Rotary mower blade removal. How to remove the blades of a Briggs and Stratton…
How to remove the blades of a Briggs and Stratton lawnmower, step by step
Briggs and Stratton Lawnmowers are lovely and helpful machines that do all your mowing efficiently. Like all devices, they need maintenance, especially the lawnmower’s blades that get worn out over time. A sharp blade can cut twice as fast as compared to a dull one. Briggs and Stratton lawnmower blades are firmly fixed with nut bolts that can be loosened to remove them. In day-to-day mowing, you will need to check your blade regularly. If you find them to be dull, remove the blade and sharpen or replace it. When removing a Briggs lawnmower blade, you should take the necessary precautions and correctly follow the removal steps.
How to remove the blades of a Briggs and Stratton lawnmower, step by step:
- Step 1. Check the operator’s manual
- Step 2. Remove the spark plug and disengage the ignition wire
- Step 3. Remove the fuel from the chamber
- Step 4. Tip the mower and use a cleaner spray
- Step 5. Remove the bolts retaining blade
This blog post provides an easy to follow step by step approach to remove your Briggs and Stratton lawnmower’s blade. We will show you the necessary precautionary measures and ways to deal with potential issues.
Steps To Follow:
Step 1: Operator’s Manual
Different companies produce various lawnmowers, but they all have a blade and will cut your grass. But the exact way the blade is attached will differ. Even between Briggs and Stratton models, this can be different. Also important is the blade’s orientation, the tightening screw, and overall construction. It is always advisable to check your Briggs and Stratton operator’s manual for your specific model’s.
Step 2: Spark plug and Ignition wire
The first step when dealing with a gas mower is a safety precaution. To make sure that the engine can’t start unintentionally, disengage the ignition wire. If you are using a Briggs and Stratton cordless model, make sure that you remove the batteries. If you use a Briggs and Stratton electric lawnmower make sure to remove the wall plus. Also turn the ignition off, if that is possible with your model.
If you have a gas model, you could consider removing the spark plug. Removing it and disengaging the ignition wire are safety measures to ensure that the mower may not turn on accidentally. Dealing with a super sharp object like the blade of a mower can cause some serious injury. Additionally, for models that do not have a nutrual gear, removing the spark plugs makes turning the blade much more comfortable than when the spark plugs are still present.
Depending on your lawnmower model, the spark plug may be positioned on the side of the chamber next to the pull cord. In the case of riding a lawnmower, you may even have to remove the seat to see it.
Step 3: Empty the fuel chamber
The next step is to remove the fuel present in the combustion. Do this to avoid any fuel spilling when you tip the mower aside. This can be done quickly using a siphon pump. The siphon pump sucks the fuel from the chamber through a tube. It is a quick, easy, and fast process. You can store the extracted gas in a suitable container and add it to the gas tank later. If you want to keep gas for a more extended period, it is good to use an airtight container. A suitable container will be marked with “UL.” This symbol shows that the container is made for a specific reason and will not ignite the fuel.
Step 4: Tip the mower and prepare it
While working on your lawnmower it can take some time, so make sure that you place it conveniently to avoid any stress on your back and ensure proper light to the machine. After you remove the spark plug and fuel, tip the mower to its side. If you have a larger and heavy model, you can use a jack for this. There are also special tools to help with this. An alternative is to lift your lawnmower up, so you can reach the underside. Always make sure that the lawnmower is correctly balanced and stable, and that it can not suddenly move when you are working on it.
The mower’s base will now expose its blade, and you can see the blade retainer bolt in the centre of the blade. Before removing it, use some cleaner spray like WD-40. This will help remove the rust, soften the tightness, and ease the unscrewing. And it helps increase the life of the bolt and its threads.
Step 5: Remove the blade
When you have tipped your Briggs mower, you can easily see the blade and its fixing mechanism. Make sure that you have your safety gloves on. Then, ensure that while you remove the central bolt, the blade doesn’t rotate. Use a universal blade removal tool or a piece of wood to fix the blade at one position. The blade won’t be able to move. This will help in terms of safety and ease of removal of the bolt.
The blade tightening bolt can be easily removed using a torque wrench or some pliers. The torque wrench is a better tool. It is fast as it clicks in one direction. So, please keep it in anti-clockwise orientation and give regular rotations to remove the blade thoroughly.
Following these steps in the correct order, and one can easily remove the mower blades. Keep in mind that when you reattach the blades, you will repeat the same steps backwards by connecting the spark plug at the end. Depending on how often you use your lawnmower, and how big your lawn is, you should check, sharpen and if needed, replace the mower blades at least once per season.
