How To Change Jigsaw Blade Quick – T-Shank And U-Shank. Jigsaw blade holder
US6178646B1. Blade clamping system for a jigsaw. Google Patents
Publication number US6178646B1 US6178646B1 US09/113,394 US11339498A US6178646B1 US 6178646 B1 US6178646 B1 US 6178646B1 US 11339498 A US11339498 A US 11339498A US 6178646 B1 US6178646 B1 US 6178646B1 Authority US United States Prior art keywords clamp blade clamp member collar slot Prior art date 1998-07-10 Legal status (The legal status is an assumption and is not a legal conclusion. Google has not performed a legal analysis and makes no representation as to the accuracy of the status listed.) Expired. Lifetime Application number US09/113,394 Inventor John W. Schnell Donald R. Bosten Daniel P. Wall James T. Stolzer Current Assignee (The listed assignees may be inaccurate. Google has not performed a legal analysis and makes no representation or warranty as to the accuracy of the list.) PORTER. CABLE Corp Black and Decker Inc Original Assignee Porter Cable Corp Priority date (The priority date is an assumption and is not a legal conclusion. Google has not performed a legal analysis and makes no representation as to the accuracy of the date listed.) 1998-07-10 Filing date 1998-07-10 Publication date 2001-01-30 1998-07-10 Application filed by Porter Cable Corp filed Critical Porter Cable Corp 1998-07-10 Priority to US09/113,394 priority Critical patent/US6178646B1/en 1998-09-18 Assigned to PORTER. CABLE CORPORATION reassignment PORTER. CABLE CORPORATION ASSIGNMENT OF ASSIGNORS INTEREST (SEE DOCUMENT FOR DETAILS). Assignors: STOLZER, JAMES T., BOSTEN, DONALD R., WALL, DANIEL P., SCHNELL, JOHN W. 1999-07-08 Priority to EP99305422A priority patent/EP0970771A3/en 2001-01-30 Application granted granted Critical 2001-01-30 Publication of US6178646B1 publication Critical patent/US6178646B1/en 2006-01-12 Assigned to BLACK DECKER INC. reassignment BLACK DECKER INC. ASSIGNMENT OF ASSIGNORS INTEREST (SEE DOCUMENT FOR DETAILS). Assignors: PORTER-CABLE CORPORATION 2018-07-10 Anticipated expiration legal-status Critical Status Expired. Lifetime legal-status Critical Current
Links
- 210000002832 Shoulder Anatomy 0.000 claims description 72
- 241000726123 Acanthurus Species 0.000 claims description 14
- 235000014101 wine Nutrition 0.000 claims 2
- 241000763859 Dyckia brevifolia Species 0.000 abstract description 8
- 239000000428 dust Substances 0.000 description 44
- 210000001847 Jaw Anatomy 0.000 description 38
- 210000004279 Orbit Anatomy 0.000 description 24
- 239000012530 fluid Substances 0.000 description 8
- 230000000875 corresponding Effects 0.000 description 6
- 230000001154 acute Effects 0.000 description 4
- 230000000717 retained Effects 0.000 description 4
- 210000002320 Radius Anatomy 0.000 description 2
- 230000001276 controlling effect Effects 0.000 description 2
- 230000001419 dependent Effects 0.000 description 2
- 230000005611 electricity Effects 0.000 description 2
- 230000002708 enhancing Effects 0.000 description 2
- 238000002955 isolation Methods 0.000 description 2
- 239000000463 material Substances 0.000 description 2
Images
Classifications
- B — PERFORMING OPERATIONS; TRANSPORTING
- B23 — MACHINE TOOLS; METAL-WORKING NOT OTHERWISE PROVIDED FOR
- B23D — PLANING; SLOTTING; SHEARING; BROACHING; SAWING; FILING; SCRAPING; LIKE OPERATIONS FOR WORKING METAL BY REMOVING MATERIAL, NOT OTHERWISE PROVIDED FOR
- B23D49/00 — Machines or devices for sawing with straight reciprocating saw blades, e.g. hacksaws
- B23D49/10 — Hand-held or hand-operated sawing devices with straight saw blades
- B23D49/16 — Hand-held or hand-operated sawing devices with straight saw blades actuated by electric or magnetic power or prime movers
- B23D49/162 — Pad sawing devices
- B23D49/165 — Pad sawing devices with means to move the saw blades in an orbital path
- B — PERFORMING OPERATIONS; TRANSPORTING
- B23 — MACHINE TOOLS; METAL-WORKING NOT OTHERWISE PROVIDED FOR
- B23D — PLANING; SLOTTING; SHEARING; BROACHING; SAWING; FILING; SCRAPING; LIKE OPERATIONS FOR WORKING METAL BY REMOVING MATERIAL, NOT OTHERWISE PROVIDED FOR
- B23D49/00 — Machines or devices for sawing with straight reciprocating saw blades, e.g. hacksaws
- B23D49/10 — Hand-held or hand-operated sawing devices with straight saw blades
- B23D49/16 — Hand-held or hand-operated sawing devices with straight saw blades actuated by electric or magnetic power or prime movers
- B23D49/162 — Pad sawing devices
- B23D49/167 — Pad sawing devices with means to adjust the guide plate or with means to adjust the plane in which the saw blade moves
- B — PERFORMING OPERATIONS; TRANSPORTING
- B23 — MACHINE TOOLS; METAL-WORKING NOT OTHERWISE PROVIDED FOR
- B23D — PLANING; SLOTTING; SHEARING; BROACHING; SAWING; FILING; SCRAPING; LIKE OPERATIONS FOR WORKING METAL BY REMOVING MATERIAL, NOT OTHERWISE PROVIDED FOR
- B23D51/00 — Sawing machines or sawing devices working with straight blades, characterised only by constructional features of particular parts; Carrying or attaching means for tools, covered by this subclass, which are connected to a carrier at both ends
- B23D51/02 — Sawing machines or sawing devices working with straight blades, characterised only by constructional features of particular parts; Carrying or attaching means for tools, covered by this subclass, which are connected to a carrier at both ends of beds; of guiding arrangements for work-tables or saw carriers; of frames
- B23D51/025 — Sawing machines or sawing devices working with straight blades, characterised only by constructional features of particular parts; Carrying or attaching means for tools, covered by this subclass, which are connected to a carrier at both ends of beds; of guiding arrangements for work-tables or saw carriers; of frames of arrangements for guiding the saw blade
- B — PERFORMING OPERATIONS; TRANSPORTING
- B23 — MACHINE TOOLS; METAL-WORKING NOT OTHERWISE PROVIDED FOR
- B23D — PLANING; SLOTTING; SHEARING; BROACHING; SAWING; FILING; SCRAPING; LIKE OPERATIONS FOR WORKING METAL BY REMOVING MATERIAL, NOT OTHERWISE PROVIDED FOR
- B23D51/00 — Sawing machines or sawing devices working with straight blades, characterised only by constructional features of particular parts; Carrying or attaching means for tools, covered by this subclass, which are connected to a carrier at both ends
- B23D51/08 — Sawing machines or sawing devices working with straight blades, characterised only by constructional features of particular parts; Carrying or attaching means for tools, covered by this subclass, which are connected to a carrier at both ends of devices for mounting straight saw blades or other tools
- B23D51/10 — Sawing machines or sawing devices working with straight blades, characterised only by constructional features of particular parts; Carrying or attaching means for tools, covered by this subclass, which are connected to a carrier at both ends of devices for mounting straight saw blades or other tools for hand-held or hand-operated devices
- B — PERFORMING OPERATIONS; TRANSPORTING
- B23 — MACHINE TOOLS; METAL-WORKING NOT OTHERWISE PROVIDED FOR
- B23D — PLANING; SLOTTING; SHEARING; BROACHING; SAWING; FILING; SCRAPING; LIKE OPERATIONS FOR WORKING METAL BY REMOVING MATERIAL, NOT OTHERWISE PROVIDED FOR
- B23D59/00 — Accessories specially designed for sawing machines or sawing devices
- B23D59/006 — Accessories specially designed for sawing machines or sawing devices for removing or collecting chips
- Y — GENERAL TAGGING OF NEW TECHNOLOGICAL DEVELOPMENTS; GENERAL TAGGING OF CROSS-SECTIONAL TECHNOLOGIES SPANNING OVER SEVERAL SECTIONS OF THE IPC; TECHNICAL SUBJECTS COVERED BY FORMER USPC CROSS-REFERENCE ART COLLECTIONS [XRACs] AND DIGESTS
- Y10 — TECHNICAL SUBJECTS COVERED BY FORMER USPC
- Y10T — TECHNICAL SUBJECTS COVERED BY FORMER US CLASSIFICATION
- Y10T279/00 — Chucks or sockets
- Y10T279/17 — Socket type
- Y10T279/17393 — One movable side
Abstract
The present disclosure relates to a jig saw blade clamp including a first clamp member defining a main slot. A second clamp member is positioned within the main slot. The first clamp member is moveable relative to the first clamp member between a first position in which the first and second clamp members are adapted to clamp a blade, and a second position in which the blade can be inserted between the first and second clamp members. A collar is pivotally moveable in first and second opposite directions relative to the first and second clamp members. The collar includes a cam portion that moves the second clamp member toward the first position when the collar is pivoted in the first direction, and also moves the second clamp member toward the second position when the collar is pivoted in the second direction.
Description
The present invention relates generally to hand-held electric saws. particularly, the present invention relates to blade clamping systems for reciprocal saws such as jigsaws.
Electrically powered jigsaws, also known as saber saws, are well known in the art. A principle advantage of jigsaws over other types of hand-held saws such as circular saws or Band-type saws is the ability to make curved cuts along relatively short radiuses. Consequently, jigsaws are particularly useful in performing tight scrolling cuts to cut curves into a work piece.
A conventional jigsaw typically includes an electric motor contained within a housing, and a shoe positioned beneath the housing. The shoe includes a bottom surface adapted to slide or ride along the top surface of a work piece. An open-ended slot is formed at a front end of the shoe. A straight, bayonet-type saw blade extends downward from the housing through the front slot. A leading edge of the blade includes a plurality of teeth that face in a forward direction toward the front of the shoe. In use, the blade is reciprocated in a generally up-and-down direction by the motor. As the blade is reciprocated, the jigsaw is manually advanced in a forward direction such that the teeth of the blade cut into a work piece. As the blade cuts into the work piece, the bottom surface of the shoe rides over the top of the work piece.
Some jigsaws are capable of producing an orbital blade motion. Such a motion has a rectilinear component of a generally up-and-down nature, and fore-and-aft motion advancing the cutting blade into the work piece. Typically, the blade advances on the cutting stroke, which is conventionally in the upstroke on most saws.
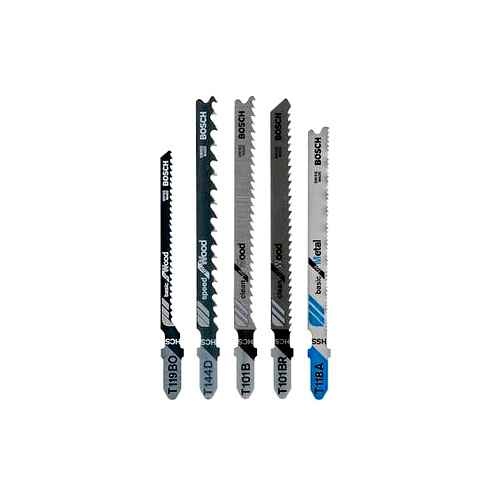
A variety of different blade types can be utilized with a jigsaw. For example, blades having different sizes, different teeth configurations, different teeth sizes, and different blade materials can be used. It is desirable to have a blade clamping system that allows blades to be quickly and easily interchanged.
An aspect of the present invention relates to a blade clamp that allows blades to readily be interchanged without requiring a tool.
