you shouldn’t learn something to do it just once.
How to insert a drill into a screwdriver?
An irreplaceable power tool in everyday life with a self-explanatory name, the screwdriver is actively used in construction work. The most common procedure with such a device is to replace the drill. Sometimes it seems that this process is very difficult and practically impossible. However, in fact, replacing a drill in a screwdriver will not be difficult, the main thing is to follow the instructions step by step and pay attention to the details.
Features of the screwdriver
A screwdriver means the same drill, but it has a lower rotation speed of the chuck and the ability to adjust the twisting force. Many hours of twisting and untwisting with their own hands have never given pleasure to anyone. The screwdriver will help you quickly and efficiently tighten and unscrew the fasteners. Also, using this device, you can make holes in materials of various densities. metal, wood and stone. The power of the screwdriver comes from the mains or battery.
The building device is divided into the following types:
- standard;
- rechargeable screwdriver;
- drill screwdriver;
- wrench.
All types of tools differ only in their purpose: a screwdriver (ordinary) is used only when working with fasteners, a drill will help to drill the required hole, a screwdriver is intended for twisting and unscrewing fasteners with a cross-shaped “head”, a device with the self-explanatory name of a nutrunner copes well with bolts and nuts.
Replacing the cutting tool
The “tail” of the screwdriver drill is fixed in the chuck. It comes in different sizes, just like the attachments. If the cutting tool is incorrectly installed, the screwdriver can damage the work process and harm your health. For example, due to the “wrong” drill, holes of different sizes with a damaged surface can be obtained. The sharp element will cause serious injury when it “leaves” the cartridge.
Most modern screwdrivers have jaw chucks. They consist of a cylindrical body as well as a sleeve and cams. When the sleeve rotates clockwise, the cams simultaneously press the drill.
The process of replacing it is simple, but it has a number of individual characteristics. The whole process can be described as follows:
- it is necessary to select the necessary nozzle (bit) for the drill;
- then you need to take the cutting tool and install it in the center of the chuck (between the open “cams”);
- after that, it should be fixed by turning the sleeve clockwise (with a key type cartridge, the key is installed in the recess);
- twist the sleeve until the attachment is fixed.
It is not difficult to change the drill, but first you need to pull out the previous one. There are the following options for the development of the situation:
- standard removal of the drill (the chuck is not damaged);
- pulling out the drill in the absence of a key;
- removing a jammed cutting element.
If the screwdriver is working properly, problems should not arise when replacing its working tool. the operation is elementary. To do this, you need to take the key, which is designed to loosen the cartridge, and insert it into the recess. Twist counterclockwise. The unwinding is carried out due to special teeth that are on the objects. There is also another option for removing the drill. To do this, turn on the reverse rotation mode on the screwdriver, hold the outer case of the cartridge and press the “start” button. This way the drill can be easily released.
If you do not have a special key, the drill can be removed using a Phillips screwdriver or a nail. It must be inserted into the recess on the chuck and half of it fixed. We twist the opposite part of the cartridge by hand. However, if such unwinding does not work, then we take a gas wrench or a vice. these tools will help to increase the rotation of the cartridge. If the previous options for pulling out the drill failed, then you should resort to “heavy artillery”. In some cases, external damage to the drill makes it difficult to reach. In this situation, it is necessary to relax the “cams” with the help of gas keys and a vice. We completely clamp the cartridge with keys and rotate (unscrew).
In this process, the simultaneous use of both the key and the vise is encouraged. You can also take a hammer and lightly hit the chuck with it. vibration from impacts helps to relax.
A radical option in the most hopeless situation would be to twist the cartridge from the screwdriver. To do this, it is necessary to squeeze it in a vice and forcefully knock out the cutting tool from the inside using a punch. Naturally, after such a procedure, the screwdriver should be taken to the repair. Summing up, it is worth noting that the procedure for inserting a drill into a screwdriver is quite simple and even someone who has never done this can handle it. The main thing in this process is to follow the recommendations.
For information on how to insert a drill into a screwdriver, see the next video.
How to change the battery in a Makita screwdriver yourself
Preparing and opening the case
Before starting work, the battery for the Makita screwdriver is disconnected, its contacts are cleaned with an emery cloth, and it is fully charged.
The battery case is usually made of two plastic halves, glued at the connecting seam, and / or bolted. To open it, the bolts are turned out, and the glued seam is slowly tapped with a mallet with a rubber or other non-metallic head. This takes some time, from 10 minutes or more. If a wedge can be inserted into the seam (for example, a chisel with a thin sting), it is inserted and tapped on it. this speeds up the process. As a result, the body should be neatly divided into two halves, which can later be reassembled.