Some Precautionary Measures
A blade is a cutting tool. When working on them, take the following points as a precaution:
- Location: Try to work in a safe location with a hard floor. So when you spill oil or fuel, you can clean it easily without damaging the environment.
- Gloves: Use safety gloves throughout the procedure.
- Fuel: Remove the fuel and spark plug.
- Clean workspace: Work in a clean workplace away from any water source.
- Cleaning spray: Use a cleaning spray to loosen and moisten the bolts.
Frequently asked questions
1.How can we get a broken bolt out of a lawnmower blade?
A broken bolt in a lawnmower blade may cause an issue. But with a little bit of effort, it can be taken out. First, use WD-40 or other lubricant to help with this process. If you can still see part of the bolt, you can try to remove it with a vise grip. Giving it some punches with a hammer may loosen it as well. If there is no part of the bolt sticking out you can use a special kit to remove the broken bolt. With a special drill, you make the top of the broken bolt such that you can use the added removal tool to it and get it out. If that also does not work, you have to drill it out. But this probably means that you need to add new threads and have to use a bigger bolt. If you do not feel comfortable with the above methods, it is good to find a good mechanic that can help you.
2.How to create a pilot hole?
A left-handed drill can be used to create a pilot hole. A pilot hole is essential as it helps to avoid damaging threads of the bolt because if the thread of bolt holes or bolt gets damage, it may either result in the removal of bolt impossible or one may not be able to put new bolt after changing the old one. To remove the broken bolt, reverse drill slowly. A magnet can easily attract out the left metal pieces of the broken bolt. One must remove the left behind pieces of the bolt also. Otherwise, it can cause a problem whenever it’s time for a new bolt to fix in its place. Even after trying these instructions, if you face issues, go for a welding shop that ought to have better tools to get the snapped bolt off the hole.
3.What direction should we move the nut to change the mower blade?
Many walk-behind lawnmowers rotate in the clockwise direction, and we must turn the blade’s retaining bolt to a counter-clockwise direction. Make sure to check the lawn mower’s fit, too, pay attention to how the blade fits into the blade adapter, and then tighten the blade retaining bolt by moving it in the clockwise direction to a torque of specified mower manual.
Final Remarks
To conclude, removing a blade from your lawnmower is not a difficult task. It sounds easy, but a lot of users forget specific steps. Maintaining your lawnmower well means that you can use it for many years to come. A lawn mower’s blade must be checked regularly during the season. And if needed, it must be sharpened or replaced. Sharpening should be done at least once per mowing season to ensure it keeps cutting well.
How To Remove Your Lawn Mower Blade? (2023 Guide)
Sometimes your lawn mower blade just needs to be replaced. Sharpening can keep you going for a little while, but the metal itself will eventually wear out and get too thin from repeated sharpening.
When it’s time to replace your blade, you need to know how to remove your current lawn mower blade first.
The process is relatively simple and can be done at home with a minimum of tools. Some professionals might offer a blade change service for a fee, but this is so easy I don’t think it’s worth paying for unless you have a large riding lawn mower.
I’ll cover riding lawn mowers too, just in case you have the equipment needed to make that change.
In this guide you’ll learn:
- How to tell when your lawn mower’s blade needs to be replaced
- How to replace 3 kinds of lawn mower blades
- And much more!
What Are the Reasons You Need To Remove Your Lawn Mower Blade?
Lawn mower blades tend to be pretty durable and long lasting tools, especially when you know how to sharpen them. But, they do eventually wear out and need replacement. A poorly mowed lawn is only the least of your problems when you have a lawn mower blade that needs to be replaced.
That doesn’t mean that a bad mowing job isn’t a big problem, though. Uneven, ragged, mowing can seriously stress your lawn and made it difficult to keep your grass healthy.
Removing your lawn mower blade is the first step to replace it, so it’s an important skill to have.
Of course, replacing your lawn mower’s blade isn’t the only time you might need to remove the blade. For instance, if you have blades for different uses, you might need to switch between them in the middle of the season. Or, your blade might need some maintenance like a sharpening session or a thorough cleaning.
Some people will remove lawn mower blades to help winterize their mowers. I don’t think that’s particularly necessary unless you live somewhere with high humidity and rust risk in the winter. But, it can sometimes make storage easier or give you an opportunity to do some maintenance on the blade during the off season.
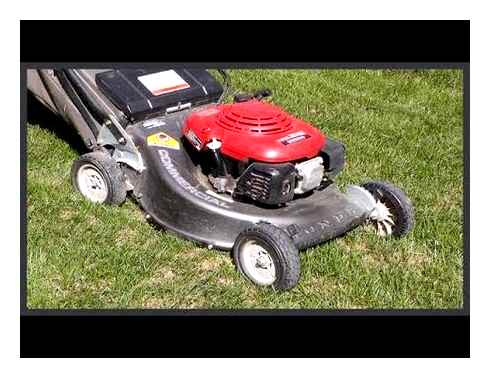
How To Tell When It’s Time To Replace Your Lawn Mower Blade?