Another aspect of the present invention relates to a single toolless blade clamp that can receive either universal or tang blades.
Jig Saw Blade Choice Made Easy
A further aspect of the present invention relates to a jig saw blade clamp including a first clamp member defining a main slot. A second clamp member is positioned within the main slot. The first clamp member is moveable relative to the first clamp member between a first position in which the first and second clamp members are adapted to clamp a blade, and a second position in which the blade can be inserted between the first and second clamp members. A collar is pivotally moveable in first and second opposite directions relative to the first and second clamp members. The collar includes a cam portion that moves the second clamp member toward the first position when the collar is pivoted in the first direction, and also moves the second clamp member toward the second position when the collar is pivoted in the second direction.
Still another aspect of the present invention relates to a jig saw blade clamp including first and second clamp members moveable between a blade release position in which a blade can be inserted between and removed from between the first and second clamp members, and a clamping position in which the first and second clamp members are adapted to clamp the blade thereinbetween. The first clamp member includes first and second spaced-apart shoulders separated by a gap. The first and second shoulders extend from the first clamp member toward the second clamp member, and are arranged and configured to trap a tang blade by engaging oppositely disposed tangs of a tang blade when the tang blade is positioned within the gap. The second clamp member includes a projection that extends from the second clamp toward the first clamp. The projection is arranged and configured to fit within a mounting opening of a universal blade when the universal blade is positioned in the gap between the shoulders.
A variety of advantages of the invention will be set forth in part in the description that follows, and in part will be apparent from the description, or may be learned by practicing the invention. It is to be understood that both the foregoing general description and the following detailed description are exemplary and explanatory only and are not restrictive of the invention as claimed.
The accompanying drawings, which are incorporated and constitute a part of the specification, illustrate several embodiments of the invention and together with the description, serve to explain the principles of the invention. A brief description of the drawings is as follows:
FIG. 1 is a perspective view of an embodiment of a jigsaw constructed in accordance with the principles of the present invention;
FIG. 7a is a front view of the jigsaw of FIG. 1 with the blade oriented in a perpendicular cutting position relative to the base;
FIG. 7b is a front view of the jigsaw of FIG. 1 with the blade pivoted counter-clockwise to a 45° angle cutting position relative to the base;
FIG. 7c is a front view of the jigsaw of FIG. 1 with the blade pivoted clockwise to a 45° cutting angle relative to the base;
FIG. 11 is a cross-sectional view that longitudinally bisects the motor housing and pivot base of FIG. 10;
FIG. 14a is a rear view of the movable clamp member of FIGS. 13a-13 d, the movable clamp is shown connected to a universal blade;
FIG. 15a is a front view of a fixed clamp member that is used by the blade clamp shown in FIG. 2, the fixed clamp member is attached to a shaft;
FIG. 16a is a front view of the fixed blade clamp of FIGS. 15a-15 c with a tang blade inserted therein;
FIG. 17 is a perspective view of the moveable clamp member of FIGS. 13a-13 d inserted within the fixed clamp member of FIGS. 15a-15 c;
FIG. 18 is a perspective view of an assembled blade clamp and blade clamp shaft utilized by the jigsaw of FIG. 1;
FIG. 19 is another perspective view of the assembled blade clamp and blade clamp shaft used by the jigsaw of FIG. 1;
FIG. 20a is an elevational view of the blade clamp and blade clamp shaft of FIG. 19 with the blade clamp in a clamped position;
FIG. 20b is an elevational view of the blade clamp and blade clamp shaft of FIG. 20a with the blade clamp in an unclamped position;
Reference will now be made in detail to exemplary aspects of the present invention which are illustrated in the accompanying drawings. Wherever possible, the same reference numbers will be used throughout the drawings to refer to the same or like parts.
FIG. 1 is a perspective view of an embodiment of a jigsaw 20 constructed in accordance with the principles of the present invention. Generally, the jigsaw 20 includes a housing 22 pivotally connected to a base or shoe 24. A front end of the shoe 24 defines an open-ended main slot 26. A blade clamp 28 is positioned above the main slot 26. A blade guide 30 is positioned generally beneath the blade clamp 28. The blade guide 30 is pivotally connected to the shoe 24 and is adapted to receive and laterally support a jigsaw blade clamped within the blade clamp 28. The terms “base” and “shoe” are intended to be used interchangeably.
In general use, a blade is inserted in the blade clamp 28 such that the blade extends downward through the blade guide 30 and also through the main slot 26. The teeth of the blade preferably face a forward direction toward the open end of the slot 26, and at least a portion of the blade preferably extends below a bottom surface of the shoe 24. When the jigsaw 20 is activated, the blade clamp 28 and its corresponding blade are oscillated in a generally up-and-down motion. By placing the bottom surface of the shoe 24 against a work piece, and moving the jigsaw 20 in a forward direction, the teeth of the reciprocating blade are brought into contact with the work piece thereby creating a cut in the work piece.
FIGS. 2 and 3 provide a more detailed illustration of each of the components of the jigsaw 20. Referring to FIG. 2, the shoe 24 of the jigsaw 20 includes a main base 32, a sub base 34 positioned below the main base 32, and a pivot base 36 positioned above the main base 32. The sub base 34 is connected to the main base 32 by a plurality of bolts 38, while the pivot base 36 is connected to the main base 32 by bolt 40. Outer edges 42 of the pivot base 36 fit within longitudinal slots 44 formed on the top of the main base 32. The bolt 40 extends through a longitudinally elongated opening 46 defined by the main base 32. By loosening the bolt 40, the pivot base 36 can be slid longitudinally along the slots 44 relative to the main base 32. When the pivot base 36 is oriented in a desired longitudinal position, the bolt 40 can be tightened to clamp or retain the pivot base 36 in the desired longitudinal position relative to the main base 32.
The housing 22 of the jigsaw 20 includes several different components. For example, as shown in FIG. 2, the housing 22 includes a handle set 48 and a gear housing set 50. Each of the sets 48 and 50 includes two separate pieces that are bolted together. The housing 22 also includes a motor housing 52 positioned behind the gear housing set 50.
The motor housing 52 is pivotally mounted on top of the pivot base 36. The motor housing 52 is connected to the pivot base 36 by a shoulder bolt 54 that extends upward through a curved slot 56 that extends across a width of the pivot base 36. A clamping structure is used to tighten or loosen the pivotal connection between the pivot base 36 and the motor housing 52. The clamping structure includes a fixed ramp or wedge 58, a moveable ramp or wedge 60, and a threaded adjustment shaft 62. By rotating the threaded adjusted shaft 62 in a first direction, the clamp structure is tightened such that pivotal motion between the pivot base and the motor housing 52 is inhibited. By contrast, when the threaded adjustment shaft 62 is rotated in a second direction opposite to the first direction, the clamping structure is loosened thereby allowing the motor housing 52 to be manually pivoted relative to the pivot base 36.
An electric motor 64 is contained within the motor housing 52. The motor 64 includes an armature portion 66 that is rotatably mounted within a field portion 68. The armature portion 66 includes a pinion gear 70 and a fan 72. The motor 64 receives electrical power through an electrical cord 74. A switch 76 controls the flow of electricity between the electrical cord 74 and the motor 64.
The electric motor 64 functions to rotate the pinion gear 70 about a generally longitudinal axis. The rotation of the pinion gear 70 is converted into a reciprocal up and down motion by a drive mechanism 78. While a specific drive mechanism is shown and described, it will be appreciated that a variety of suitable drive arrangements or mechanisms are known in the art, and that any type of arrangement that generates reciprocal up and down motion can be used in accordance with the principles of the present invention. In using the term up and down motion, it is intended that such a term includes rectilinear up and down motion as well as orbital up and down motion.
The drive mechanism 78 includes a main drive gear 80 that is rotatably mounted on a pin 82 secured to the gear housing 50. The main drive gear 80 is rotated about the pin 82 by the pinion gear 70 of the motor 64. A cam 84, that is eccentric with respect to the pin 82, is formed on the main drive gear 80. A crank block 86 is bolted to the eccentric cam 84. An orbit lever 88 and a counterweight 90 are positioned between the main drive gear 80 and the crank block 86.
The orbit lever 88 is pivotally mounted on a pin 92 secured to the gear housing 50. The orbit lever 88 includes a u-shaped slot 94 that receives the eccentric cam 84 of the main drive gear 80. As the main drive gear 80 is rotated, the eccentric cam 84 pivots the orbit lever 88 back and forth about the pin 92. As the orbit lever 88 is pivoted back and forth, a lower arm 96 of the orbit lever 88 engages a lever arm 98 causing the lever arm 98 to be reciprocated up and down. The lever arm 98 is part of a roller holder 99 that includes a fork 100 in which a roller 102 is rotatably mounted. The roller holder 99 is pivotally mounted on a pivot pin 104. When the lever arm 98 is moved up and down by the orbit lever 88, the roller holder 99 is pivoted back and forth about the pivot pin 104. A rubber grommet 106 biases the lever arm 98 in an upward direction.
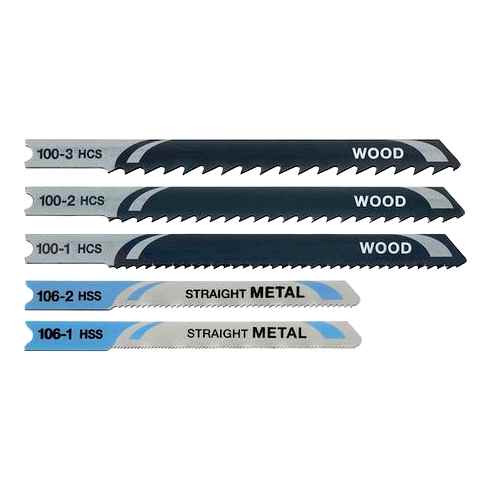
The roller holder 99 allows the jigsaw 90 to move a blade in an orbital up and down motion. For example, when a jigsaw blade is inserted within the blade clamp 28, a rear portion of the blade engages the roller 102 held by the roller holder 99. When the roller holder 99 is pivoted back and forth by the orbit lever 88, the roller 102 causes the blade to move forward and backward. Concurrently, the blade is reciprocated in an up and down motion by the blade clamp 28. In this manner, the blade is moved in an orbital up and down motion.
The amount of orbital motion provided to the blade is dependent upon the amount the roller holder 99 is pivoted about the pivot pin 104. In this regard, the jigsaw 20 is provided with an orbital motion adjustment mechanism for controlling the forward and backward movement of the blade. The adjustment mechanism includes an orbital motion adjustment shaft 108 including a cam surface 110 that engages the lever arm 98 of the roller holder 99. A knob 112 is used to rotate the shaft 108. By rotating the shaft 108, a spacing between the lever arm 98 and the lower arm 96 of the orbit lever 88 can be adjusted. For example, when the shaft 108 is in a first position, the cam surface 110 allows the lever arm 98 to be in close proximity to the lower arm 96 of the orbit lever 88. Consequently, a maximum amount of orbital motion is generated. By contrast, when the shaft 108 is in a second position, the cam surface 110 pushes the lever arm 98 a sufficient distance away from the lower arm 96 of the orbit lever 88 such that the orbit lever 88 fails to contact the lever arm 98 when the main gear 80 is rotated. As a result, no orbital motion is generated. It will be appreciated that the shaft 108 can be oriented at intermediate positions between the first and second positions in order to achieve intermediate amounts of orbital motion.
The counterweight 90 of the drive mechanism 78 includes an opening 114 that is elongated in a lateral direction. The eccentric cam 84 is received within the opening 114 such that the counterweight is reciprocated up and down as the main drive gear 80 is rotated. It will be appreciated that the reciprocation of the counterweight 90 is 180 degrees out of phase with respect to the reciprocation of a blade secured to the jigsaw 20.
