How to properly cut metal with a cutter
4 Igniting the torch and heating the metal
Before igniting the torch, you need to:
- make sure that all connections are tight (valves, pressure gauges, hoses, other fittings). any gas leak can instantly cause a fire;
- check again the place of work for the absence of flammable materials, strangers (especially children), animals;
- make sure you are ready to work;
- wear safety glasses and gloves.
The acetylene valve is then opened on the torch, allowing the oxygen that is in the mixing chamber to escape. A few seconds are enough for this. Then the valve is turned on until it becomes audible that the acetylene is barely coming out. A special lighter is placed in front of the cutter, as shown in the video, so that its inside touches the mouthpiece. Then press on the lighter lever. When the sparks produced ignite the acetylene, a small yellow flame should form in front of the mouthpiece.
By turning the gas supply valve, the flame length is increased to about 25 cm. The torch should start at the very mouth of the torch. The flame will burst from it or jump when too much acetylene is supplied.
Open the front oxygen valve slowly. In this case, the flame should change color from yellow to blue. at this moment, the supply of such an amount of oxygen will be provided, which is sufficient for the complete combustion of acetylene. The oxygen supply should be increased until the inner blue flame tongue diminishes and contracts towards the mouthpiece.
The oxygen valve is opened even further. the size of the torch is increased until the length of the inner flame becomes slightly greater than the thickness of the steel being cut (for cold-rolled sheet thickness of 9.5 mm, an excess of the flame length by 1.3 mm is sufficient). When you hear “puffing” or the blue flame seems to be feathery and unstable, it means too much oxygen is being supplied. It is reduced until the entire flame is stabilized, and the inner flame takes the shape of a clear cone.
The inner flame is brought with its very tip to the surface of the steel being processed. It is heated until a puddle of molten glowing metal forms at the point of contact. The tip of the flame must be held still at a distance of about 10 mm from the surface of the steel as shown in the video so that all the heat is concentrated in one area.
2 Preparing the site and conditions for safe and comfortable work
To ensure safe work using a gas torch, the following rules and recommendations must be followed:
- To do the work, choose only a place in an ideally ventilated room or in the open air.
- Can be cut away from flammable substances and materials.
- The floor in the room must be concrete or earthen.
- The surface of the earth or concrete must be free of any foreign objects and materials within a radius of at least 5 m, since sparks from the cut metal fly up several meters and can set fire to dry rags, shavings, paper, dried plants or leaves.
- Place the metal to be cut on a suitable support to use the torch at a comfortable working height. For these purposes, it is best to use a steel table.
- Do not allow the flame to touch concrete (especially if it is fresh). this will cause its expansion and subsequent intense cracking with small fragments of concrete flying out of it.
- It is strictly forbidden to use flammable surfaces as workers, or on which flammable, explosive materials are spilled.
- The place of the metal cut is marked as shown in the video.
How to use a gas torch. the basics of safe and quality work
Cutting metal with an oxyacetylene torch requires certain precautions and the correct sequence of actions. This gas equipment is classified as flammable and explosive.
3 Preparing and setting up gas cutting equipment
To work safely with a gas torch, it is important not only to correctly select the appropriate set of equipment, but also to connect and configure it correctly. First, the appropriate tubes are connected to the oxygen and acetylene cylinders. Oxygen hoses and containers are usually green, acetylene ones are red.
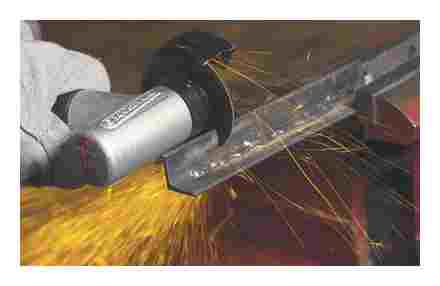
At both ends of the hoses, install safety seals (a device that retards back blows of the flame).