Knowing that you might need to replace your lawn mower’s blade won’t do you any good if you can’t tell when it’s time for a replacement. Here are a few signs to look for that it’s time to replace your blade:
Your Lawn Mower Blade has Bent or Twisted
Despite being relatively simple tools, lawn mower blades are still optimized to provide good cutting power. Any sign that your blade has started bending or twisting means, at a minimum, that your blade isn’t performing the way it should any longer.
At worst, your blade could be starting to damage your lawn mower itself, or may start damaging your lawn mower soon.
As soon as you notice signs of bending or twisting in your lawn mower’s blade, it’s time for a new one.
Nicks and Gouges Make It Difficult to Sharpen
Re-sharpening your lawn mower’s blade can extend the life quite a bit, but sometimes the surface scratches on your blade are too deep to work around. Scratches are a normal part of any used lawn mower blade. Grass, gravel, rocks, and even small clumps of dirt can all cause scratches over time.
Usually small surface scratches are no problem. You can buff them out while sharpening, and many scratches won’t be anywhere that affects the function of the blade.
However, if you’re starting to get deeper scratches and gouges, more than about 2-3mm deep, it may be time to consider replacement. That’s because deeper scratches and gouges can cause weak points in the blade. The last thing you want is your lawn mower blade cracking while you’re using it.
In a worse case scenario a deep gash could crack and eventually break free entirely. If you’re lucky, a broken blade will damage your lawn mower. If you’re not lucky the blade could fly free of the mower and cause damage to you, or the people, plants, and buildings around you.
It Isn’t Holding An Edge
This is less common, but some blades will lose their ability to hold an edge over time. Usually this happens with blades where only the original cutting edge was fully hardened, and problems with hardening can happen with any manufacturer and model.
Over time these blades just won’t take or hold an effective cutting edge, losing their ability to cut grass at the same time. If you’re having to sharpen your lawn mower’s blade more and more often it’s probably time to remove the blade and replace it.
It’s Not Performing Well
The last reason is both the most common, and the simplest. You might need to remove and replace your blade simply because it doesn’t seem to be working as well anymore. Sharpening may be an option at this phase, but it depends on the blade and owner. Lawn mower blades are usually pretty affordable, so I know plenty of people who don’t bother sharpening their blades when they’ve started to go dull.
If you’re getting uneven clumps of grass after mowing, chances are you either need to sharpen your blade, or replace it.
How To Remove Your Push Lawn Mower Blade
To start with, let’s talk about one of the most common kinds of lawn mower—the motorized push behind lawn mower. Chances are, if you have a suburban-sized lawn, this is the kind of lawn mower you use.
Step 1: Get Your Lawn Mower Ready
The first step to remove your lawn mower’s blade is to get it ready to be tilted or flipped over. For gas-powered lawn mowers that means you should drain the gas tank (if possible) and remove the spark plug.
Remove the battery from battery powered lawn mowers.
Unplug electric corded lawn mowers.
This prep helps prevent accidents and can also help your lawn mower last longer in the case of gas-powered mowers.
Once the power source is safe, either tilt your lawn mower up so you can access the blade, or consider flipping it entirely on it’s back. I like to place a tarp under the lawn mower to help prevent scratches on the outer casing.
Step 2: Remove Fasteners
Your lawn mower’s blade should be held on by 1 to 3 bolts in the center of the blade. It’s unlikely that you’ll be able to loosen these bolts with your hands, so you’ll need a wrench, or in some cases a screwdriver, to get them free.
Try to only use tools the right size and shape from the bolt to prevent stripping them or changing the shape. Most lawn mower blade fasteners can be replaced, but some are a non-standard size or length and can be hard to find.
Once the fasters are loose, put them in a small bag or a to keep them safe.
Step 3: Lift the Blade Off
With the fasteners gone your blade should lift free of the lawn mower. I recommend having a can of WD-40, or a rag and some water, in case the blade is stuck in place. Gently work the blade free until it’s completely loose.
Remember, don’t use too much force at this phase or you’ll risk breaking either the blade or it’s attachment points.
How To Remove Your Riding Lawn Mower Blade
Step 1: Park Your Riding Lawn Mower
First you’ll need to drive your riding lawn mower into a garage, barn, or other sheltered area and park it. You don’t want anything to move while you’re working, so go ahead and use the brake systems and other lock settings to keep the lawn mower as immobile as possible.