The crank block 86 of the drive mechanism 78 is used to convert the rotational motion of the drive gear 80 into rectilinear motion. For example, the crank block 86 is used to reciprocate a blade holder shaft 116 in an up and down motion. The blade clamp 28 is connected to a lower end of the blade holder shaft 116. The blade clamp 28 includes a fixed clamp member 130 that is fixedly connected to the bottom of the blade holder shaft 116, a moveable clamp member 132 that is moveable with respect to the fixed clamp member 130, a collar 134 that is mounted over both the fixed and moveable clamp members 130 and 132, and a coil spring 136.
The crank block 86 includes a pin 118 on which a roller 120 is mounted. The roller 120 fits within a lateral slot 122 formed in a drive bracket 124. The blade holder shaft 116 is fixedly clamped between the drive bracket 124 and a drive clamp 126. The blade holder shaft 116 is also slidably mounted in a bearing holder assembly 126 that is pivotally mounted on a shaft 128 secured to the gear housing 50.
As the crank block 86 is rotated by the main drive gear 80, the roller 120 is laterally reciprocated within the lateral slot 122 and causes the drive bracket 124 to be oscillated up and down. Because the blade holder shaft 116 is fixedly clamped between the drive bracket 124 and the drive clamp 125, the reciprocation of the drive bracket 124 also causes a blade holder shaft 116 to be reciprocated in an up and down motion. As the blade holder shaft 116 is reciprocated in an up and down motion relative to the bearing holder assembly 126, the shaft 128 allows the bearing holder assembly 126 to pivot to accommodate orbital motion of a blade secured to the blade secured within the blade clamp 28.
FIGS. 4-6 provide various views of the shoe 24 in isolation from the remainder of the jigsaw 20. Referring to FIGS. 4-6, the blade guide 30 is connected to the pivot base 36 of the shoe 24 and is positioned within the main slot 26 defined by the shoe 24. As positioned in the slot 26, the blade guide 30 is preferably relatively close to the sub base 34. Consequently, when the jigsaw 20 is used to cut a workpiece, the blade guide 30 is positioned relatively close to the workpiece thereby enhancing the amount of lateral support provided to the blade.
The blade guide 30 is pivotally connected to a front portion 138 of the pivot base 36. The front portion 138 includes a sleeve 140 defining a cylindrical bore 139 aligned along a longitudinal axis L—L of the shoe 24. The blade guide 30 is pivotally mounted within the bore 139 of the sleeve 140. The blade guide 30 is retained in the sleeve 140 by a snap ring 148 that engages the rear side of the sleeve 140, and a radial shoulder 150 that engages a front side of the sleeve 140.
A front portion 146 of the blade guide 30 projects forwardly from the pivot base 36 into the main slot 26 of the shoe 24. The front portion 146 defines a front blade slot 152 sized for receiving a jigsaw blade. The front blade slot 152 has an open end that faces the front of the shoe 24. The blade guide 30 is aligned along and pivotally moveable about the longitudinal axis L—L.
The blade slot 152 of the blade guide 30 is formed by two spaced-apart projections 154. For example, the blade slot 152 is defined by opposing, generally planar inner surfaces 156 of the projections 154. The blade slot 152 is wide enough to allow a blade to freely reciprocate within the blade slot 152. While the blade is reciprocated, the inner surfaces 156 provide lateral support that resists twisting of the blade. In certain embodiments of the present invention, a threaded pin (not shown), or other type of pin, can extend transversely through the projections 154 into the slot 152. Such a pin is adapted to engage the blade within the blade slot 152. In this manner, the pin functions to effectively narrow the width of the slot 152.
As previously described, the position of the pivot base 36 can be longitudinally adjusted relative to the main base 32. For example, by loosening bolt 40, the pivot base 36 can be slid longitudinally along slots 44 and along the elongated opening 46 formed through the main base 32. By adjusting the longitudinal position of the pivot base 36 relative to the main base 32, the longitudinal position of the blade guide 30 within the main slot 26 can also be adjusted.
Referring now to FIG. 7a, a schematic front view of the jigsaw 20 is illustrated. As shown in FIG. 7a, the blade guide 30 is positioned in the main slot 26 and is in close proximity to a bottom surface 141 of the sub base 34. The inner surfaces 156 defining the blade slot 152 are shown facing and in close proximity to opposite lateral surfaces 158 of a blade 160.
Still referring to FIG. 7a, the pivot base 36 includes a convex surface 162 that is centered on or swung about the longitudinal axis L—L. Additionally, the housing 22 includes a concave surface 164 that is centered on or swung about the longitudinal axis L—L. The concave surface 164 is adapted to slide relative to the convex surface 162 when the housing 22 is pivoted relative to the pivot base 36.
The blade guide 30, the blade 160, and the housing 22 are all pivotally moveable about the same longitudinal axis L—L. To adjust a cutting angle of the blade 160 relative to the shoe 24, the housing 22 and blade 160 are pivoted as a unit about the longitudinal axis L—L. As the housing 22 and blade 160 are pivoted, contact between the blade 160 and the blade guide 30 causes the blade guide 30 to concurrently pivot about the longitudinal axis L—L. FIG. 7a shows the blade 160 aligned at a perpendicular cutting position relative to the bottom surface 141 of the shoe 24. FIG. 7b shows the blade 160 pivoted clockwise to a 45 degree cutting angle relative to the bottom surface 141 of the shoe 24. FIG. 7c shows the cutting blade 160 pivoted counterclockwise to a 45 degree cutting angle relative to the bottom surface 141 of the shoe 24.
FIGS. 8 and 9 illustrate an exemplary dust collection system used by the jigsaw 20. Referring to FIG. 9, the dust collection system includes a dust chamber 166 integrally formed beneath the main base 32. Although FIG. 9 shows the dust chamber 166 with the sub base 34 removed, it will be appreciated that when the sub base 34 is secured to the main base 32, the sub base 34 effectively seals the dust chamber 166.
Referring again to FIG. 9, the dust chamber 166 includes an outlet port 168 formed at the rear of the main base 32, and two inlet ports 170 positioned on opposite sides of the main slot 26 defined by the shoe 24. The inlet ports 170 are positioned on opposite sides of the blade 160 and are arranged and configured to suction sawdust generally transversely away from the lateral surfaces 150 of the blade 160. In other words, the inlet ports 170 draw dust laterally away from the lateral surfaces 158 as shown by arrows 172. For certain embodiments of the present invention, the inlet ports 170 draw or suction dust in a direction generally transverse with respect to the longitudinal axis L—L of the sub base 24.
The dust chamber 166 provides fluid communication between the outlet port 168 and the inlet ports 170. Specifically, the dust chamber 166 includes a main portion 174 and two channel portions 176 that are in fluid communication with the main portion 174. The two channel portions 176 branch outward from the main portion 174 and include portions that are laterally spaced apart and generally parallel. The channel portions 176 extend along opposite sides of the main slot 26 and each channel portion 176 is in fluid communication with a respective one of the inlet ports 170. In use of the dust collection system, an external source of vacuum is placed in fluid communication with the outlet port 168. The source of vacuum creates a vacuum within the dust chamber 166 that causes air and dust to be drawn into the dust chamber 166 through the inlet ports 170. From the inlet ports 170, the evacuated air and dust travel through the channel portions 176 to the main portion 174, and exit the dust chamber 166 through the outlet port 168.
To facilitate connecting source of vacuum to the outlet port 168, an adapter or dust wand 178 can be used. The dust wand 178 has one end that snaps or friction fits within the outlet port 168, and a second end adapted for connection to an external source of vacuum. For example, a vacuum hose can be friction fit over the second end of the dust wand 178. The dust wand 178 also includes a tab 180 that fits within an aperture defined by the rear of the housing 22 to provide vertical support to the dust wand 178.
FIGS. 10-12 illustrate a base clamping mechanism arranged and configured for selectively clamping the housing 22 at desired pivot locations relative to the shoe 24. As previously described with respect to FIG. 2, the base clamping mechanism includes the threaded adjustment shaft 62, the fixed ramp or wedge 58, the moveable ramp or wedge 60, and the shoulder bolt 54. The shoulder bolt 54 connects the pivot base 63 to the motor housing 52. For example, as shown in FIG. 11, the shoulder bolt 54 extends upward through the curved slot 56 defined by the pivot base 36 and also through a circular opening 182 defined by the motor housing 52. The circular opening 182 is defined by a lower wall 184 of the motor housing 152, while the curved slot 56 is defined by a curved upper wall 186 of the pivot base 36. An upper end of the shoulder bolt 54 is threaded within a captured nut 188 mounted within the motor housing 52. The captured nut 188 is mounted to resist rotation, and the shoulder bolt 54 is preferably threaded within the captured nut 188 such that a shoulder 190 of the shoulder bolt 154 presses against the bottom surface of the captured nut 188.
The fixed wedge 58 and the moveable wedge 60 are mounted on the shoulder bolt 54. For example, referring again to FIG. 11, the shoulder bolt 190 extends through a circular aperture 192 defined by the fixed wedge 58 and an elongated opening 194 defined by the moveable ramp 60. The circular aperture 192 has a diameter that is generally equal to the outer diameter of the shoulder bolt 54. The elongated opening 194 is elongated in a forward direction that is generally parallel to the longitudinal axis L—L of the shoe 24.
Both the fixed wedge 58 and the moveable wedge 60 are captured or trapped between the curved upper wall 186 of the pivot base 36 and a head 196 of the shoulder bolt 54. The moveable wedge 60 is mounted above the fixed wedge 58. The fixed wedge 58 includes a bottom surface 198 that engages the head 196 and is generally transversely aligned with respect to the shaft of the shoulder bolt 54. Additionally, the fixed ramp 58 also includes a top surface 200 aligned at an acute angle with respect to the bottom surface 198. The top surface 200 inclines upward in a forward direction with respect to the shoe 24.
The moveable wedge 60 includes a top surface 202 that engages the curved upper wall 186 of the pivot base 36, and a bottom surface 204 that engages the top surface 200 of the fixed wedge 58. The top surface 202 is generally transversely aligned with respect to the shaft of the shoulder bolt 54, and the bottom surface 204 is aligned at an acute angle with respect to the top surface 202. The bottom surface 204 of the moveable wedge 60 is generally parallel with respect to the top surface 200 of the fixed wedge 58.
The fixed and moveable ramps 58 and 60 cooperate with the shoulder bolt 54 to selectively clamp the motor housing 52 relative to the pivot base 36. When the clamping mechanism is tightened or clamped, the motor housing 52 is inhibited from pivoting relative to the pivot base 36 about the longitudinal axis L—L. By contrast, when the clamping mechanism is released, loosened or unclamped, the motor housing 52 can be manually pivoted relative to the pivot base 36 about the longitudinal axis L—L with minimal resistance.
To tighten the clamping mechanism, the moveable wedge 58 is forced in a forward direction relative to the fixed wedge 58. As the moveable wedge 60 moves in the forward direction, the moveable wedge 60 is wedged between the top surface 200 of the fixed wedge 58 and the bottom surface of the curved upper wall 186 of the pivot base 36. Such a wedge action places an axial tension on the shoulder bolt 54 and causes the lower wall 184 of the motor housing 52 and the upper wall 186 of the pivot base 36 to be drawn together. For example, the wedge action pushes the head 196 of the shoulder bolt 54 downward relative to the upper wall 186 of the pivot base 36 causing the shoulder bolt 54 to pull downward on the captured nut 188. As the captured nut 188 is pulled downward, the lower wall 184 of the motor housing 52 and the upper wall 186 of the pivot base 36 are compressed together. As the lower and upper walls 184 and 186 are compressed together by the shoulder bolt 54, enhanced friction is generated between the concave surface 164 of the motor housing 52 and the convex surface 162 of the pivot base 36. Such enhanced friction resists movement of the motor housing 52 relative to the pivot base 36. Consequently, the motor housing 52 is effectively locked or clamped relative to the pivot base 36.
