Mtd mower blade removal. Lawn Mower Blade Bolt Stuck – Mechanics secret tips
Lawn Mower Blade Bolt Stuck – Mechanics secret tips
I know the feeling, FRUSTRATION. but we’ll get it figured out. The blade bolt can be stuck for a few different reasons. Usually, it’s a combination of rust and over-tightening.
The easiest way to remove a stuck blade bolt is with an impact tool; they make the whole job look easy. Other options include:
You may not have an impact, so I’ll show you a few different options. Some of these options may not suit you; it’ll depend on what tools you have available. Best to don a pair of work gloves. Stuck bolts usually mean slipping tools.
Removing A Rounded Bolt
Over-tightening is common. Mower blades are designed to be tightened to a specific torque, which isn’t as tight as you might expect. That’s because they’re designed to slip if they hit a solid object. The slipping protects the engine from serious damage associated with a curbstone strike.
Also common is turning the bolt the wrong way; hey, it could happen to a bishop. All single-blade walk-behind mowers will have what’s known as a right-hand thread. That means, to loosen the bolt, you turn it to the left. (counter-clockwise)
I cover all you need to know pretty well in this post, but if you need more help, check out the following videos:
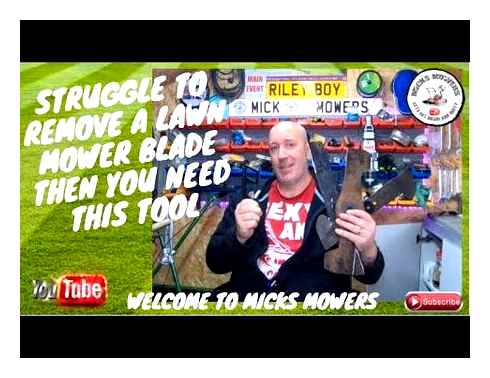
Blade Bolt Torque
Mower blade bolts should be torqued to spec. These bolts are usually over-tightened, and when you add corrosion, removing them can be a headache.
Only some large twin blades walk-behind mowers and some lawn tractor mowers are likely to have one only left-hand threaded blade bolt; the other bolt will be a regular right-hand thread.
How do you know which is which?
Simple, if the blade is designed to cut turning right (viewed from above), then it will be a right-hand thread; this is the most common type. To loosen a right-hand thread, you turn it to the left.
The same idea applies to twin-blade tractor mowers. However, a left-hand thread is common on some lawn tractor mowers.
So, if the blade cuts grass turning to the right, as before, it’s likely a regular right-hand thread (left to loosen). But it’s not uncommon for a tractor mower to have one of the blades turn to the left when cutting, and that usually means it’s a left-hand thread (check your owner manual) to loosen a left-hand thread, turn it to the right.
L/H – R/H Thread
A r/h thread loosens to the left. This is the most common type of thread. (counterclockwise)
A l/h threaded bolt loosens to the right. (clockwise)
Typical torque specs for blade bolts are anywhere from 35 ft. lbs. to 90 ft. lbs., you’ll need to check the spec of your mower, it’s important to get it right.
Most of the time blade bolts just get buttoned uptight and aren’t torqued to spec, and that’s OK, but you run the risk of bending the crankshaft if you hit a solid object. I advise using a torque wrench, it’s a lot cheaper than a new mower engine.
Torque wrenches are easy to use, they come in inch-pounds for smaller torque specs, but for mowers, you’ll need foot-pounds. A torque wrench from 30 to 100 foot-pounds is about right.
If you don’t have or can’t borrow one, check out this post on my 1/2 drive Teng Torque, it won’t break the bank, it covers 30 to 150 ft. lbs., it’s simple to use, calibrated from the factory, and has a flexible working range.
I get my torque wrenches calibrated every year but it gets a lot of use. If you set your torque wrench to zero after you use it and don’t throw it around, it should stay calibrated for years.
Damage – The bolt on the right has a rounded head, this kind of damage happens when a tool slips on a bolt head, or corrosion deforms it. Getting the bolt out presents a challenge.
A rounded bolt head is a real pain in jacksie. It usually happens when the bolt is old and corrosion has deformed it. Worn or damaged tools will give you the same result.