Step 2: Lift The Lawn Mower So You Have Work Space
The next step is getting the lawn mower lifted enough that you can get your tools underneath and have room to work. Some people drive up a ramp onto a special maintenance frame to get access, while others lift the lawn mower onto wooden blocks.
I personally recommend using a riding lawn mower and tractor lift since it’s the safest and most secure option. However, those lifts can be relatively expensive equipment so not everyone uses them.
Whatever method you choose, check to make sure the lawn mower is secure and unlikely to fall. Think about this the same way you would think about lifting a car and working under it, the risks are very similar.
Step 3: Match The Bolt To The Appropriate Wrench
The larger, tighter bolts of a riding lawn mower’s blade generally need a wrench to remove. I recommend checking to make sure you have the right size, or setting the width of an adjustable wrench, before you start to get to work.
The wrench is a good fit if it’s wide enough to reach all the way around the bolt without any wiggle room. The more space between the sides of the bolt and the wrench, the more likely you’ll accidentally curve the corners of the bolt when you remove it.
Step 4: Remove the Fastener
Most riding lawn mower blades only have a single attachment bolt, but some do have more than one. Use the wrench to remove each bolt, until the blade is free.
I don’t recommend using a breaking bar unless absolutely necessary in this process. A small amount of WD-40 should be enough to loosen particularly stubborn bolts. Alternatively you can use a rubber mallet on the end of the wrench to provide some more force without risking damaging the bolts.
Step 2: Remove the Blade
Slowly and gently remove the blade if it didn’t come free on it’s own after you’ve removed the fasteners. Once the blade is free I recommend taking a moment to clean the area and remove any rust or corrosion that could make reattaching or removing the blade more difficult in the future.
How To Remove Your Reel Lawn Mower Blade
Reel lawn mowers are a little different, if you need to replace or repair the blades you’re not going to remove them from the lawn mower. Instead, your best option is to remove the other components of your reel mower and then replace them after sharpening or repairing the blade.
In some cases, you might replace the whole reel blade and then reattach the other components to the new blade.
Step 1: Remove the Drive Wheels
First, lay your reel mower on a flat space where it’s relatively stable. Your drive wheels are on either side of the blade, usually covered by a plastic hub cap. You can use a screwdriver to remove the hub caps without damaging them. Set the hub caps aside.
There is a clip holding both wheels to the axel. Use the same screwdriver to pull the clip loose. Set aside.
Next is a pinion gear. This can be removed by turning it counterclockwise until it comes free. You should be able to turn the gear with your hands.
There’s one more clip you’ll need to remove, also on the axel. Pull this away from the assembly plate. While you can dissasemble the assembly plate as well, it isn’t necessary and can cause irreparable damage to your lawn mower, so I don’t recommend it. Instead you’ll work around it to get this pin free.
Once the last pin is out you should be able to remove the blade from that side. Repeat on the other drive wheel.
Step 2: Remove the Rear Wheels
Most lawn reel mowers have a set of rear wheels for added stability. Some will also have a set of front wheels, but the removal process is the same for both.
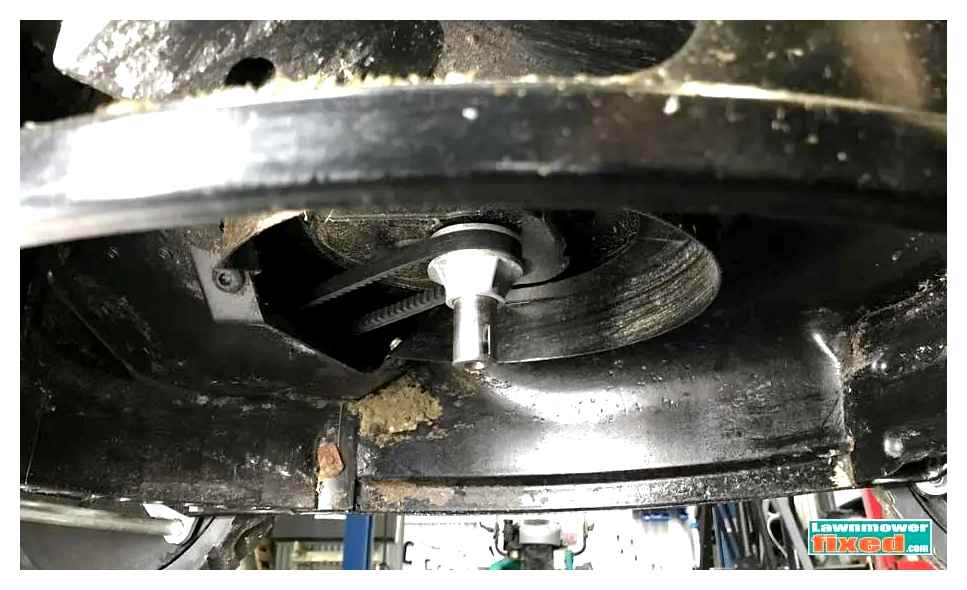
All you need to do here is unbolt the wheels from the main assembly with a wrench. Try to make sure the wrench fits securely before you start to help avoid damaging the bolts.