To release the clamping mechanism, the moveable wedge 60 is moved in a rearward direction relative to the fixed wedge 58. As the moveable wedge 58 moved rearward, the head 196 of the shoulder bolt 54 is allowed to move toward the curved upper wall 186 thereby reducing the pressure between the lower wall 184 of the motor housing 52 and the upper wall 186 of the pivot base 36. As the pressure is reduced, the friction between the convex and concave surfaces 162 and 164 is also reduced such that the motor housing 52 can be manually pivoted relative to the pivot base 36. When the motor housing 52 is pivoted relative to the pivot base 36, the shoulder bolt 54 slides along the curved slot 56 defined by the pivot base 36. Once the motor housing 52 has been moved to a desired pivot location, the clamp mechanism is re-tightened to retain the housing 52 in the desired position.
Referring to FIGS. 10 and 11, the pivot base 36 also defines a plurality of depressions 206. The depressions 206 are arranged and configured to receive ball detents 208 mounted within the motor housing 52. The ball detents 208 are biased downward by detent springs 210. Each of the depressions 206 corresponds to a particular cutting angle that may be desired. For example, the depressions 206 can be located at positions corresponding to a perpendicular cutting angle as well as cutting angles of 15 degrees, 30 degrees, and 45 degrees offset from perpendicular. The ball detents 208 and depressions 206 help a user quickly and precisely set the jigsaw 20 at a desired cutting angle.
It will be appreciated that a variety of arrangements can be used to move the moveable wedge 60 relative to the fixed wedge 58. As shown in FIGS. 11 and 12, the threaded adjustment shaft 62 is used to control the position of the moveable wedge 60. The adjustment shaft 62 is aligned generally parallel with respect to the longitudinal axis L—L and is rotatably mounted in a downwardly opening slot 212 formed in the motor housing 52. The adjustment shaft 62 is retained in the slot 212 by a cross pin 214. A flange 216 limits axial movement of the adjustment shaft 62 relative to the motor housing 52 and the pivot base 36. For example, as shown in FIG. 11, the flange is captured between the motor housing 52 and the pivot base 36.
The adjustment shaft 62 has a threaded end 218 having external threads. The threaded end 218 is threaded within a longitudinal slot 220 defined by the moveable wedge 60. The longitudinal slot 220 includes internal threads that mate with the external threads of the threaded end 218. When the adjustment shaft 62 is rotated in a first direction, the internal and external threads cooperate to force the moveable wedge 60 in the forward direction toward the fixed wedge 58. By contrast, when the adjustment shaft 62 is rotated in a second direction opposite to the first direction, the internal and external threads cooperate to pull the moveable wedge 60 rearward away from the fixed wedge 58.
The adjustment shaft 60 is also equipped with a lever arm 222 for increasing the manual torque that can be applied to the adjustment shaft 62. The lever arm 222 is telescopically mounted within a handle portion 224 of the adjustment shaft 62. By telescopically extending the lever arm 222 outward from the handle portion 224, and pivoting the lever arm 222 90 degrees about pivot pin 226, the lever arm 222 can be used to increase the manual torque applied to the adjustment shaft 62.
Referring back to FIG. 2, the basic components of the blade clamp 28 used by the jig saw 20 include the fixed clamp member 130, the moveable clamp member 132, the collar 134, and the coil spring 136. When assembled, the blade clamp 28 is adapted to releasably clamp or secure a blade to the bottom end of the blade holder shaft 116.
Referring now to FIGS. 13a-13 d, various views of the moveable clamp member 132 are shown. The moveable clamp member 132 includes a main body 300. A clamping face 264 and an inner follower surface 260 are formed on opposite sides of the main body 300. First and second axially aligned projections 302 and 303 project transversely outward from the clamping face 264. The first projection 302 is generally cylindrical, while the second projection 303 has a ramped surface 305. The moveable clamp member 132 also includes a rounded end 304 and transverse wings 306 that project transversely outward from the main body 300.
Types of Jigsaw Blades
The first and second projections 302 and 303 are arranged and configured to secure a universal blade to the moveable clamp member 132. For example, FIGS. 14a and 14 b show the moveable clamp member 132 connected to a universal blade 324. As shown in FIGS. 14a and 14 b, the second projection 303 of the moveable clamp member 132 fits within an opening 326 of the universal blade 324, while first projection 302 of the moveable clamp member 132 fits within a top notch 328 formed on the universal blade 324. The projections 302 and 303 of the moveable clamp member 132 inhibit axial movement of the universal blade 324 relative to the moveable clamp member 132.
Referring back to FIGS. 13a-13 d, the moveable clamp member 132 also includes a jaw lever 246 that projects outward from the inner follower surface 260. The jaw lever 246 includes an extension 250 connected to the main body 300 of the moveable clamp member 132. The jaw lever 246 also includes a distally located jaw tab 248 having outer follower surfaces 262 positioned on opposite sides of the extension 250. The outer follower surfaces 262 on the jaw tab 248 generally oppose the inner follower surface 260 formed on the main body 300.
FIGS. 15a-15 c illustrate the fixed clamp member 130 of the blade holder 28. The fixed clamp member 130 is fixedly connected to the bottom end of the blade holder shaft 116. The shaft 116 includes a slot 117 for facilitating clamping the shaft 116 between the drive bracket 124 and the drive clamp 126 (shown in FIG. 2).
Referring to FIGS. 15a-15 c, the fixed clamp member 130 includes a main axial slot 252 aligned along a longitudinal axis A—A of the shaft 116. The main axial slot 252 is sized for receiving the moveable clamp member 132. A curved end 253 of the main axial slot 252 is sized to receive the rounded end 304 of the moveable clamp member 130. A secondary axial slot 255 defined by the fixed clamp member 130 is sized to receive the first and second projections 302 and 303 of the moveable clamp member 130 when the moveable clamp member 132 is mounted within the main axial slot 252.
The fixed clamp member 130 also includes first and second transverse slots 308 and 310. The first transverse slot 308 is sized and shaped to receive tangs of a tang blade. The second transverse slot 310 is arranged and configured to receive the transverse wings 306 of the moveable clamp member 132 when the moveable clamp member 132 is mounted within the main axial slot 252. The first and second transverse slots 308 and 310 are defined by first, second and third shoulders sets 312, 313 and 314. Each of the shoulder sets 312, 313 and 314 includes a separate shoulder positioned on opposite sides of a gap 316 that corresponds to the width of the main axial slot 252. The gap 316 is sized for receiving either a tang blade or a universal blade.
FIGS. 16a and 16 b show the fixed clamp member 130 with a tang blade trapped therein. As shown in FIGS. 16a and 16 b, oppositely disposed tangs 320 of the tang blade 319 fit within the first transverse slot 308 of the fixed clamp member 130. The first and second shoulder sets 312 and 313 inhibit axial movement of the blade 319 relative to the fixed clamp member 130.
FIG. 17 illustrates the fixed clamp member 130 with the moveable clamp member 132 mounted in the main axial slot 252. As shown in FIG. 17, the transverse wings 302 of the moveable clamp member 132 fit within the second transverse slot 310 of the fixed clamp member 130. The transverse wings 306 function to transfer axial loading from a universal blade mounted on the moveable clamp member 132 directly to the blade holder shaft 116 through the fixed clamp member 130.
FIGS. 18 and 19 provide assembled views of the blade clamp 28. As shown in FIGS. 18 and 19, the moveable clamp member 132 is mounted in the main axial slot 252 of the fixed clamp member 130 (as shown in FIG. 17). The collar 134 is mounted over both the fixed clamp member 130 and the moveable clamp member 132. The collar 134 is pivotally moveable relative to the fixed and moveable clamp members 130 and 132 about the longitudinal axis A—A of the shaft 116. The spring 136 is mounted over the shaft 116 and has a first end 230 fixedly secured relative to the collar 134 (as shown in FIG. 19), and a second end 232 fixedly secured relative to the shaft 116 (as shown in FIG. 18).
Referring now to FIGS. 20a and 20 b, the collar 134 defines a circumferential slot 234 having a first end 240 positioned opposite from a second end 244. The collar 134 also defines an axial access slot 236 located adjacent to the second end 244 of the circumferential slot 234. The collar 134 further includes a radial collar tab 242 positioned adjacent to the first end 240 of the circumferential slot 234. The extension 250 of the jaw lever 246 extends outward through the circumferential slot 234, and jaw tab 248 is positioned outside the collar 134.
The collar 134 is pivotally moveable off the longitudinal axis A—A between a blade clamping position (shown in FIG. 20a) where the blade clamp 28 is adapted to clamp a blade, and a blade release position (shown in FIG. 20b) where a blade can be inserted into or removed from the blade clamp 28. In the blade clamping position, the jaw lever 246 is located adjacent to the second end 244 of the circumferential slot 234. In the blade release position, the jaw lever 246 is located adjacent to the first end 240 of the circumferential slot 234. The spring 136 biases the collar 134 toward the blade clamping position.
A user preferably moves the collar 134 from the position of clamping position of FIG. 20a to the blade release position of FIG. 20b by manually pushing the collar and jaw tabs 242 and 248 toward one another. As the collar and jaw tabs 242 and 248 are pushed toward one another, the collar 134 pivots about the longitudinal axis A—A against resistance provided by the spring 136. Also, as the collar 134 is pivoted, relative movement is generated between the circumferential slot 234 and the jaw lever 246 such that the first end 240 of the circumferential slot 234 moves toward the jaw lever 246. With the blade clamp 28 manually held in the position of FIG. 20b, a blade can be inserted in the blade clamp 28. Once the blade is inserted in the blade clamp 28, the collar and jaw tabs 242 and 248 can be released thereby allowing the spring 136 to return the blade clamp 28 to the position of FIG. 20a.
FIG. 21 a is a bottom view of the blade clamp 28 showing the blade clamp 28 in the blade clamping position of FIG. 20a. In the blade clamping position, the clamping face 264 of the moveable clamp member 232 is in close proximity to the corresponding clamping face 266 formed on the fixed clamp member 130. FIG. 21a is a bottom view of the blade clamp 28 showing the blade clamp 28 in the blade release position of FIG. 20b. As shown in FIG. 21b, the moveable clamp member 132 is pulled away from the fixed clamp member 130 such that a relative large spacing S exists between the clamping faces 264 and 266. The spacing is preferably sufficiently large to allow a jigsaw blade to be inserted between the clamping faces 264 and 266, or removed from between the clamping faces 264 and 266.
A cam mechanism is used to move the moveable clamp member 232 between the clamping position of FIG. 21a and the blade release position of FIG. 21b. For example, as shown in FIGS. 21a and 21 b, the collar 134 includes a cam wall or portion 254 that curves gradually away from the axis A—A of rotation of the collar 134. The circumferential slot 234 (shown in FIGS. 20a and 20 b) is formed through the cam portion 254. Referring to FIGS. 21a and 21 b, the cam portion 254 includes inner cam surfaces 256 and outer cam surfaces 258. The inner cam surfaces 256 face or engage the inner follower surface 260 formed on the moveable clamp member 232. Similarly, the outer cam surfaces 258 face or engage outer follower surfaces 262 formed by the jaw tab 248.
With respect to FIG. 21a, by pivoting the collar 134 in a counterclockwise direction about the axis of rotation A—A, the collar tab 242 is moved toward the jaw tab 248. As the collar 134 is pivoted, the cam portion 154 of the collar 134 slides along the moveable clamp member 132. As the cam portion 254 slides relative to the moveable clamp member 132, the outer cam surfaces 258 engage the outer follower surfaces 262 causing the moveable clamp member 132 to be pulled away from the fixed clamp member 130. In this manner, the moveable clamp member 132 is moved from the blade clamping position of FIG. 21a to the blade release position of FIG. 21b.