It can also happen if the wrong size tool is used. An American mower may use imperial size nuts and bolts, I know the more modern kit is metric and some mowers are a mix of both. If your mower is European or Asian it will be metric sizes.
The trouble is you can get an imperial wrench to almost fit a metric bolt, but it’s loose and will slip, which rounds the bolt head. Typical bolt sizes for mower blade bolts are Imperial 1/2″, 5/8″, 3/4″ and Metric sizes 13mm, 14mm, 15mm, 16mm, and 17mm.
Imperial or Metric, be sure your tools are a good fit.
Tools You’ll Need
Impact power tools are designed for this exact job. They cause a hammering action which helps reduce the bolt thread friction and breaks any corrosion loose. So if you have an air or battery impact tool, you going to feel like a superhero when that bolt just walks out.
Basic tools needed assuming you don’t have an impact tool: wire brush, wd40, ratchet sockets, selection of wrenches.
Other tools you’ll need if things don’t go exactly to plan: breaker bar, hammer chisel, butane torch, and if everything goes to crap, a Mig welder. In my workshop, I use an air impact tool, if you haven’t got one or can’t borrow I have other solutions for you.
But the tool I am least likely to be without is an impact tool, it just makes life really easy and saves so much time. The coolest thing about the latest generation impact tools is their mobility, cordless now packs the power of an air tool. Great for around the home and for flat wheel emergency, use it to run the jack-up and take the nuts off.
Although I still use air in the workshop, I bought a 20v Ingersoll Rand cordless for mobile repairs, I know they ain’t cheap but you won’t ever need to buy another.
If you do buy an impact tool, you’ll need to buy impact sockets too. Sure you can use regular sockets, but you run the risk of them shattering. Anyway, you’ll find all these tools on the “Small engine repair tools page”.
Tool Up – Most stuck bolts won’t need all these tools, but some do.
Removing The Bolt
Removing a stuck bolt involves trying different solutions until you ring the bell. In the first attempts, we’ll try the simple stuff and if that doesn’t move it, I have lots more ideas.
Before we start any work on our mower we need to make it safe. Pull the plug wire off and set it away from the plug. Turn your gas off if you have a gas tap, if you don’t know where your gas tap is check out “Gas tap location”.
WD40 is my favorite tool, it solves lots of problems, I also like a product called nut buster, it’s formulated for dissolving rust. Try spraying the bolt liberally above and below the blade, and allow it time to work into the threads.
Disable Mower – For safety, let’s remove the plug wire and turn off the gas.
Turn the mower over with the carburetor side facing up, stops gas leaking on the floor. (see tilting mower over)
Wire Brush to remove any rust. Wd40 Spray front and rear of the bolt and give it some time to soak in.
Impact Tool – By far the preferred way to remove a bolt. An Impact gun hammers the bolt as well as twists it, this loosens the corrosion between the threads.
An impact tool will remove the bolt in seconds and you won’t need to lock the blade. But if the bolt head is rounded, the impact tool is of no use. You’ll need a different solution.
Check out the Amazon link, some of these impact wrench surprised me.
Lock Blade – If you are not using an impact tool we’ll need to use a piece of timber to lock the blade against the body. Longer timber is better than shorter. Cut a length to suit.
Good Fit – Select a socket (6 points preferably) and check the fit. Turn the ratchet left to loosen. Using a breaker bar, or if you don’t have to improvise with your ratchet and some pipe.
Pushing down on the pipe will give you the extra power you need to break it loose. Just be sure the socket is a good fit, and it stays on the bolt head when you’re applying force.
Wrench Leverage – Turn the Wrench left to loosen. If you don’t have a ratchet and breaker bar, try 2 interlocked wrench’s for extra leverage, or use a hammer to shock the bolt.
If it still won’t budge, try tightening it slightly, this often helps, odd I know!
Striking – Try striking two hammers sharply (wear eye protection) while one is placed against the bolt head, this can help break loose any corrosion on the threads. If the head of the bolt is rounded, move on to the next solution.
Rounded Bolt – If your bolt head is rounded, try a vice grip. Get it as tight as you can, and try hitting it to the left sharply with a hammer.