Step 3: Remove the Mower Handle
Most reel mower handles are held on with a small pin near the bottom of the handle. Use a screwdriver to help remove the pin, and push the lawn mower handle toward the bottom to help remove some pressure from the pin.
Once the pin is free, the handle should be easy to remove. If it sticks, clean off the bottom of the handle and grease it with some mineral oil or WD-40 to help prevent further corrosion and make future maintenance easier.
Once the handle is removed you should be left with the blade and the assembly plate. Removing the blade is simple at this point, or you can sharpen the blade still attached to the assembly plate.
My Final Thoughts On Removing Your Lawn Mower Blade
Removing your lawn mower blade might not be fun or exciting, but it is an important skill to have. This guide should cover just about any standard lawn mower in the United States, but it’s also a good idea to check your users manual if you have it.
Remember that not all maintenance means you have to remove the blade. You can even sharpen some blades without taking them off of the lawn mower. I’ve written a guide to sharpening blades without removing them, but it does work best for blades with a simpler design.
As always, if you’re concerned that you can’t safely perform maintenance on your lawn mower yourself you should take it to a professional instead. No amount of savings is worth taking unnecessary risks to maintain your lawn mower.
With that in mind, happy mowing, and may your lawn mower never need more than basic maintenance!
Lawn Mower Blade Bolt Stuck – Mechanics secret tips
I know the feeling, FRUSTRATION. but we’ll get it figured out. The blade bolt can be stuck for a few different reasons. Usually, it’s a combination of rust and over-tightening.
The easiest way to remove a stuck blade bolt is with an impact tool; they make the whole job look easy. Other options include:
You may not have an impact, so I’ll show you a few different options. Some of these options may not suit you; it’ll depend on what tools you have available. Best to don a pair of work gloves. Stuck bolts usually mean slipping tools.
Removing A Rounded Bolt
Over-tightening is common. Mower blades are designed to be tightened to a specific torque, which isn’t as tight as you might expect. That’s because they’re designed to slip if they hit a solid object. The slipping protects the engine from serious damage associated with a curbstone strike.
Also common is turning the bolt the wrong way; hey, it could happen to a bishop. All single-blade walk-behind mowers will have what’s known as a right-hand thread. That means, to loosen the bolt, you turn it to the left. (counter-clockwise)
I cover all you need to know pretty well in this post, but if you need more help, check out the following videos:
Blade Bolt Torque
Mower blade bolts should be torqued to spec. These bolts are usually over-tightened, and when you add corrosion, removing them can be a headache.
Only some large twin blades walk-behind mowers and some lawn tractor mowers are likely to have one only left-hand threaded blade bolt; the other bolt will be a regular right-hand thread.
How do you know which is which?
Simple, if the blade is designed to cut turning right (viewed from above), then it will be a right-hand thread; this is the most common type. To loosen a right-hand thread, you turn it to the left.
The same idea applies to twin-blade tractor mowers. However, a left-hand thread is common on some lawn tractor mowers.
So, if the blade cuts grass turning to the right, as before, it’s likely a regular right-hand thread (left to loosen). But it’s not uncommon for a tractor mower to have one of the blades turn to the left when cutting, and that usually means it’s a left-hand thread (check your owner manual) to loosen a left-hand thread, turn it to the right.
L/H – R/H Thread
A r/h thread loosens to the left. This is the most common type of thread. (counterclockwise)
A l/h threaded bolt loosens to the right. (clockwise)
Typical torque specs for blade bolts are anywhere from 35 ft. lbs. to 90 ft. lbs., you’ll need to check the spec of your mower, it’s important to get it right.
Most of the time blade bolts just get buttoned uptight and aren’t torqued to spec, and that’s OK, but you run the risk of bending the crankshaft if you hit a solid object. I advise using a torque wrench, it’s a lot cheaper than a new mower engine.
Torque wrenches are easy to use, they come in inch-pounds for smaller torque specs, but for mowers, you’ll need foot-pounds. A torque wrench from 30 to 100 foot-pounds is about right.
If you don’t have or can’t borrow one, check out this post on my 1/2 drive Teng Torque, it won’t break the bank, it covers 30 to 150 ft. lbs., it’s simple to use, calibrated from the factory, and has a flexible working range.
I get my torque wrenches calibrated every year but it gets a lot of use. If you set your torque wrench to zero after you use it and don’t throw it around, it should stay calibrated for years.