Analysis of elements and assembly of a healthy module
The extracted elements (all together and each separately) are measured for voltage. It is recommended to keep contacts on each of them not for long, but not too little, the optimal time is about 5 seconds. If this limit is exceeded, the elements may burn out, and insufficient measurement time may distort the readings. The normal voltage of each individual lithium battery should be between 3.6-3.8 V. If this value is 3 volts or less, such a unit is no longer suitable for operation. The measurement results are recorded, after a while (about 20 minutes) the procedure is repeated for the reliability of the readings. If the battery voltage was high, but in the second measurement it became low, and the difference is 0.4-0.8 volts, it is inoperative.
Screwdrivers usually come with two battery modules. If you disassemble both and identify serviceable and faulty batteries, you can assemble one full-fledged module from two blocks that have lost power. To do this, the identified serviceable parts are connected according to a certain scheme, placed inside the case and fastened together. Serviceable elements can also be purchased separately, you just need to make sure that their capacity and dimensions are identical to the old used ones.
Fastening of new batteries is carried out using soldering. At the same time, some precautions are observed.
- They must not overheat or they will deteriorate.
- The plates connecting the elements must have a certain current conductivity, so it is better to use those that were originally in the module.
- The sequence of connecting the batteries must not be broken: the plus must always be followed by the minus.
How to replace the battery in a Makita screwdriver
To find out how to replace the battery in a Makit screwdriver, you need to familiarize yourself with its device. The screwdriver battery pack consists of:
- plastic case;
- feeding elements (“cans”);
- thermal detector.
Elements can be nickel-cadmium or lithium-ion. They are interconnected in a certain sequence, their number differs and depends on the model of the screwdriver, the magnitude of the voltage. The temperature detector transmits its readings to the charger so that the battery does not get too large or insufficiently charged.
How to replace the battery without laborious disassembly / assembly
If the user does not want to disassemble a used battery and assemble it from several serviceable elements, a new serviceable battery module can be purchased separately.
Right choice
- Plastic brushes.
- Three-piece. dismountable parts.
- Conventional, consisting of a spring and a graphite rod.
Please note that it is not necessary to immediately dismantle the old ones to purchase new parts. You can tell the brand and model of the washing machine to the seller, and he will advise the appropriate option.
During inspection of the electric motor, it may be revealed that only one brush is worn out. In this case, it is recommended to replace both parts anyway.
Breakage signs
Service center masters claim that with proper use of the washer, brushes can last up to five years. And with rare use of the machine. twice as long. By what external signs can you understand that the brushes are faulty:
- The washing machine stopped in the middle of a wash cycle, although the electricity did not turn off.
- When the SMA is working, extraneous sounds are heard (noise, crackling).
- Poorly spinning laundry as a result of reduced engine speed.
- You can smell the burning.
- Fault code F02 appears on the washing machine screen, which means problems with the operation of the electric motor.
From these signs, you can only assume a malfunction. To be sure that replacing brushes in the Indesit washing machine is necessary, you need to partially disassemble it.
How to change brushes in the Indesit washing machine
The collector motors of washing machines are equipped with electric brushes, which are used to transmit electricity to the rotor of the motor, and it rotates. These are small parts consisting of a tip and a long spring. Since their tip is made of soft material, it will wear off over time.
In this article, we will find out how to replace the brushes on the Indesit washing machine.
Preparing for repair
Replacing the brushes of the engine of the Indesit washing machine is a simple repair. You will need the following tools:
- Slotted or Phillips screwdriver.
- 8mm torx wrench.
- Marker.
Prepare your washing machine:
- Disconnect the CM from the network.
- Shut off the water supply by turning the inlet valve.
- Prepare a container to collect water.
- Unscrew the inlet hose from the body, drain the remaining water from it.
- Go to the front panel. Below you will see a hatch. open it by pressing the plastic latches with a screwdriver.
- There is a drain filter behind the hatch.
- Take it out, drain it, clean it up.
- Move the machine away from the wall so that you can walk to the back wall.
So, you have prepared the tools and the washer for repair. Get started.
Step-by-step execution of work
Before changing the brushes on the Indesit washing machine, you need to remove the back wall of the washing machine. For this:
- Take a screwdriver and unscrew the two self-tapping screws that hold the top cover at the back.
- Push the cover away from you, lift it up and set it aside.
- Remove the screws around the perimeter of the back cover.
- Take it off.
- Below, under the tank, the SM engine is located.
- To remove the drive belt, pull it towards you while rotating the drum pulley. It will fly off easily.
- Photograph or mark the location of the motor wires with a marker. Then disconnect the wiring.
- Using an 8mm socket wrench, remove the bolts that hold the motor. There can be from three to four pieces.
- Swinging the electric motor back and forth, pull it out of the SMA housing.