After a blade has been inserted into or removed from between the clamping faces 264 and 266, the collar tab 242 can be released causing the spring to pivot the collar 134 clockwise about the pivot axis A—A. As the collar 134 pivots clockwise about the pivot axis A—A, the inner follower surface 260 engages the inner cam surfaces 256 causing the moveable clamp member 132 to be pushed toward the fixed clamp member 130. In this manner, the moveable clamp member 132 is moved from the blade release position of FIG. 21b back to the clamping position of FIG. 21a.
The blade clamp 28 is preferably assembled by first placing the moveable clamp member 132 within the main axial slot 253 of the fixed clamping member 130. Next, the collar is inserted over the shaft 116 and slid downward over both the moveable and fixed clamp members 132 and 130. As the collar 134 is slide downward, the collar is oriented such that the jaw lever 246 is received in the axial access slot 236. The jaw lever 246 travels through the access slot 236 and enters the circumferential slot 234. Once the jaw lever is positioned in the circumferential slot 234, the spring 136 is slid over the shaft 116 and positioned on top of the collar 134. Finally, the first end 230 of the spring 136 is fixedly secured to the collar 134, and the second end 232 of the spring 136 is fixedly secured to the shaft 116.
With regard to the foregoing description, it is to be understood that changes may be made in detail, especially in matters of the shape, size and arrangement of the parts without departing from the scope of the present invention. It is intended that the specification and depicted embodiment be considered exemplary only, with a true scope and spirit of the invention being indicated by the broad meaning of the following claims.
Claims ( 23 )
a second clamp member positioned within the main slot, the second clamp member being moveable relative to the first clamp member between a first position in which the first and second clamp members are adapted to clamp a blade, and a second position in which the blade can be inserted between the first and second clamp members; and
a collar being pivotally moveable in first and second opposite directions relative to the first and second clamp members, the collar including a cam portion that moves the second clamp member toward the first position when the collar is pivoted in the first direction, and also moves the second clamp member toward the second position when the collar is pivoted in the second direction.
The blade clamp of claim 1, wherein the first clamp member is fixedly connected to a reciprocating shaft.
The blade clamp of claim 1, wherein at least one of the first and second clamp members includes a projection arranged and configured to fit within a mounting opening of a universal blade.
The blade clamp of claim 1, wherein at least one of the first and second clamp members includes a first projection arranged and configured to fit within a mounting opening of a universal blade, and a second projection arranged and configured to fit within a top notch of the universal blade.
The blade clamp of claim 1, wherein at least one of the first and second clamp members includes a transverse slot arranged and configured for trapping the oppositely disposed tangs of a tang blade.
The blade clamp of claim 3, wherein at least one of the first and second clamp members includes a transverse slot arranged and configured for trapping the oppositely disposed tangs of a tang blade.
The blade clamp of claim 7, wherein the projection is formed on the second clamp member, and the transverse slot is defined by the first clamp member.
The blade clamp of claim 1, wherein the first clamp member includes first and second shoulders positioned on opposite sides of the main slot, the shoulders being arranged and configured for engaging oppositely disposed tangs of a tang blade.
The blade clamp of claim 9, wherein the projection is formed on the second clamp member and extends toward the first clamp member into the main slot.
The blade clamp of claim 1, wherein at least one of the first and second clamp members defines a transverse slot, and the other of the first and second clamp members includes transverse projections that fit within the transverse slot to allow axial loading to be transferred between the first and second clamp members.
The blade clamp of claim 11, wherein the transverse slot is formed by the first clamp member, and the transverse projections are formed on the second clamp member.
The blade clamp of claim 1, further comprising a spring that biases the collar in the first direction.
The blade clamp of claim 1, wherein the cam portion of the collar curves gradually away from a pivot axis of the collar.
The blade clamp of claim 14, wherein the cam portion defines a circumferential slot, and the second clamp member includes an extension member that extends through the circumferential slot.
The blade clamp of claim 15, wherein the second clamp member includes a tab positioned at a distal end of the extension member at a location outside the collar.
first and second clamp members moveable between a blade release position in which a blade can be inserted between and removed from between the first and second clamp members, and a clamping position in which the first and second clamp members are adapted to clamp the blade thereinbetween;
the first clamp member including first and second spaced-apart shoulders separated by a gap, the first and second shoulders extending from the first clamp member toward the second clamp member, the first and second shoulders being arranged and configured to trap a tang blade within the blade clamp by engaging oppositely disposed tangs of a tang blade when the tang blade is positioned within the gap;
the second clamp member including a projection extending from the second clamp member toward the first clamp member, the projection being arranged and configured to fit within a mounting opening of a universal blade when the universal blade is positioned in the gap between the shoulders; and
wherein the first blade clamp includes a transverse slot, and the second blade clamp includes transverse wines that fit within the transverse slot.
The blade clamp of claim 17, wherein the projection is positioned in general axial alignment with the gap between the first and second shoulders.
a second clamp member having a portion that opposes the first clamp member, the second clamp member being moveable relative to the first clamp member between a first position in which the first and second clamp members are adapted to clamp a blade, and a second position in which the blade can be inserted between the first and second clamp members;
a collar that is pivotally moveable in first and second opposite directions relative to the first and second clamp members, the collar including a cam portion for positively moving the second clamp member between the first and second positions, the second clamp member being forced by the cam portion toward the first position when the collar is pivoted in the first direction, and the second clamp member being forced by the cam portion toward the second position when the collar is pivoted in the second direction; and
The blade clamp of claim 19, wherein the cam portion of the collar curves gradually away from a pivot axis of the collar.
The blade clamp of claim 20, wherein the cam portion defines a circumferential slot, and the second clamp member includes an extension member that extends through the circumferential slot.
The blade clamp of claim 21, wherein the second clamp member includes a finger grip positioned at a distal end of the extension member at a location outside the collar.
The blade clamp of claim 22, wherein an outer surface of the cam-portion engages the finger grip to positively move the second clamp member toward the second position when the collar is pivoted in the second direction.
US09/113,394 1998-07-10 1998-07-10 Blade clamping system for a jigsaw Expired. Lifetime US6178646B1 ( en )
Priority Applications (2)
US09/113,394 US6178646B1 ( en ) | 1998-07-10 | 1998-07-10 | Blade clamping system for a jigsaw |
EP99305422A EP0970771A3 ( en ) | 1998-07-10 | 1999-07-08 | Jigsaw blade clamping system with cam-operated clamping member |
ID=22349143
Cited By (34)
US20020124419A1 ( en ) | 2001-03-01 | 2002-09-12 | Shinji Hirabayashi | Blade clamps suitable for reciprocating power tools |
US6453565B1 ( en ) | 2001-01-24 | 2002-09-24 | Porter-Cable/Delta | Universal blade adapter |
US20040098870A1 ( en ) | 2002-11-25 | 2004-05-27 | One World Technologies Limited | Toolless blade holder for a reciprocating tool |
US20050120568A1 ( en ) | 2003-10-28 | 2005-06-09 | Mike Wilson | Blade clamp for reciprocating saw |
US20050283984A1 ( en ) | 2004-06-29 | 2005-12-29 | Neil Walmsley | Shoe assembly for power tool power tool incorporating such assembly |
US20060288647A1 ( en ) | 2005-06-27 | 2006-12-28 | 3M Innovative Properties Company | Coated abrasive article, and method of making and using the same |
US20070000368A1 ( en ) | 2005-06-29 | 2007-01-04 | Credo Technology Corporation And Robert Bosch Gmbh. | Tool-less adjustable foot assembly for a power hand tool |
US20090077814A1 ( en ) | 2007-09-21 | 2009-03-26 | Black Decker Inc. | Cutting Angle Indicator in Jigsaw Housing with Dust Extraction |
US20090077816A1 ( en ) | 2007-09-21 | 2009-03-26 | Black Decker Inc. | Adjustable and removable keel assembly and blade guide for a jigsaw |
US20090077819A1 ( en ) | 2007-09-21 | 2009-03-26 | Black Decker Inc. | Cutting Angle Indicator in Jigsaw Housing with Positive Lock in Separately Assembled Shoe Sub-Assembly |
US20090077818A1 ( en ) | 2007-09-21 | 2009-03-26 | Black Decker Inc. | Housing of a cutting tool including blade storage, integral blade guard and motor ventilation pathway |
US20100162579A1 ( en ) | 2008-03-07 | 2010-07-01 | Michael Naughton | Reciprocating power tool having a counterbalance device |
USD642028S1 ( en ) | 2010-05-21 | 2011-07-26 | Irwin Industrial Tool Company | Reciprocating saw blade |
US8210081B2 ( en ) | 2007-06-12 | 2012-07-03 | Irwin Industrial Tool Company | Reciprocating saw blade having variable-height teeth and related method |
US8230607B2 ( en ) | 2008-05-09 | 2012-07-31 | Milwaukee Electric Tool Corporation | Keyless blade clamp for a power tool |
USD688543S1 ( en ) | 2012-03-20 | 2013-08-27 | Milwaukee Electric Tool Corporation | Saw blade |
US8578615B2 ( en ) | 2011-09-12 | 2013-11-12 | Black Decker Inc. | Jigsaw with deployable keel and tiltable shoe |
US8813372B2 ( en ) | 2007-09-14 | 2014-08-26 | Milwaukee Electric Tool Corporation | Blade clamp mechanism |
USD725450S1 ( en ) | 2013-11-13 | 2015-03-31 | Irwin Industrial Tool Company | Reciprocating saw blade |
USD729600S1 ( en ) | 2014-05-06 | 2015-05-19 | Milwaukee Electric Tool Corporation | Saw blade |
USD732914S1 ( en ) | 2013-11-13 | 2015-06-30 | Irwin Industrial Tool Company | Reciprocating saw blade |
US9156097B2 ( en ) | 2012-03-20 | 2015-10-13 | Milwaukee Electric Tool Corporation | Reciprocating saw blade clamp |
US9248518B2 ( en ) | 2010-06-30 | 2016-02-02 | Irwin Industrial Tool Company | Saw blade tooth form for abusive cutting applications |
US9375796B2 ( en ) | 2010-05-07 | 2016-06-28 | Irwin Industrial Tool Company | Saw blade with robust tooth form |
US9475141B2 ( en ) | 2011-08-04 | 2016-10-25 | Milwaukee Electric Tool Corporation | Reciprocating saw blade |
US9757807B2 ( en ) | 2013-03-14 | 2017-09-12 | Irwin Industrial Tool Company | Reciprocating saw blade with curved cutting edge |
US9827623B2 ( en ) | 2007-09-21 | 2017-11-28 | Black Decker Inc. | Control of reciprocation speed and orbital magnitude of a jigsaw with a plurality of material and/or task descriptive icons |
US9899899B2 ( en ) | 2013-10-25 | 2018-02-20 | Black Decker Inc. | Handheld power tool with compact AC switch |
US10413980B2 ( en ) | 2011-04-01 | 2019-09-17 | Milwaukee Electric Tool Corporation | Reciprocating saw, such as a jigsaw |