Not all vice grips are the same, for this application you’ll need a flat jawed set. Check out this post on Vice-grips tools.
Chisel – This method is pretty effective, but you’ll need a new bolt, sharp metal working chisel, and a heavy hammer. With the chisel and hammer, take a sideways and downward aim at the bolt, we’re attempting to loosen it by turning it left. This will require good aim, so now’s a good time for those gloves.
Heat – Ordinarily I’ll tell you to get some heat on the bolt, the reason I haven’t introduced it earlier is that it comes with the risk of damaging the crankshaft nylon seal, which would cause the engine to leak oil.
The risk of this is fairly small, once you direct the flame and only use a small amount. We’re not going to redden the bolt, just going to heat it up.
Maybe 2 minutes with a butane torch directed at the bolt. You can now try heat with any combination of the above methods. Heat is very successful at helping move stuck bolts.
Welding – This method will obviously require a welder, when I get a really stubborn bolt with a rounded head, I take a new bolt and weld it to it. This gives me a not-so-pretty but clean bolt head to work with.
This solution has never failed me yet. You’ll need to replace the bolt. Blade bolts have a fine thread, they are a specialized bolt, getting one in the hardware store isn’t advisable.
Torque – Finally, you’ll have to move your timber to lock the blade in the other direction and torque your new bolt to spec.
Check out this post to see why it’s important to torque your blade bolt.
Related Questions
The spindle turns when removing the blades? The easiest way to prevent the blade from turning while loosening the blade bolt is to use a large block of wood to lock the blade against the mowing deck.
Lawnmower blade bolt direction? Turn the mower on its side, carburetor side up, turn the blade bolt to the left (anticlockwise) to loosen.
Hey, I’m John, and I’m a Red Seal Qualified Service Technician with over twenty-five years experience.
I’ve worked on all types of mechanical equipment, from cars to grass machinery, and this site is where I share fluff-free hacks, tips, and insider know-how.
And the best part. it’s free!
Rouge River Workshop
Queen Anne Table Legs? We Don’t Need No Stinking Queen Anne Table Legs!
Sunday, April 13, 2014
MTD 12B-443F500 Blade Removal And Sharpening
[What follows is specifically about the MTD mulching lawnmower model cited in the title of this post. Much of it is applicable to any rotary mower.]
Here’s a view of the blade’s fastening underneath.
That bolt head takes a 5/8 wrench. A shallow 1/2 square drive socket wrench on a breaker bar is ideal for loosening the bolt. Hold the blade end steady with a rag to save wear-and-tear on your hand. (The bolt will be quite tight, but I’ve never encountered a seized one.) Unscrew the bolt and the big washer and the blade will be free to come off.
Here’s a view of the blade fastening hardware off the mower.
How I Removed a Stuck Lawn Mower Blades After Multiple Failures
The bolt is SAE grade 8; 3/8. 24 x 2 1/2, with an oversize (5/8 A/F) head. (The standard hex head size for 3/8 bolts is 9/16 A/F.) At reassembly, [1] it doesn’t hurt to apply some oil or grease to the bolt’s threads as an anti-seize measure.
This old blade is in rough shape. It looks like it was never sharpened while it was in service, and it’s been outside rusting on an idle mower for a few years. Here’s a view of one of the blade’s ends.
Proper Way To Tip A Lawn Mower Over
That’s a grass flogger, not a grass cutter. Here’s a blade end after a lot of grinding with a belt grinder. [2]
It’s still not perfect and never will be, but it will cut grass.
That upward-curved portion of the blade complicated the grinding job a bit. I take it that that’s the part of the blade that does the mulching.
[1] Pay close attention to getting the blade back on the right way up. Inadvertently flipping the blade is an easy mistake to make. I once picked up a perfectly good mower from the side of the road that turned out to have its blade on upside down. I suppose the owner got fed up with the poor cutting action, and discarded the mower.
[2] A belt grinder with a 1 wide belt is the best tool I know of for this sort of sharpening chore.- far superior to a wheel grinder. See this post for more information on a suitable belt grinder.
A lot of sharpening instruction I’ve seen makes much of checking and correcting blade balance. You’d have to do a pretty uneven grinding job to affect blade balance to any significant degree. Blade balance is not something I fret about; I just try to do a reasonably even grinding job.