Be careful! The engine is heavy.
Now is the time to inspect the collector brushes. They are located on both sides of the motor housing. Usually, Indesit washing machines use CAR014UN brushes, which are also analogous to N52A, CAR024UN, UN135. So, choosing one of the models, you can’t go wrong.
HOW TO CHANGE CARBON BRUSH OF YOUR HAND DRILL / WHAT’S INSIDE A HAND DRILL
To get the brushes:
- Disconnect the wire.
- Push the contact down.
- Pull the spring and pull out the brush.
To reinstall the parts, first place the graphite tip in the slot. Now squeeze the spring and also fit into the socket, closing with the contact. Connect wire.
Fine! You have performed a repair to replace the electric brushes. It remains to put the electric motor in place. What should be done:
- Bolt the motor in place.
- Connect wires according to photo or markings.
- Replace the drive belt. Put it on the engine pulley immediately, then, scrolling a little, onto the drum pulley.
- Replace the back cover by tightening all the screws.
DIY: Replace Carbon Brushes On An Impact Driver
- Close the top cover, screw in the two self-tapping screws.
It remains to connect the car and check the engine. At first, the motor can run quite noisy until the brushes are rubbed in. Then everything returns to normal.
It is possible to make a replacement with your own hands. Follow our instructions and you will succeed. Watch the video :
Chuck device
An internal thread on the chuck or a special cone is designed for mounting on a shaft. Structurally, the most wear-resistant components are divided into three main types:
- quick-clamping (BZP);
- self-tightening;
- gear-girth (key).
The most common option is BZP.
In this case, the shank is clamped by manually rotating the tool sleeve.
Clamping elements, which are installed on modern screwdrivers and drills, allow you to reliably fix shanks with a diameter of 0.8-25 mm.
Perhaps the only drawback of a new product of this type is the higher cost relative to key sleeves.
It takes a few seconds to fix an element in a clamping device of the BZP type.
In this case, the help of auxiliary components is not required.
The adjustment sleeve is corrugated, so the cylinder can be rotated easily.
The pressure on the shank of the product is adjusted using a locking element.
Clamping parts wear out over time.
Therefore, the device of the cartridge of the BZP category implies a gradual weakening of the clamp.
Due to wear, the liner is unable to securely hold large diameter round shanks.
Disassembled self-clamping and quick-clamping models are:
- sleeve;
- base;
- movable jaws;
- washer;
- bearing;
- toothed nut.
Design and features of the girth gear chuck
Unlike popular modern sleeves, this classic version requires the use of a special key. But in this case, a more reliable fastening is possible in all situations.
ZVP refers to clamping sleeves of the cam or collet type.
They make it possible to clamp both products with round shanks and cylindrical elements. The main components of cam SGP:
- cylindrical body;
- an adjusting sleeve or ring that rotates outside;
- cam mechanism that is mounted internally.
Collet mechanism is made of durable steel.
It consists of three twin cams.
When the sleeve or ring rotates, the latter form a single whole.
Due to this, there is a reliable fixation of products.
What is a cartridge
The cartridge resembles a metal cylinder. The part is attached to the shaft of the screwdriver.
The purpose of the element is to fix the working bits of fasteners.
How to choose a new cartridge
The chuck for the screwdriver is chosen based on a number of aspects. When choosing a suitable part, you need to be guided by the following recommendations:
- if the bits have to be changed frequently, it is better to prefer quick-clamping or self-locking cylinders; otherwise, work will go slower;
- gear-crown design. the choice of those who strive for maximum chuck reliability; if the priority is one hundred percent fixing the bit, it is better to purchase a key cartridge;
- when choosing a part, it is necessary to take into account its characteristics; parameters are regulated by the corresponding GOST; the larger the clamping cone, the larger the number with which it is marked;
- it is necessary to take into account the country of origin. the alphanumeric designations of foreign models differ from domestic ones.
If it is difficult to independently determine the type of “clamp”, it is better to consult a specialist.
Wrong choice is tantamount, at least, to incorrect operation of the tool.
In the worst case, it is possible not only to re-spend on a new cylinder, but also to replace the entire screwdriver.
How to remove a chuck from a screwdriver? Step by step instructions
How to remove a cartridge from a screwdriver, what it is and what they are, learn from this article.
The chuck for the screwdriver is one of the most mobile parts of the tool. Therefore, it wears out faster than many others.
To repair or replace this element, you need to know how to remove the chuck from the screwdriver.
To do this, you need to understand the types, device and methods of mounting cartridges.
Cartridge removal methods
To remove the cartridge, you need to know how it is secured.
If you have to replace the chuck in a screwdriver with a Morse taper fixation, you need the help of a hammer.