The next step is to check that the acetylene supply is working properly. First, close the flow control valve. turn the T-handle back several times. On the cylinder, in its upper part, open the valve. turn it 1 turn of the hand. They do this for security purposes. The acetylene pressure in the cylinder must not be allowed to exceed 1 atm. in the case of high pressure, this gas becomes unstable and may even spontaneously explode or ignite. To check that the acetylene pressure is adjusted correctly, proceed as follows:
- The main valve of the vessel is unlocked, then the control valve is opened by turning the knob clockwise. This should be done very slowly, observing the readings of the pressure gauge installed at the low pressure outlet. The control valve is opened until the pressure becomes 0.34-0.54 atm.
- Then air is blown from the hose. the acetylene valve of the torch is opened until the sound of escaping gas appears. After that, they look at the readings of the low pressure gauge. During purging, the pressure value must be stable (if not, then make sure that the regulator is installed correctly).
- The valve on the torch is closed.
They check and adjust the oxygen supply. turn off the regulator of its supply (twist it down), and then adjust the pressure. To reduce the oxygen supply, turn the manometer knob a few turns back. Then follow the sequence of the following steps:
- On the oxygen cylinder, the main valve is fully unlocked. It is double-seated and in the case of its partial opening due to high pressure in the cylinder (150 atm) oxygen escapes around the sealing ring of the valve stem connection.
- Slowly open the flow regulator, following the readings of the pressure gauge installed at the low pressure outlet, until the oxygen pressure is set within 1.7-2.7 atm.
- The atmosphere is blown out of the hose. the oxygen valve is opened on the torch. The cutter has 2 valves for oxygen: one closer to the hose, controls the supply to the chamber, where oxygen is mixed with acetylene to heat the steel (combustion of the mixture), as well as to supply it to the oxygen nozzle for cutting; the other is located further away and supplies oxygen to a separate cutting nozzle (until this valve is open or the special cutting lever is released, oxygen should not come out of the cutting nozzle). First, the first valve is opened and turned several times to ensure sufficient oxygen supply for both functions. After that, the second (front) valve is slightly opened. for a while until the hose is cleaned (3-5 s for a 7.5 m tube).
- The front valve is closed.
1 Gas torch basics
The process of cutting with a gas torch occurs due to the combustion of metal in a stream of oxygen supplied under pressure. The alloy must be preheated to the required operating temperature using a burning mixture of acetylene and oxygen. The only metals that can be cut in this way are various grades of carbon steel and unalloyed steel. Stainless steel, non-ferrous metals and alloys cannot be cut with an oxygen-acetylene cutter.
To perform this type of work, in addition to the corresponding set of gas equipment, you will need the following:
- Fire extinguisher.
- Protective equipment: special glasses; thick leather gloves; sturdy work shoes with leather soles.
- Appropriate clothing. It is recommended to wear fire resistant clothing, but if not available, a well-fitting cotton will do. Do not wear things made of synthetic and flammable fabrics, loose fit, with torn or worn edges.
- Measuring and marking tools: ruler, square and soapstone pencil.
- Torch lighter. designed to properly ignite the torch flame. It is very dangerous to use ordinary matches, lighters.
5 Cutting steel with a gas torch
The handle of the gas cutting valve is slowly released downward. a stream of oxygen is supplied, igniting the molten metal. If a violent reaction immediately begins to occur, then the steel caught fire and you can continue to gradually increase the oxygen pressure until its jet cuts through the material. When the reaction does not proceed, the metal is not heated enough to ignite in a stream of oxygen. It is necessary to add oxygen to the heating flame and allow it to heat up the steel.
When the oxygen jet begins to cut, the cutter mouthpiece is slowly moved along the cut line. At the same time, almost all processing products (molten slag, sparks) are blown away by a jet to the rear side of the cutting zone, as shown in the video. If this flow comes back or slows down, then reduce the speed of the torch or stop it and warm up the material even more (it is better to work very slowly than trying to cut too fast). Cutting continues until the intended cutting or separation of the metal is completed.