The LawnmowerBlade that cuts itself sharp
Any landscaping professional knows that sharper mower blades make for sharper-looking lawns, but blades that maintain their sharpness can also improve a lawn-care business’s on-site efficiency and cut its maintenance costs.
Mowing lawns with LaserEdge® Eversharp™ blades means minimal maintenance and downtime associated with blade sharpening, increasing overall uptime and profits.
Redefining the Cutting Edge
High-quality, hardened steel blades equipped with the LaserEdge® Eversharp™ technology on their cutting edges have demonstrated their toughness and durability in field tests, even in the most abrasive conditions.
In one test, the LaserEdge® Eversharp™ cutting edge withstood 30 hours in severe sand conditions and became sharper during use. In a highly controlled durability test, the blade’s advanced technology performed remarkably, enduring multiple impacts from a 1-inch steel stake traveling at more than 200 mph.
Hours of Toughness
In an intense 50-hour field test in central Florida, mower blades with LaserEdge® Eversharp™ technology proved they “cut themselves sharp” when a new cutting edge emerged as the blade wore down.
In the test, a brand-new mower blade had LaserEdge technology applied on one cutting edge and was left untreated on the other edge. After putting the blade to work for 50 hours, the results were clear. The LaserEdge cutting edge was still sharp, and the untreated side was dulled and worn away.
Results will vary based on grass type, soil type and condition, and geographical region.
Cutting Costs, Boosting Bottom Lines
Increased Fuel Efficiency
Dull blades produce resistance, putting strain on the mower deck and making it difficult to maintain speed and efficiency. Mowing with a dull blade can reduce fuel economy by as much as 22 percent, which increases operating costs and reduces productivity.
Healthier, Greener Lawns
A dull blade shreds and tears grass, leaving it vulnerable to dehydration, browning, and disease. LaserEdge® blades cut grass cleanly, making it easier to deliver high-quality lawn care and in-demand enhancements such as lawn striping.
Blades Stay Sharp Longer
In abrasive conditions, a blade can get dull in as little as four hours, and lawn-care operations can go through dozens of blades a week, resulting in downtime and lost revenue. No matter the environment, a LaserEdge blade “cuts itself sharp,” reducing time spent sharpening.
Less Mower Maintenance
Blade replacement can be a dangerous undertaking. Attacking a dulled edge with a makeshift sharpening tool can irreversibly damage a blade and put workers in danger. LaserEdge blades dramatically reduce the frequency and risk of blade sharpening.
D.H. Steinegger, R.C. Shearman, T.P. Riordan and E.J. Kinbacher, “Mower Blade Sharpness Effects on Turf,” in Agronomy Journal 75 (1983): 479–480.
Savings Calculator
See how much you can save with LaserEdge® Eversharp™ lawnmower blades.
- 432 Saved on Fuel Cost
- 1575 Saved on Blade Sharpenings
- 2625 Additional Revenue Opportunity
- ( 960 ) Premium Spent on LaserEdge Blades
Calculations above are based off the following: type of lawn mower: 3-blade, 60-inch cut, gas-powered. Average gas price: 2.38. Lawn mower blade pricing: standard blade is 16. Average cost of sharpening: 5 per blade. Fuel savings: 11%. Blade removal and re-installation time: 30 minutes.
Frequently Asked Questions
How does LaserEdge ® Eversharp™ maintain a cutting edge that “cuts itself sharp”?
The LaserEdge Eversharp technology is applied to the underside of the cutting edge. As the blade cuts grass, the original blade material begins to wear away and exposes a new LaserEdge cutting edge, which is even sharper than the blade’s original sharpness.
Will I need to sharpen my LaserEdge ® Eversharp™ lawnmower blades?
LaserEdge blades “cut themselves sharp” and require minimal sharpening, but you should monitor cutting-edge wear. Sharpening is only needed if the new LaserEdge cutting edge is not presenting itself.
If I find the need to sharpen my LaserEdge ® Eversharp™ mower blades, how do I do so?