US10537951B2 ( en ) | 2017-08-16 | 2020-01-21 | Black Decker Inc. | Band saw blade for cutting structural workpieces |
US10960474B2 ( en ) | 2017-05-31 | 2021-03-30 | Bosch Power Tools (China) Co., Ltd. | Power tool |
US11007588B2 ( en ) | 2010-04-22 | 2021-05-18 | Milwaukee Electric Tool Corporation | Saw blade |
US11141805B2 ( en ) | 2010-04-22 | 2021-10-12 | Milwaukee Electric Tool Corporation | Saw blade |
US11413693B2 ( en ) | 2017-05-16 | 2022-08-16 | Milwaukee Electric Tool Corporation | Saw blade |
Patent Citations (24)
US2996089A ( en ) | 1960-08-25 | 1961-08-15 | Black Decker Mfg Co | Self-aligning anti-splintering insert for shoe of jig saw |
US3303861A ( en ) | 1964-07-06 | 1967-02-14 | Rockwell Mfg Co | Saw structure |
US3339598A ( en ) | 1964-08-12 | 1967-09-05 | Rockwell Mfg Co | Saw structures |
US3547166A ( en ) | 1968-07-03 | 1970-12-15 | Singer Co | Chuck attachment for sabre saws |
DE2546527A1 ( en ) | 1975-10-17 | 1977-04-28 | Bosch Gmbh Robert | CRAFT MACHINE |
US4090297A ( en ) | 1975-10-17 | 1978-05-23 | Robert Bosch Gmbh | Power tool with dust collecting arrangement |
GB2069406A ( en ) | 1980-02-20 | 1981-08-26 | Bosch Gmbh Robert | Mounting of a keyhole-saw blade |
US4512078A ( en ) | 1982-04-20 | 1985-04-23 | Black Decker Inc. | Jig saw with orbital mechanism |
US4665617A ( en ) | 1984-06-01 | 1987-05-19 | Peter Maier | Compass saw for cutting workpieces of wood, plastics and metal |
EP0215073B2 ( en ) | 1985-03-16 | 1994-03-16 | Festo KG | Compass saw |
US4628605A ( en ) | 1985-06-10 | 1986-12-16 | Porter-Cable Corporation | Orbital bayonet saw |
US4730397A ( en ) | 1985-08-09 | 1988-03-15 | Black Decker, Inc. | Jig saw with two-piece shoe |
US4837935A ( en ) | 1986-04-19 | 1989-06-13 | Peter Maier | Jig saw |
US5012583A ( en ) | 1987-04-10 | 1991-05-07 | Robert Bosch Gmbh | Compass saw |
US5165173A ( en ) | 1988-03-15 | 1992-11-24 | Robert Bosch Gmbh | Jigsaw |
US5205043A ( en ) | 1991-01-23 | 1993-04-27 | Black Decker Inc. | Pendulum jigsaws |
EP0544129A1 ( en ) | 1991-11-27 | 1993-06-02 | ATLAS COPCO ELEKTROWERKZEUGE GmbH | Holder for a sabre saw |
DE4313718A1 ( en ) | 1993-04-27 | 1994-11-03 | Bernd Hoeschele | Device for holding a saw blade |
JPH07266129A ( en ) | 1994-03-24 | 1995-10-17 | Makita Corp | Blade tool fitting device for reciprocating cutting tool |
GB2296888A ( en ) | 1994-11-29 | 1996-07-17 | Milwaukee Electric Tool Corp | Keyless clamp assembly for reciprocating tool |
WO1996028274A1 ( en ) | 1995-03-16 | 1996-09-19 | Robert Bosch Gmbh | Saw blade clamping device for piercing saw machines |
DE19532494A1 ( en ) | 1995-09-02 | 1997-03-06 | Festo Tooltechnic Kg | Rapid tensioner for machine tool, especially fret saw |
DE19609388A1 ( en ) | 1996-03-01 | 1997-09-04 | Black Decker Inc | Motor-driven compass saw |
US5727322A ( en ) | 1996-12-31 | 1998-03-17 | Black Decker Inc. | Adjustable shoe for a jig saw |
Cited By (52)
US6453565B1 ( en ) | 2001-01-24 | 2002-09-24 | Porter-Cable/Delta | Universal blade adapter |
US20020124419A1 ( en ) | 2001-03-01 | 2002-09-12 | Shinji Hirabayashi | Blade clamps suitable for reciprocating power tools |
US6735876B2 ( en ) | 2001-03-01 | 2004-05-18 | Makita Corporation | Blade clamps suitable for reciprocating power tools |
US7040023B2 ( en ) | 2002-11-25 | 2006-05-09 | Eastway Fair Company Limited | Toolless blade holder for a reciprocating tool |
US20040098870A1 ( en ) | 2002-11-25 | 2004-05-27 | One World Technologies Limited | Toolless blade holder for a reciprocating tool |
US20050120568A1 ( en ) | 2003-10-28 | 2005-06-09 | Mike Wilson | Blade clamp for reciprocating saw |
US20050283984A1 ( en ) | 2004-06-29 | 2005-12-29 | Neil Walmsley | Shoe assembly for power tool power tool incorporating such assembly |
US20060288647A1 ( en ) | 2005-06-27 | 2006-12-28 | 3M Innovative Properties Company | Coated abrasive article, and method of making and using the same |
US20070000368A1 ( en ) | 2005-06-29 | 2007-01-04 | Credo Technology Corporation And Robert Bosch Gmbh. | Tool-less adjustable foot assembly for a power hand tool |
US7503121B2 ( en ) | 2005-06-29 | 2009-03-17 | Robert Bosch Gmbh | Tool-less adjustable foot assembly for a power hand tool |
US8210081B2 ( en ) | 2007-06-12 | 2012-07-03 | Irwin Industrial Tool Company | Reciprocating saw blade having variable-height teeth and related method |
US8813373B2 ( en ) | 2007-09-14 | 2014-08-26 | Milwaukee Electric Tool Corporation | Blade clamp mechanism |
US8813372B2 ( en ) | 2007-09-14 | 2014-08-26 | Milwaukee Electric Tool Corporation | Blade clamp mechanism |
US10029322B2 ( en ) | 2007-09-21 | 2018-07-24 | Black Decker Inc. | Housing of a cutting tool including blade storage, integral blade guard and motor ventilation pathway |
US20090077819A1 ( en ) | 2007-09-21 | 2009-03-26 | Black Decker Inc. | Cutting Angle Indicator in Jigsaw Housing with Positive Lock in Separately Assembled Shoe Sub-Assembly |
US9844823B2 ( en ) | 2007-09-21 | 2017-12-19 | Black Decker Inc. | Jigsaw with cutting angle indicator in jigsaw housing assembly |
US8033026B2 ( en ) | 2007-09-21 | 2011-10-11 | Black Decker Inc. | Adjustable and removable keel assembly and blade guide for a jigsaw |
US20090077818A1 ( en ) | 2007-09-21 | 2009-03-26 | Black Decker Inc. | Housing of a cutting tool including blade storage, integral blade guard and motor ventilation pathway |
US9981327B2 ( en ) | 2007-09-21 | 2018-05-29 | Black Decker Inc. | Cutting angle indicator in jigsaw housing with dust extraction |
US9827623B2 ( en ) | 2007-09-21 | 2017-11-28 | Black Decker Inc. | Control of reciprocation speed and orbital magnitude of a jigsaw with a plurality of material and/or task descriptive icons |
US20090077814A1 ( en ) | 2007-09-21 | 2009-03-26 | Black Decker Inc. | Cutting Angle Indicator in Jigsaw Housing with Dust Extraction |
US20090077816A1 ( en ) | 2007-09-21 | 2009-03-26 | Black Decker Inc. | Adjustable and removable keel assembly and blade guide for a jigsaw |
US8407902B2 ( en ) | 2008-03-07 | 2013-04-02 | Milwaukee Electric Tool Corporation | Reciprocating power tool having a counterbalance device |
US9061411B2 ( en ) | 2008-03-07 | 2015-06-23 | Milwaukee Electric Tool Corporation | Reciprocating power tool having a counterbalance device |
US20100162579A1 ( en ) | 2008-03-07 | 2010-07-01 | Michael Naughton | Reciprocating power tool having a counterbalance device |
US8230607B2 ( en ) | 2008-05-09 | 2012-07-31 | Milwaukee Electric Tool Corporation | Keyless blade clamp for a power tool |
US11433467B2 ( en ) | 2010-04-22 | 2022-09-06 | Milwaukee Electric Tool Corporation | Saw blade |
US11141805B2 ( en ) | 2010-04-22 | 2021-10-12 | Milwaukee Electric Tool Corporation | Saw blade |
US11007588B2 ( en ) | 2010-04-22 | 2021-05-18 | Milwaukee Electric Tool Corporation | Saw blade |
USD977926S1 ( en ) | 2010-04-22 | 2023-02-14 | Milwaukee Electric Tool Corporation | Saw blade |
US9375796B2 ( en ) | 2010-05-07 | 2016-06-28 | Irwin Industrial Tool Company | Saw blade with robust tooth form |
USD693661S1 ( en ) | 2010-05-21 | 2013-11-19 | Irwin Industrial Tool Company | Reciprocating saw blade |
USD714602S1 ( en ) | 2010-05-21 | 2014-10-07 | Irwin Industrial Tool Company | Reciprocating saw blade |
USD642028S1 ( en ) | 2010-05-21 | 2011-07-26 | Irwin Industrial Tool Company | Reciprocating saw blade |
US9248518B2 ( en ) | 2010-06-30 | 2016-02-02 | Irwin Industrial Tool Company | Saw blade tooth form for abusive cutting applications |
US10413980B2 ( en ) | 2011-04-01 | 2019-09-17 | Milwaukee Electric Tool Corporation | Reciprocating saw, such as a jigsaw |
US9475141B2 ( en ) | 2011-08-04 | 2016-10-25 | Milwaukee Electric Tool Corporation | Reciprocating saw blade |
US10226829B2 ( en ) | 2011-08-04 | 2019-03-12 | Milwaukee Electric Tool Corporation | Reciprocating saw blade |
US8578615B2 ( en ) | 2011-09-12 | 2013-11-12 | Black Decker Inc. | Jigsaw with deployable keel and tiltable shoe |
USD723892S1 ( en ) | 2012-03-20 | 2015-03-10 | Milwaukee Electric Tool Corporation | Saw blade |
US9156097B2 ( en ) | 2012-03-20 | 2015-10-13 | Milwaukee Electric Tool Corporation | Reciprocating saw blade clamp |
USD688543S1 ( en ) | 2012-03-20 | 2013-08-27 | Milwaukee Electric Tool Corporation | Saw blade |
US9757807B2 ( en ) | 2013-03-14 | 2017-09-12 | Irwin Industrial Tool Company | Reciprocating saw blade with curved cutting edge |
US10343229B2 ( en ) | 2013-03-14 | 2019-07-09 | Black Decker Inc. | Reciprocating saw blade with curved cutting edge |
US10857605B2 ( en ) | 2013-03-14 | 2020-12-08 | Black Decker Inc. | Reciprocating saw blade with curved cutting edge |
US9899899B2 ( en ) | 2013-10-25 | 2018-02-20 | Black Decker Inc. | Handheld power tool with compact AC switch |
USD732914S1 ( en ) | 2013-11-13 | 2015-06-30 | Irwin Industrial Tool Company | Reciprocating saw blade |
USD725450S1 ( en ) | 2013-11-13 | 2015-03-31 | Irwin Industrial Tool Company | Reciprocating saw blade |
USD729600S1 ( en ) | 2014-05-06 | 2015-05-19 | Milwaukee Electric Tool Corporation | Saw blade |
US11413693B2 ( en ) | 2017-05-16 | 2022-08-16 | Milwaukee Electric Tool Corporation | Saw blade |
US10960474B2 ( en ) | 2017-05-31 | 2021-03-30 | Bosch Power Tools (China) Co., Ltd. | Power tool |
US10537951B2 ( en ) | 2017-08-16 | 2020-01-21 | Black Decker Inc. | Band saw blade for cutting structural workpieces |
Similar Documents
US6178646B1 ( en ) | 2001-01-30 | Blade clamping system for a jigsaw |
US6357124B1 ( en ) | 2002-03-19 | Clamp system for a jigsaw tilt base |
US6230411B1 ( en ) | 2001-05-15 | Blade guide system for a jigsaw |
EP0970771A2 ( en ) | 2000-01-12 | Jigsaw blade clamping system with cam-operated clamping member |
US20200030897A1 ( en ) | 2020-01-30 | Reciprocating saw |
US6249979B1 ( en ) | 2001-06-26 | Orbital reciprocating saw |
US7096589B2 ( en ) | 2006-08-29 | Bearing for a reciprocating shaft of a reciprocating saw |
EP0748665B1 ( en ) | 2003-03-19 | A reciprocating saw blade clamp |
AU2003257883B2 ( en ) | 2008-09-25 | Support mechanism for reciprocating tool and tool incorporating such mechanism |
US20060117580A1 ( en ) | 2006-06-08 | Power tool and method of operating the same |
EP1884304A1 ( en ) | 2008-02-06 | Bearing for a reciprocating shaft of a reciprocating saw |
AU2004204061B2 ( en ) | 2008-12-11 | Clamping arrangement for receiving a saw blade in multiple orientations |
US6009627A ( en ) | 2000-01-04 | Saw blade clamping arrangement for a power tool |
US6023848A ( en ) | 2000-02-15 | Saw blade clamping arrangement for a power tool |
EP0810050B1 ( en ) | 2002-08-14 | Saw blade clamping arrangement for a power tool |
US20020014014A1 ( en ) | 2002-02-07 | Blade ejection mechanism for a saw blade clamping arrangement of a power tool |
US20210213548A1 ( en ) | 2021-07-15 | Reciprocating saw |
EP1010489A2 ( en ) | 2000-06-21 | An arrangement for clamping a saw blade |
GB2271735A ( en ) | 1994-04-27 | Reciprocating drive in hand held machine tools |
US11311952B2 ( en ) | 2022-04-26 | Reciprocating saw |
EP2938452B1 ( en ) | 2019-06-12 | Reciprocating tool with internal guiding bushing and method of operating such a tool |
US5870829A ( en ) | 1999-02-16 | Portable powered hack-saw |
JP2003501290A ( en ) | 2003-01-14 | Hand held thread saw machine |
CA1111321A ( en ) | 1981-10-27 | Pneumatic hack saw |
Legal Events
Owner name: PORTER. CABLE CORPORATION, TENNESSEE
Free format text: ASSIGNMENT OF ASSIGNORS INTEREST;ASSIGNORS:SCHNELL, JOHN W.;BOSTEN, DONALD R.;WALL, DANIEL P.;AND OTHERS;REEL/FRAME:009465/0254;SIGNING DATES FROM 19980824 TO 19980827
Free format text: PATENTED CASE
Owner name: BLACK DECKER INC., DELAWARE
Free format text: ASSIGNMENT OF ASSIGNORS INTEREST;ASSIGNOR:PORTER-CABLE CORPORATION;REEL/FRAME:017006/0374
Effective date: 20041002
How To Change Jigsaw Blade Quick – T-Shank And U-Shank
Changing a jigsaw blade is really simple for most jigsaw models, and you can do it in about 5 seconds. But some older jigsaw models do have some complicated ways to change a blade without it being too obvious how to do it. For modern jigsaws, you can just do the following to change the blade.