The last shank is knocked out of the body socket.
Sometimes the method may not work.
In this case, you need to take a radical path:
- disassemble the screwdriver;
- we take out the shaft with the gearbox and the chuck;
- using a pipe wrench, unscrew the clamping cylinder.
In rare cases, the sleeves may have wrench recesses.
This simplifies the task, but it is better not to count on it.
How to remove a threaded chuck
Consider how to remove the chuck from a screwdriver, in which the cylinder is attached to the spindle using a thread.
- unscrew the threaded fastener using the L-shaped hexagon;
- insert a key (usually 10 mm) with a short part into the cylinder and securely fix with cams;
- at low speeds turn on and then turn off the screwdriver; in this case, the free part of the hexagon must hit the support.
If the mount is very strong and all three methods do not work, then the tool must be disassembled.
How to remove the sleeve in this case is described above.
Situations requiring the disassembly of a drill or screwdriver arise when preventive work is neglected. the planned removal and cleaning of the “clamp”.
In addition, it is recommended to rest the instrument at least every 15 minutes.
Then the repair can be postponed, and you can protect yourself from unnecessary difficulties with removing the clamping device.
Design features
In the normal sliding mode, there is a small break in the electric current circuit. Microscopic arcs appear, and this is a faithful companion of sparks. A decent inductive resistance of the motor windings can also be added here.
At maximum load on the machine, even with new brushes, there will always be a spark. Visually, this may not be so noticeable, especially on low-power models, but sensitive equipment located in a room with a working vacuum cleaner will let you know about this in a specific background. Therefore, filters are installed on TVs, personal computers and other devices to eliminate such interference.
Why brushes sparkle
Brushes can be called the weakest element of a collector motor: at the time of operation of the unit, they are subjected to constant friction, which leads to their wear. This moment is especially noticeable on copper surfaces, where a layer of coal dust accumulates during the operation of the brushes.
Change the angle of inclination
If the angle of inclination of the brushes in relation to the stator is incorrect, arcing is also possible. The correct position is when both brushes are strictly on the same line passing through the axis of rotation of the collector. Over time, from constant vibration, the mount of the brush holder may loosen or even receive mechanical damage. Examine the knot surfaces carefully. Parts with cracks, chips or traces of corrosion must be replaced.
Each manufacturer brings design features to its product line, and therefore different types of vacuum cleaners have different types of brush attachment. However, in general, all models have the same design and the brush holder is usually screwed in with two screws and allows adjustment.
Homemade brush
The element must fit tightly into the grooves and be located strictly perpendicular to the axis of the rotor shaft. If the brush is less than the prescribed size, then a skew will appear. This will again lead to arcing and thus a decrease in engine performance. Therefore, here it is better to give preference to industrial options, rather than homemade ones.
Why sparkle brushes in a vacuum cleaner
Slight arcing between the brushes and the collector is normal. It is quite another matter if the former directly “spew out” sparks. Increased sparking of the brushes in the electric motor of the vacuum cleaner indicates a malfunction that can significantly reduce the life of the device. The phenomenon may be accompanied by a loss of engine power, uneven operation, overheating and other malfunctions. About why vacuum cleaner brushes sparkle. and what can be done, we will tell in this publication.
Eliminating bad contact
Often brushes spark when poor contact with the collector. This happens if you have installed new ones. For a more snug fit of the brushes to the collector, you can use the “sandpaper” zero, or just let the vacuum cleaner run at medium speed for about 20 minutes. It is imperative to check the condition of the bearings, as their wear can cause runout and uneven rotation of the rotor. Insulation protrusions between the collector plates, scratches on the surface, and various irregularities manifest themselves in the same way. Use abrasive paper for polishing.
The device of the collector motor of the vacuum cleaner
The brushes should not dangle in the brush holder, but have free travel, which is provided by a spring, the state of which also plays an important role.
If you decide to replace the brushes, be sure to pay attention to how tightly the spring presses them against the manifold. Sometimes, in order for the brushes to press harder, it is enough to stretch the spring a little.
Replacing brushes
The simplest and most obvious cause of sparks is brush wear. Despite the fact that collector motors are equipped with special spark-suppressing capacitors, which, in addition to increasing the service life of these elements, also reduce radio interference, over time the brushes wear out and must be replaced.
To replace the brushes, you first need to get to the electric motor. To do this, you will have to disassemble the vacuum cleaner. In most cases, it is quite easy to do this with a screwdriver, but do not forget to unplug the appliance. Having disassembled the vacuum cleaner and providing convenient access to the engine, we find the brush holders. Depending on the design, to remove the brushes from the brush holder, you usually need to pull back the latches, for this you may need a screwdriver.
When buying new brushes, you need to pay attention to their size and material.