Damage – The bolt on the right has a rounded head, this kind of damage happens when a tool slips on a bolt head, or corrosion deforms it. Getting the bolt out presents a challenge.
A rounded bolt head is a real pain in jacksie. It usually happens when the bolt is old and corrosion has deformed it. Worn or damaged tools will give you the same result.
How to EASILY replace the blade and blade adapter on your push mower.
It can also happen if the wrong size tool is used. An American mower may use imperial size nuts and bolts, I know the more modern kit is metric and some mowers are a mix of both. If your mower is European or Asian it will be metric sizes.
The trouble is you can get an imperial wrench to almost fit a metric bolt, but it’s loose and will slip, which rounds the bolt head. Typical bolt sizes for mower blade bolts are Imperial 1/2″, 5/8″, 3/4″ and Metric sizes 13mm, 14mm, 15mm, 16mm, and 17mm.
Imperial or Metric, be sure your tools are a good fit.
Tools You’ll Need
Impact power tools are designed for this exact job. They cause a hammering action which helps reduce the bolt thread friction and breaks any corrosion loose. So if you have an air or battery impact tool, you going to feel like a superhero when that bolt just walks out.
Basic tools needed assuming you don’t have an impact tool: wire brush, wd40, ratchet sockets, selection of wrenches.
Other tools you’ll need if things don’t go exactly to plan: breaker bar, hammer chisel, butane torch, and if everything goes to crap, a Mig welder. In my workshop, I use an air impact tool, if you haven’t got one or can’t borrow I have other solutions for you.
But the tool I am least likely to be without is an impact tool, it just makes life really easy and saves so much time. The coolest thing about the latest generation impact tools is their mobility, cordless now packs the power of an air tool. Great for around the home and for flat wheel emergency, use it to run the jack-up and take the nuts off.
Although I still use air in the workshop, I bought a 20v Ingersoll Rand cordless for mobile repairs, I know they ain’t cheap but you won’t ever need to buy another.
If you do buy an impact tool, you’ll need to buy impact sockets too. Sure you can use regular sockets, but you run the risk of them shattering. Anyway, you’ll find all these tools on the “Small engine repair tools page”.
Tool Up – Most stuck bolts won’t need all these tools, but some do.
Removing The Bolt
Removing a stuck bolt involves trying different solutions until you ring the bell. In the first attempts, we’ll try the simple stuff and if that doesn’t move it, I have lots more ideas.
Before we start any work on our mower we need to make it safe. Pull the plug wire off and set it away from the plug. Turn your gas off if you have a gas tap, if you don’t know where your gas tap is check out “Gas tap location”.
WD40 is my favorite tool, it solves lots of problems, I also like a product called nut buster, it’s formulated for dissolving rust. Try spraying the bolt liberally above and below the blade, and allow it time to work into the threads.
Disable Mower – For safety, let’s remove the plug wire and turn off the gas.
Turn the mower over with the carburetor side facing up, stops gas leaking on the floor. (see tilting mower over)
Wire Brush to remove any rust. Wd40 Spray front and rear of the bolt and give it some time to soak in.
Impact Tool – By far the preferred way to remove a bolt. An Impact gun hammers the bolt as well as twists it, this loosens the corrosion between the threads.
An impact tool will remove the bolt in seconds and you won’t need to lock the blade. But if the bolt head is rounded, the impact tool is of no use. You’ll need a different solution.
Check out the Amazon link, some of these impact wrench surprised me.
Lock Blade – If you are not using an impact tool we’ll need to use a piece of timber to lock the blade against the body. Longer timber is better than shorter. Cut a length to suit.
Good Fit – Select a socket (6 points preferably) and check the fit. Turn the ratchet left to loosen. Using a breaker bar, or if you don’t have to improvise with your ratchet and some pipe.
Pushing down on the pipe will give you the extra power you need to break it loose. Just be sure the socket is a good fit, and it stays on the bolt head when you’re applying force.
Wrench Leverage – Turn the Wrench left to loosen. If you don’t have a ratchet and breaker bar, try 2 interlocked wrench’s for extra leverage, or use a hammer to shock the bolt.
If it still won’t budge, try tightening it slightly, this often helps, odd I know!
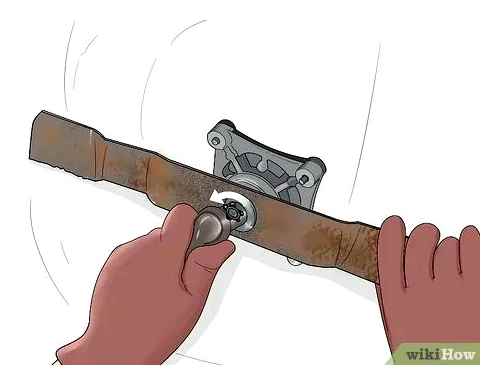
Striking – Try striking two hammers sharply (wear eye protection) while one is placed against the bolt head, this can help break loose any corrosion on the threads. If the head of the bolt is rounded, move on to the next solution.