Jigsaws that use a T-shank blade usually have a lever just above the jigsaw blade. To change the blade we simply pull this lever, which will turn the blade slot 45 degrees. Now you can remove the blade from the slot. Hold the lever in the 45-degree position and insert the new blade all the way in and release the lever.
The example above will be the case for most of you reading this article, but for some jigsaws, it is different. For some older Bosch models, there is even a 4″ deep skinny hole you have to insert your screwdriver into to change the blade.
Let’s go through all the methods of changing a jigsaw blade. In an order starting with the obvious, then the not-so-obvious, and at last the absolutely ridiculous methods.
But first, we have to find out what type of blade your jigsaw can use.
T-Shank Or U-Shank
Jigsaw either uses a T-Shank blade or a U-shank Blade. The T-shank is the industry standard now. Generally, jigsaws that use T-shank blades can not use U-Shank blades and jigsaws that use U-shank blades can not use T-shank blades.
A U-shank jigsaw will sometimes be able to secure a T-shank blade in the holder and vice versa. And you will be able to cut with it. But it isn’t optimal and the cuts are going to be worse than if the right blade was used.
T-shank blades have a tighter fit than U-shank blades, they vibrate less, and are often easier to change.
T-shank blades have a shank shape similar to a T.
U-Shank Blades have a shank shape similar to a T.
To determine if your jigsaw uses a T-shank or U-shank blade you can look at the blade that is in your jigsaw right now, check the default blade that came with the jigsaw, or look in the manual for the jigsaw.
How To Change A T-Shank Blade On A Modern Jigsaw
Now, by a modern jigsaw, I mean any jigsaw made in the 21 century. On these jigsaws, it will be simple to change the blade. They have a quick-release system that does most of the job for you.
Locate The Lever
The lever might be in different places depending on the jigsaw. On my Makita jigsaw, it is right above the blade holder.
On some jigsaws, the lever is placed on the right or the left side of the jigsaw.
On others, the blade holder itself is the lever you have to turn. And is a little bit harder to access, but the concept is the same.
Some jigsaws can use a quick-release system where you have to pull the blade holder towards you when you want to change the blade. You have to do the same when you want to insert the new blade.
Pull The Lever
To release the blade we need to pull the lever or twist it about 45 degrees. This will turn the blade holder and the blade will come loose.
Remove Jigsaw Blade
Keep the lever at 45 degrees and pull out your jigsaw blade. It should come out without using any force.
Some jigsaw blade changing systems are spring-loaded. If so, the jigsaw blade will jump out on its own when you turn the lever.
I do not really like these spring-loaded systems. Sometimes the spring has too much tension, and the blade will come shooting out and land somewhere in the room.
Insert Jigsaw Blade
While still holding the lever at about 45 degrees, insert the jigsaw blade with the teeth facing away from the jigsaw.
Put it in as far as it can go without using force and slowly release the lever.
Now the blade should settle in tight and is automatically straightened.
Line Up Roller And Blade
It is important that Jigsaw sits up against the roller guide, and that it is in the center of it.
I usually turn the jigsaw upside down to check that blade is securely placed and looks straight.
With the power turned off, you can also pull the jigsaw blade a couple of times to make sure that it is tight and does not come loose.
Common Problems
A common problem with jigsaws is that the blade keeps fallout out while cutting. Some jigsaw models have a poor design that can cause this to happen.
The set screw can also become loose due to the vibration that is created when cutting with a jigsaw. But the set screw problem is more relevant to the upcoming way to change a jigsaw blade.
Jigsaw blades can become crooked after use, this usually happens if you use too much force during the cut, you have a dull blade or you hit something hard like a nail during the cut.
When you have a crooked jigsaw blade you should change the blade, or you can try to straighten it with a vice.
How to change T-Shank/U- Shank Jigsaw Blade With Set Screw
The method of changing T-shank and U-shank blades that are secured with a set screw is very similar. So I’m going to join them together.
Locate The Set Screw
The set screw will either be at the front of the blade holder or on the side of the blade holder. It can either be a flat head screw or an alan head screw.
Some jigsaws use one screw and some jigsaws use two screws.
On some jigsaw models, the set screws are placed behind the blade guard. But there are slots that you can fit the alan key through.
It can also be completely exposed so it is easy to get access.
Loosen The Set Screw
When you have located the set screw, you need to determine what tool you need to use.
But basically, you need a normal flathead screwdriver or a set of alan wrenches.
The tool to change the blade is usually included when you buy the jigsaw.
Just loosen the set screw enough to take out the blade, don’t remove it entirely. It can be a pain to get back in the hole, especially for jigsaws with a blade guard.
Insert The New Blade
Insert the blade in the blade holder with the teeth facing away from the jigsaw. Push it as far in as it goes without using force, it should slide in without effort.
On T-shank blades that use a set screw, the T part of the shank is supposed to be placed right up to the blade holder. So the two shoulders of the blade are on the outside of the blade holder.
On U-shank blades that use a set screw, you will just push it in as far as it goes.
Tighten The Set Screw
Be sure to hold your jigsaw in a way so that the blade does not move while you are tightening the screw.
My tip is to hold it upside down at a slight angle.
Check That It Is Straight
After you have finished tightening there is one more thing we have to do before we start cutting.
Make sure the blade is straight, and that it rests on the blade guide that supports the blade.
While the unit is unplugged, try to pull the blade to check if it is secured tightly.
The set screws can become loose after you have used the same blade for a while due to the high vibrations that a jigsaw produces while cutting.
Be sure to tighten the set screws once in a while.
How To Change Jigsaw Blade With No Lever Or Set Screw Visible
For this last blade change, I am not going to complete a full guide, because it is basically the same method as the one above. But the set screw is hidden.
On some jigsaw models, they have managed to hide the set screw deep down in the tool, in a hole on the top of the tool. I have no idea why they thought this was a good idea, but it is what it is.
An example of a model that uses this type of blade-changing system is the Bosch 1581vs jigsaw. Some other older Bosch model also uses this method too. There might be other brands that use this method as well, but I don’t know about them.
Luckily, they have moved away from this method.
The method of changing the blade is the same as with other jigsaws that use a set screw for tightening.
Use a long flathead screwdriver that can into the long hole on the top of the tool, loosen the set screw, remove the blade, insert the new blade and tighten the set screw.
Recent Posts
What is a Jigsaw? A jigsaw is a handheld power saw that can cut a wide range of different materials by cutting in a reciprocation motion. A jigsaw is one of the most versatile power saws and it.
Dremel Plunge Router 335-01 A Dremel is not the best tool to make straight cuts in wood, but in a pinch, you can achieve decently straight cuts with a Dremel. This will take some effort.
About Us
Here At Mainly Woodwork, we strive to make woodworking simple, cheap, and accessible to everyone!
LEGAL INFORMATION
This site is a participant in the Amazon Services LLC Associates Program, an affiliate advertising program designed to provide a means for sites to earn advertising fees by advertising and linking to Amazon.com. We are compensated for referring traffic and business to Amazon and other companies linked to on this site. report this ad
Jigsaw blade holder
Choose additional country / region / language Milwaukee Tool websites
Choisissez des sites Web supplémentaires de pays / région / langue pour Milwaukee Tool
Elija sitios web adicionales de Milwaukee Tool por país / región / idioma
Get Connected. Receive FREE Decal!
Claim your free Milwaukee decal by joining HEAVY DUTY NEWS the trusted source of new Milwaukee solutions, events, contests and more.
We experienced a technical difficulty while processing your request. Your request may not have been correctly sent.
By signing up, you agree to receive emails from Milwaukee with news and other information. To unsubscribe at any time, go to Privacy Policy. For more information regarding free Milwaukee decal giveaway, please visit Terms Conditions. While supplies last. Please allow 4-5 weeks for delivery.
T-Shank Blade Holder for Leatherman FREE P4
This mod involves extra steps by the user, please read the information tabs below.
You can also install this on the Leatherman FREE P2, if your willing to replace the main blade, or the scissors, and some of the thin implements.
Not compatible with the FREE K or T series.
#ScissorsOrSerratedBlade
If installing the T-Shank on the same side as the two thick implements: Then you need to trade one of the thick implements with a thin one from the other side.
Features:
This is a user-installed modification. It is a more involved than my bit-holders, so please read the various tabs below.
- Holds T-Shank Jig-Saw blades
- Holds blades ranging from 1 to 2 mm thick
- 1 mm blades may require use of a shim (See video)
- Sorry the screws cannot be included
- Shapeways only makes and ships the 3D printed parts.
- Select “Silvered Bronze” for the closest fit to the tool
- Select “Bronze” for a fully bronze color
- Select “Blackened Bronze” for a contrasting dark bronze look
- See this page for an image of all three side by side
The default “Saw or Main Blade” variant can replace the Saw or Main Blade on the FREE P4. This is the version seen in the video. It can also be installed in place of the Main Blade on a FREE P2.
The alternate “Serrated or Scissors” variant is a mirrored design. It can replace the Serrated Blade or Scissors on a FREE P4, or the Scissors on a FREE P2.