If you choose to re-sharpen your LaserEdge blade, do so in a safe, controlled setting with the proper equipment. Remember to prep the machine and remove the spark plug before removing the blade. Secure the blade to a work surface with a vise or clamp, and sharpen the blade with a file, bench grinder, or professional blade grinder. Ensure the blade is evenly sharpened and balanced before remounting on the mower deck.
How often will I need to change my LaserEdge Eversharp™ lawnmower blades?
The LaserEdge blade is designed to “cut itself sharp” and requires minimal sharpening over its life. The overall life of the blade will vary due to conditions, but its lifespan should be at least as long as a standard blade’s. In several of our tests, we found LaserEdge blades had longer lives.
How do LaserEdge ® Eversharp™ lawn mower blades perform in abusive mowing conditions?
The LaserEdge technology is an extremely hard, wear-resistant material. If you mow in conditions that regularly include rocks, curbs, out-cropping stones, and other hard objects, LaserEdge lawn mower blades may not be suitable for your operation.
A good test to see if LaserEdge is right for your operation is to inspect your worn blades. Worn blades that show excessive gouging, deep gashes, or large scraps may not see all the benefits of LaserEdge.
How long will it take for LaserEdge ® Eversharp™ to take effect?
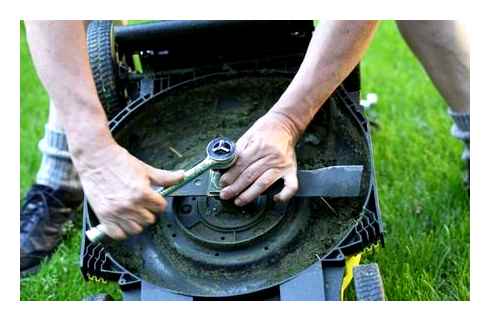
This is highly dependent on geography, soil type, and cutting conditions. The magic of LaserEdge happens when the base blade material wears away at a faster rate than the harder, more wear-resistant LaserEdge material. In highly abrasive soil conditions (like sand), we have experienced standard blades wearing out in as few as 50 hours with blade sharpenings occurring as frequently as every 4 to 8 hours. In these areas, LaserEdge began exhibiting self-sharpening in as little as 5 to 10 hours. When using LaserEdge, these blades required no sharpening over the entire life of the blade. In less abrasive conditions, LaserEdge technology will take effect but over a longer time period.
How much do LaserEdge ® Eversharp™ lawn mower blades cost?
The price of LaserEdge blades will vary depending on the OEM and blade configuration. Although the LaserEdge will typically be more expensive than a standard blade, the benefits of consistently having a sharp cutting edge and increased uptime surpass the increase in blade price (see Savings Calculator).
Where can I purchase LaserEdge ® Eversharp™ lawnmower blades?
Most lawn mower Original Equipment Manufacturers (OEMs) are currently in the process of adding LaserEdge to their product line-ups. Be sure to talk to your local dealer about LaserEdge.
How do I get more information on LaserEdge ® Eversharp™ blades?
Fill out the contact form at the bottom of this page, and Fisher Barton will email you updates on product availability and news.
Get LaserEdge® For Your Business
Ready to bring this cost-effective, state-of-the-art mower blade technology to your lawn-care business? LaserEdge blades are currently available through select OEMs.
Available for the following brands through their independent dealers: (Click on the logo for information on available part numbers)
Connect With An Expert
We’re here to help and would love the opportunity to discuss your technical questions or application challenges.
Which Side Of The Lawn Mower Blade Is Up? (2023 Guide)
Owning a lawn mower is a great way to save some money and maintain more control over your lawn and yard. But, it can come with some unexpected maintenance, and it’s alright if you don’t already know how to keep your lawn mower in good condition.
If you want to keep your lawn mower working well, you need to know how to install your lawn mower’s blade.
Don’t worry if you’ve looked at lawn mower blades and been completely baffled by them before.
I wrote this guide because I’ve been there, and I know how important proper blade installation can be. After all, getting the installation right is critical for the life of the blade, the function of the lawn mower, and the appearance of your lawn.
In this guide you’ll learn:
- Why lawn mower blade direction matters
- How to tell which side of your lawn mower’s blade is up
- And much more!
Why Does It Matter Which Side Of Your Lawn Mower Blade Is Up?