Rounded Bolt – If your bolt head is rounded, try a vice grip. Get it as tight as you can, and try hitting it to the left sharply with a hammer.
Not all vice grips are the same, for this application you’ll need a flat jawed set. Check out this post on Vice-grips tools.
Chisel – This method is pretty effective, but you’ll need a new bolt, sharp metal working chisel, and a heavy hammer. With the chisel and hammer, take a sideways and downward aim at the bolt, we’re attempting to loosen it by turning it left. This will require good aim, so now’s a good time for those gloves.
Heat – Ordinarily I’ll tell you to get some heat on the bolt, the reason I haven’t introduced it earlier is that it comes with the risk of damaging the crankshaft nylon seal, which would cause the engine to leak oil.
The risk of this is fairly small, once you direct the flame and only use a small amount. We’re not going to redden the bolt, just going to heat it up.
Maybe 2 minutes with a butane torch directed at the bolt. You can now try heat with any combination of the above methods. Heat is very successful at helping move stuck bolts.
Welding – This method will obviously require a welder, when I get a really stubborn bolt with a rounded head, I take a new bolt and weld it to it. This gives me a not-so-pretty but clean bolt head to work with.
This solution has never failed me yet. You’ll need to replace the bolt. Blade bolts have a fine thread, they are a specialized bolt, getting one in the hardware store isn’t advisable.
Torque – Finally, you’ll have to move your timber to lock the blade in the other direction and torque your new bolt to spec.
Check out this post to see why it’s important to torque your blade bolt.
Related Questions
The spindle turns when removing the blades? The easiest way to prevent the blade from turning while loosening the blade bolt is to use a large block of wood to lock the blade against the mowing deck.
Lawnmower blade bolt direction? Turn the mower on its side, carburetor side up, turn the blade bolt to the left (anticlockwise) to loosen.
Hey, I’m John, and I’m a Red Seal Qualified Service Technician with over twenty-five years experience.
I’ve worked on all types of mechanical equipment, from cars to grass machinery, and this site is where I share fluff-free hacks, tips, and insider know-how.
And the best part. it’s free!
The LawnmowerBlade that cuts itself sharp
Any landscaping professional knows that sharper mower blades make for sharper-looking lawns, but blades that maintain their sharpness can also improve a lawn-care business’s on-site efficiency and cut its maintenance costs.
Mowing lawns with LaserEdge® Eversharp™ blades means minimal maintenance and downtime associated with blade sharpening, increasing overall uptime and profits.
Redefining the Cutting Edge
High-quality, hardened steel blades equipped with the LaserEdge® Eversharp™ technology on their cutting edges have demonstrated their toughness and durability in field tests, even in the most abrasive conditions.
In one test, the LaserEdge® Eversharp™ cutting edge withstood 30 hours in severe sand conditions and became sharper during use. In a highly controlled durability test, the blade’s advanced technology performed remarkably, enduring multiple impacts from a 1-inch steel stake traveling at more than 200 mph.
How To Replace A Lawn Mower Blade & Blade Adapter In Less Than 2 Minutes!
Hours of Toughness
In an intense 50-hour field test in central Florida, mower blades with LaserEdge® Eversharp™ technology proved they “cut themselves sharp” when a new cutting edge emerged as the blade wore down.
In the test, a brand-new mower blade had LaserEdge technology applied on one cutting edge and was left untreated on the other edge. After putting the blade to work for 50 hours, the results were clear. The LaserEdge cutting edge was still sharp, and the untreated side was dulled and worn away.
Results will vary based on grass type, soil type and condition, and geographical region.
Cutting Costs, Boosting Bottom Lines
Increased Fuel Efficiency
Dull blades produce resistance, putting strain on the mower deck and making it difficult to maintain speed and efficiency. Mowing with a dull blade can reduce fuel economy by as much as 22 percent, which increases operating costs and reduces productivity.
Healthier, Greener Lawns
A dull blade shreds and tears grass, leaving it vulnerable to dehydration, browning, and disease. LaserEdge® blades cut grass cleanly, making it easier to deliver high-quality lawn care and in-demand enhancements such as lawn striping.
Blades Stay Sharp Longer
In abrasive conditions, a blade can get dull in as little as four hours, and lawn-care operations can go through dozens of blades a week, resulting in downtime and lost revenue. No matter the environment, a LaserEdge blade “cuts itself sharp,” reducing time spent sharpening.