The T-Shank holder is designed to replace the saw and one thin implement. You cannot install it on the same side as my Bit Driver mods due to the total thickness.
Taking the tool apart is a non-destructive process, however any warranty concerns are entirely up to the user.
Alternate configurations are up to the end user. Other adjustments to the tool order/washers may be needed to keep the correct stack-up height. The T-Shank holder takes up 0.18″ of the tool stack height.
Refer to the images below to reference the stack-up of the FREE P4 or P2.
T-Shank Blades:
This has been designed and tested to fit Bosch brand blades as well as the Leatherman T-shank blades.
If you want to store a blade in the tool, it needs to be cut to a total length of 78 mm /- 1 mm. Note: If the blade is cut too short it can pop-out when the pliers are deployed.
Screws and tap tool:
The parts requires some light metal work including tapping threads into the holes.
Shapeways only produces and ships the 3D printed parts, so the screws and tools cannot be included with your order. Please keep this in mind before ordering.
The cost of these parts from McMaster is ~30shipping, or about half that price from eBay
The mod requires two small screws with the following specs:
You also will need a M2 x 0.4 mm tap to finish the two holes. The tap must be able to handle stainless steel. I recommend using this tap from Amazon, or McMaster P/N: 8305A77 I also recommend using cutting fluid or oil to prevent the tap from binding.
If the tap doesn’t bite, you can ream out the hole using a 1/16″ (1.6mm) drill bit.
To drive the set screws you need a 1.5mm hex bit, or Allen key. I recommend getting a few of McMaster P/N: 7289A11, and then cutting one down to fit in the tool, and leaving a second with your spare T-Shank blades.
Also, the Leatherman Flat Bit Kit does include a 1.5mm Hex bit. This can be stored in the tool in my Flat bit holder, or on one of my holsters.
Post Processing:
The parts are made by a bonding stainless steel powder. The resulting part is sintered and impregnated with bronze to fully meld the two metals together. Because a powder is used: Some internal areas of the part may end up with stuck powder that needs to be cleared away using drill bits or files. If your part has an excessive amount of stuck powder, or filled holes, contact Shapeways customer service with a photo of your part for a replacement, along with your order number.
The part is similar to a casting, and shrinks a small amount during processing. The CAD model has been designed to compensate for this, but some manual filing may be needed on some parts if the parts fit too tight or bind. Use a needle file to clean up any burrs or places that are sticking. The material is stainless steel, so diamond needle files may be required.
The mounting hole may require reaming using a drill bit capable of handling stainless steel. A 1/8″ or 3.2mm drill bit may be used for this task.
Installation:
The tool must be taken apart to install this modification. See the video above.
- You will need two Torx T9 bits to remove the screws holding the tool together.
- The screws need to be loosened by holding one side with a bit, and turning the other side.
- The screws are secured using thread-locking compound, and heat may be required to loosen the compound.
- Care should be taken to open the tool on a clean surface.
- To install you need to remove the following items from the Leatherman FREE P4
- Saw blade
- Can opener (Or any of the other four small implements)
- The Thin spacer washers. Keep one washer in the stack if your removed the File or Ruler.
- One Thick spacer washer (Near scale on saw side)
- After removing those components, stack the three remaining small implements up against the serrated blade.
- Place the spring arm next to the implements.
- Install the two halves into the remaining space.
- Silicone based lubricant may be added during assembly.
- Re-install the post and screws. The tightness of the tool will depend on the amount of torque you apply during reassembly.
Design:
The result of six physical prototypes, combined with input from the folks at Multitool.org. Click the link to see how these was designed and the early prototypes.
How Shapeways fulfillment Works:
Many items on this website are manufactured by Shapeways.com
The parts are professionally 3D printed, and then drop shipped to your address.
I cannot customize, alter or process any returns after your order has been placed. All sales are final.
ZapWizard is the part designer. I receive a fixed portion of the total order.
Upon order you will receive a confirmation of the order, and a notification upon shipment. If you need more details on the state of an item please send me a message with the order number, or place your order directly on my Shapeways.com store.
All items in the US are shipped using UPS Mail Innovations. This means your shipment will be transferred your local carrier for final delivery. If you require faster shipping or international shipping: Please order directly from the Shapeways.com marketplace.
Shipping costs and any other related fees related to Shapeways are controlled by Shapeways.com. For more information please see the Shapeways.com page on shipping time and costs.
Shapeways.com provides a 10-day warranty for manufacturing defects. Please contact me as soon as possible if you have any defects such as a warped metal part, or heavily filled area. Please include your order number and a photo of the defective part.
Printed by binding stainless steel powder into the shape of the object. The part is then placed in a 1100°C over and infused with bronze. The part is then sintered into a solid metal part.
The part is then polished. Some burrs may escape polishing, especially on internal areas. Holes may require reaming with a drill bit.
If your part has an excessive amount of stuck powder, or filled holes, please contact Shapeways customer service with a photo of your part for a replacement.
The bronze steel amalgam comes in three finishes:
- Silver Bronze
- It can vary a bit from part to part. Sometimes is it a lighter silvery color, sometimes a slightly brass looking color
- The finish does remain and won’t wear off
- This is a more solid looking brown/bronze finish
- The finish does remain and won’t wear off
- This is a matte black surface finish
- It will rub off in wear areas leaving a patina like finish over time
T-Shank Blade Holder for Leatherman FREE P4
This mod involves extra steps by the user, please read the information tabs below.
You can also install this on the Leatherman FREE P2, if your willing to replace the main blade, or the scissors, and some of the thin implements.
Not compatible with the FREE K or T series.
#ScissorsOrSerratedBlade
If installing the T-Shank on the same side as the two thick implements: Then you need to trade one of the thick implements with a thin one from the other side.
Features:
This is a user-installed modification. It is a more involved than my bit-holders, so please read the various tabs below.
- Holds T-Shank Jig-Saw blades
- Holds blades ranging from 1 to 2 mm thick
- 1 mm blades may require use of a shim (See video)
- Sorry the screws cannot be included
- Shapeways only makes and ships the 3D printed parts.
- Select “Silvered Bronze” for the closest fit to the tool
- Select “Bronze” for a fully bronze color
- Select “Blackened Bronze” for a contrasting dark bronze look
- See this page for an image of all three side by side
The default “Saw or Main Blade” variant can replace the Saw or Main Blade on the FREE P4. This is the version seen in the video. It can also be installed in place of the Main Blade on a FREE P2.
The alternate “Serrated or Scissors” variant is a mirrored design. It can replace the Serrated Blade or Scissors on a FREE P4, or the Scissors on a FREE P2.
The T-Shank holder is designed to replace the saw and one thin implement. You cannot install it on the same side as my Bit Driver mods due to the total thickness.
Taking the tool apart is a non-destructive process, however any warranty concerns are entirely up to the user.
Alternate configurations are up to the end user. Other adjustments to the tool order/washers may be needed to keep the correct stack-up height. The T-Shank holder takes up 0.18″ of the tool stack height.
Refer to the images below to reference the stack-up of the FREE P4 or P2.
T-Shank Blades:
This has been designed and tested to fit Bosch brand blades as well as the Leatherman T-shank blades.
If you want to store a blade in the tool, it needs to be cut to a total length of 78 mm /- 1 mm. Note: If the blade is cut too short it can pop-out when the pliers are deployed.
Screws and tap tool:
The parts requires some light metal work including tapping threads into the holes.
Shapeways only produces and ships the 3D printed parts, so the screws and tools cannot be included with your order. Please keep this in mind before ordering.
The cost of these parts from McMaster is ~30shipping, or about half that price from eBay
The mod requires two small screws with the following specs:
You also will need a M2 x 0.4 mm tap to finish the two holes. The tap must be able to handle stainless steel. I recommend using this tap from Amazon, or McMaster P/N: 8305A77 I also recommend using cutting fluid or oil to prevent the tap from binding.
If the tap doesn’t bite, you can ream out the hole using a 1/16″ (1.6mm) drill bit.
To drive the set screws you need a 1.5mm hex bit, or Allen key. I recommend getting a few of McMaster P/N: 7289A11, and then cutting one down to fit in the tool, and leaving a second with your spare T-Shank blades.
Also, the Leatherman Flat Bit Kit does include a 1.5mm Hex bit. This can be stored in the tool in my Flat bit holder, or on one of my holsters.
Post Processing:
The parts are made by a bonding stainless steel powder. The resulting part is sintered and impregnated with bronze to fully meld the two metals together. Because a powder is used: Some internal areas of the part may end up with stuck powder that needs to be cleared away using drill bits or files. If your part has an excessive amount of stuck powder, or filled holes, contact Shapeways customer service with a photo of your part for a replacement, along with your order number.
The part is similar to a casting, and shrinks a small amount during processing. The CAD model has been designed to compensate for this, but some manual filing may be needed on some parts if the parts fit too tight or bind. Use a needle file to clean up any burrs or places that are sticking. The material is stainless steel, so diamond needle files may be required.
The mounting hole may require reaming using a drill bit capable of handling stainless steel. A 1/8″ or 3.2mm drill bit may be used for this task.
Installation:
The tool must be taken apart to install this modification. See the video above.
- You will need two Torx T9 bits to remove the screws holding the tool together.
- The screws need to be loosened by holding one side with a bit, and turning the other side.
- The screws are secured using thread-locking compound, and heat may be required to loosen the compound.
- Care should be taken to open the tool on a clean surface.
- To install you need to remove the following items from the Leatherman FREE P4
- Saw blade
- Can opener (Or any of the other four small implements)
- The Thin spacer washers. Keep one washer in the stack if your removed the File or Ruler.
- One Thick spacer washer (Near scale on saw side)
- After removing those components, stack the three remaining small implements up against the serrated blade.
- Place the spring arm next to the implements.
- Install the two halves into the remaining space.
- Silicone based lubricant may be added during assembly.
- Re-install the post and screws. The tightness of the tool will depend on the amount of torque you apply during reassembly.
Design:
The result of six physical prototypes, combined with input from the folks at Multitool.org. Click the link to see how these was designed and the early prototypes.
How Shapeways fulfillment Works:
Many items on this website are manufactured by Shapeways.com
The parts are professionally 3D printed, and then drop shipped to your address.
I cannot customize, alter or process any returns after your order has been placed. All sales are final.
ZapWizard is the part designer. I receive a fixed portion of the total order.
Upon order you will receive a confirmation of the order, and a notification upon shipment. If you need more details on the state of an item please send me a message with the order number, or place your order directly on my Shapeways.com store.
All items in the US are shipped using UPS Mail Innovations. This means your shipment will be transferred your local carrier for final delivery. If you require faster shipping or international shipping: Please order directly from the Shapeways.com marketplace.
Shipping costs and any other related fees related to Shapeways are controlled by Shapeways.com. For more information please see the Shapeways.com page on shipping time and costs.
Shapeways.com provides a 10-day warranty for manufacturing defects. Please contact me as soon as possible if you have any defects such as a warped metal part, or heavily filled area. Please include your order number and a photo of the defective part.
Printed by binding stainless steel powder into the shape of the object. The part is then placed in a 1100°C over and infused with bronze. The part is then sintered into a solid metal part.
The part is then polished. Some burrs may escape polishing, especially on internal areas. Holes may require reaming with a drill bit.
If your part has an excessive amount of stuck powder, or filled holes, please contact Shapeways customer service with a photo of your part for a replacement.
The bronze steel amalgam comes in three finishes:
- Silver Bronze
- It can vary a bit from part to part. Sometimes is it a lighter silvery color, sometimes a slightly brass looking color
- The finish does remain and won’t wear off
- This is a more solid looking brown/bronze finish
- The finish does remain and won’t wear off
- This is a matte black surface finish
- It will rub off in wear areas leaving a patina like finish over time