If you’re in a hurry, this video will help explain why it matters which side of your lawn mower’s blade is up, why it matters, and how to install the blade.
Use the Cutting Edge
Most walk-behind lawn mowers rotate the blade to the right, or clockwise. That means that when the blade is spinning, the cutting edge should spin to the right. However, this isn’t 100% foolproof.
Some lawn mowers do spin counterclockwise. It’s rarer, but you have to know which direction your lawn mower spins to be sure. Your lawn mower’s user’s manual should be able to tell you which direction the blades spin.
The Wings Face Up
On most lawn mower blades there will be a small part of the blade that isn’t flat, but angled up. This little wing on the blade is designed to encourage air movement, helping pull your grass upward for an even cut.
The wings on lawn mower blades are always designed to point up toward the lawn mower’s cutting deck. The same is true for the more extensive wings on mulching blades. If your lawn mower blade has wings, those wings should point toward the lawn mower and away from the grass.
Those three techniques should help you figure out which side of the lawn mower blade is up on pretty much any lawn mower blade. Assuming you know which direction your lawn mower spins the blade, that is the most fool-proof method, but the other two options are usually easier and faster ways to tell.
How To Tell What Kind Of Lawn Mower Blade You Need?
There are two basic kinds of lawn mower blade to choose between, and getting the right one can make a significant impact on your lawn mower’s performance. Most lawn mowers are compatible with both types of blade.
It’s important to remember that not all blades are created equal, and just because a blade is the right length doesn’t mean it’s compatible with your lawn mower. You always need to check your lawn mower for which blades are compatible.
Regular Lawn Mower Blades
Regular lawn mower blades are the simplest option. They are blades that are designed to get the job done without any bells and whistles or extra functions. These blades leave clippings relatively long, but they can also provide a more even mow than more complicated blades.
It’s important to have a good cutting edge on these blades since they are really reliant on cutting power to get good results.
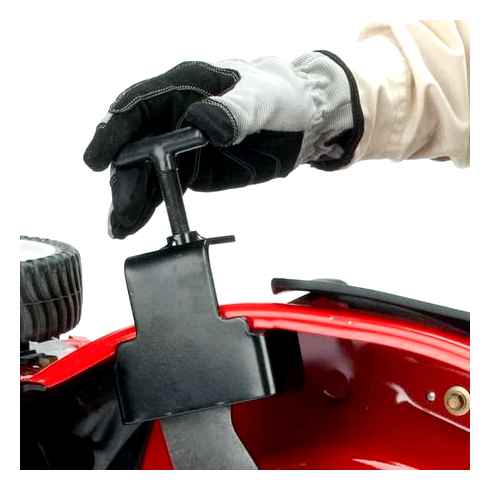
Also called standard or medium-lift blades, these blades are typically on lawn mowers with side-discharge designs.
High Lift Blades
High lift blades are generally used for lawn mowers that have a bagging function because they provide more airflow that helps to move the grass clippings into the bag. These blades also provide higher suction, which means that they cut the grass at a more consistent height by pulling the grass up straighter.
Mulching Blades and Gator Blades
Mulching blades and gator blades both provide even more suction and cutting power in order to process the grass into smaller pieces. Of the two blade types, mulching blades are gentler. They process clippings into smaller chunks to distribute back over your lawn to act as a protective layer over the top soil.
However, mulching blades are not typically a good idea if you’re trying to bag your grass clippings at the same time. They just don’t move the clippings toward the bag very effectively.

Gator blades process the grass clippings even smaller than mulching blades. They are designed to get the clippings small enough to eventually mix into the top soil of your lawn where they will decompose and replenish the soil.
My Final Thoughts On Which Side Of The Lawn Mower Blade Is Up
Knowing which side of your lawn mower is up might seem like a simple thing, but it’s incredibly important. Choosing the right side of your lawn mower blade will help maintain the health of your lawn and can even reduce the maintenance on your lawn mower itself.
Learning how to install your lawn mower’s blade properly shouldn’t be difficult, but it is an important step if you want to keep your lawn mower in good condition. Hopefully this guide will help you decide which kind of blade is right for your lawn, and learn how to install it successfully.