Less Mower Maintenance
Blade replacement can be a dangerous undertaking. Attacking a dulled edge with a makeshift sharpening tool can irreversibly damage a blade and put workers in danger. LaserEdge blades dramatically reduce the frequency and risk of blade sharpening.
D.H. Steinegger, R.C. Shearman, T.P. Riordan and E.J. Kinbacher, “Mower Blade Sharpness Effects on Turf,” in Agronomy Journal 75 (1983): 479–480.
Savings Calculator
See how much you can save with LaserEdge® Eversharp™ lawnmower blades.
- 432 Saved on Fuel Cost
- 1575 Saved on Blade Sharpenings
- 2625 Additional Revenue Opportunity
- ( 960 ) Premium Spent on LaserEdge Blades
Calculations above are based off the following: type of lawn mower: 3-blade, 60-inch cut, gas-powered. Average gas price: 2.38. Lawn mower blade pricing: standard blade is 16. Average cost of sharpening: 5 per blade. Fuel savings: 11%. Blade removal and re-installation time: 30 minutes.
Frequently Asked Questions
How does LaserEdge ® Eversharp™ maintain a cutting edge that “cuts itself sharp”?
The LaserEdge Eversharp technology is applied to the underside of the cutting edge. As the blade cuts grass, the original blade material begins to wear away and exposes a new LaserEdge cutting edge, which is even sharper than the blade’s original sharpness.
Will I need to sharpen my LaserEdge ® Eversharp™ lawnmower blades?
LaserEdge blades “cut themselves sharp” and require minimal sharpening, but you should monitor cutting-edge wear. Sharpening is only needed if the new LaserEdge cutting edge is not presenting itself.
If I find the need to sharpen my LaserEdge ® Eversharp™ mower blades, how do I do so?
If you choose to re-sharpen your LaserEdge blade, do so in a safe, controlled setting with the proper equipment. Remember to prep the machine and remove the spark plug before removing the blade. Secure the blade to a work surface with a vise or clamp, and sharpen the blade with a file, bench grinder, or professional blade grinder. Ensure the blade is evenly sharpened and balanced before remounting on the mower deck.
How often will I need to change my LaserEdge Eversharp™ lawnmower blades?
The LaserEdge blade is designed to “cut itself sharp” and requires minimal sharpening over its life. The overall life of the blade will vary due to conditions, but its lifespan should be at least as long as a standard blade’s. In several of our tests, we found LaserEdge blades had longer lives.
How do LaserEdge ® Eversharp™ lawn mower blades perform in abusive mowing conditions?
The LaserEdge technology is an extremely hard, wear-resistant material. If you mow in conditions that regularly include rocks, curbs, out-cropping stones, and other hard objects, LaserEdge lawn mower blades may not be suitable for your operation.
A good test to see if LaserEdge is right for your operation is to inspect your worn blades. Worn blades that show excessive gouging, deep gashes, or large scraps may not see all the benefits of LaserEdge.
How long will it take for LaserEdge ® Eversharp™ to take effect?
This is highly dependent on geography, soil type, and cutting conditions. The magic of LaserEdge happens when the base blade material wears away at a faster rate than the harder, more wear-resistant LaserEdge material. In highly abrasive soil conditions (like sand), we have experienced standard blades wearing out in as few as 50 hours with blade sharpenings occurring as frequently as every 4 to 8 hours. In these areas, LaserEdge began exhibiting self-sharpening in as little as 5 to 10 hours. When using LaserEdge, these blades required no sharpening over the entire life of the blade. In less abrasive conditions, LaserEdge technology will take effect but over a longer time period.
How much do LaserEdge ® Eversharp™ lawn mower blades cost?
The price of LaserEdge blades will vary depending on the OEM and blade configuration. Although the LaserEdge will typically be more expensive than a standard blade, the benefits of consistently having a sharp cutting edge and increased uptime surpass the increase in blade price (see Savings Calculator).
Where can I purchase LaserEdge ® Eversharp™ lawnmower blades?
Most lawn mower Original Equipment Manufacturers (OEMs) are currently in the process of adding LaserEdge to their product line-ups. Be sure to talk to your local dealer about LaserEdge.
How do I get more information on LaserEdge ® Eversharp™ blades?
Fill out the contact form at the bottom of this page, and Fisher Barton will email you updates on product availability and news.
Get LaserEdge® For Your Business
Ready to bring this cost-effective, state-of-the-art mower blade technology to your lawn-care business? LaserEdge blades are currently available through select OEMs.
Available for the following brands through their independent dealers: (Click on the logo for information on available part numbers)
Connect With An Expert
We’re here to help and would love the opportunity to discuss your technical questions or application challenges.