Propane to oxygen ratio
Such adjustment is carried out according to the recommendations of reference books, where tables and diagrams are available, in the absence of the necessary literature, you must check the technology specified in the product documents.
In the absence of regulatory documents, the ratio of one part of propane to ten parts of oxygen is used.
13 Ways to Cut Metal
The question of choosing which is better
Today the following are popular:
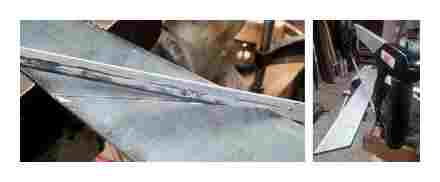
- all the same good old Mayak (2-2R LEVER; 2-01) and RZP-02M
- Acetylene P1A LATION with extended handle and PC-2A-100
- Universal (P2-01 UShL; P3 P; R1P) with in-head gas mixing and gas mixing in the mouthpiece.
- P3-300K cutter with KR valve. lasts ten times longer than injection
Torch Assembly Instructions
- Reducers are installed: blue is screwed onto an oxygen cylinder (hereinafter referred to as O2), red. onto propane. Check the condition of the rubber seals before tightening. Examine the valve with O2. Traces of oil and grease on its surface are not allowed (be careful, it may cause an explosion)
- Defects on the union are not allowed. If present, they are edited with a file. If this is not done, the rubber gasket of the gearbox will etch.
- Match hoses by threads (left-handed, right-handed).
Also inspect them carefully for damage. They are connected to the cutter and the gear with clamps.
Safety precautions: do not purge the propane sleeve with oxygen or change the sleeves between each other. - on the union with fuel. backstroke valve is installed.
How to work with a gas torch. correct ignition of the mixture
- A little O2 and gas lamb opens (half a turn), the mixture is ignited.
- Now you need to rest against the metal and add O2 before the crown appears. everything is ready to perform the tasks
- The valves are closed in the opposite direction. Combustible gas always closes first, then O2
The most important thing in the work to remember is that if the flame is attenuated, in order to stop the operation and avoid a kickback, it is necessary to shut off the propane supply and add O2 for a few seconds.
If you close O2, an explosion can thunder.
How to use a Cutting Disc with an Angle Grinder
Newbie tips for using a gas torch
Due to the appearance on the market of construction tools of various types of cutters, affordable and relatively easy to use, the question of how to use a cutter is becoming more and more relevant. In order to competently and safely perform work using such equipment, you must first study its features and operating rules.
How to properly cut metal with an Oxy-propane cutter?
Compared to gas welding, gas cutting requires much less skill from a person. Therefore, mastering a gas torch is not that difficult. It is enough to understand how to do it correctly. The most widespread in our time are propane cutters. They use propane and oxygen together, since their mixture gives the highest combustion temperature.
The propane cutter is designed for manual separation oxyfuel cutting of carbon and low-alloy steels using propane.
How much gas is consumed
Gas consumption when cutting metal with a propane-oxygen cutter depends on the thickness of the structure and the configuration of the cut. For clarity, we present the table below:
Workpiece size (thickness), mm | Time per hole, sec | Cut size (width), mm | Consumption, per cut m3 | |
propane | oxygen | |||
4.0 | 5-8 | 2.5 | 0.035 | 0.289 |
10.0 | 8-13 | 3.0 | 0.041 | 0.415 |
20.0 | 13-18 | 4.0 | 0.051 | 0.623 |
40.0 | 22-28 | 4.5 | 0.071 | 1,037 |
60.0 | 25-30 | 5.0 | 0.087 | 1,461 |
Gas consumption is significantly reduced when surfacing or brazing is performed.
Working with a gas torch presupposes careful observance of safety precautions, as well as rules and instructions for working with equipment.
At the same time, it does not present any particular technological complexity and can be easily performed with an acceptable result in terms of quality, even without special education.
It is interesting to know the opinion of experts about professional secrets that probably exist in large numbers. They can be expressed in x to the article.