What can replace the battery for an electric screwdriver
Troubleshooting
Due to the fact that the power supply is a chain of series-connected elements, you need to determine which specific participant is out of order to perform its replacement to restore the battery performance of an electric screwdriver. As one inoperative link de-energizes the entire chain.
For this purpose, the following algorithm applies:
- The battery is placed in the charger until the charging signal is received.
- The battery pack is disassembled.
- The voltage of each bank is measured with a voltmeter.
- Marks are placed on all cells that are below the normal operating rating. For example, the nickel-cadmium ones give out 1.1 or 1.0 volt instead of the 1.2 volt.
- Then the device is assembled and turned on until the engine power is noticeably decreased.
- After that all the cells are disassembled again and the voltage is measured.
Banks, the loss of which has a rating of 0.4 volts or more compared to normal, are not suitable for further operation and require replacement.
Replacing the cells in the screwdriver battery with your own hands
Hello! Here is a review with step-by-step instructions for replacing the cells in the screwdriver battery. In the review a little text, a little more photo material, as well as the answer to the question: “What is the capacity of Chinese batteries at 2500 mA/h?”.
I have such an inexpensive screwdriver Roteri RCD-14.4, which has been in use for several years, but over time the battery charge has become less and less. The search for a suitable battery in the stores led to nothing. So it was decided to order battery cells and replace them myself. Disassembling the battery presented a review of the following:
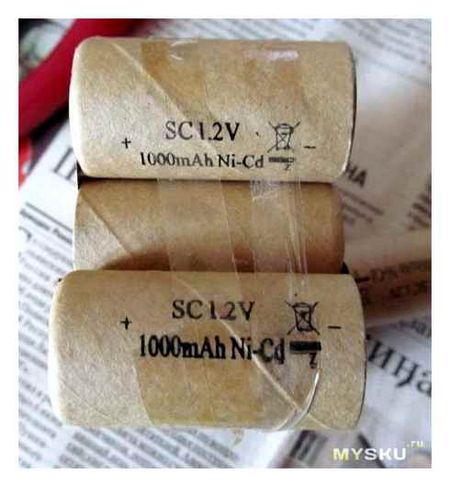
The battery consists of 12 cells SC Ni-Cd. It was decided, ordered, received: To check the performance of all cells, as well as to check the capacity, was used La Crosse RS-700 charger, which I reviewed here. Because of the size of these batteries can not be normally installed in the charger, AA batteries with duct tape on one end were used to ensure contact with the device, and to the reviewed battery cells were soldered wires: The charger itself was switched to TEST mode, and so 3 times, that’s what came out of it: So, out of 12 batteries 3 were defective (real capacity of about 100 mA/h), the rest have a capacity in the range from 900mAh to 1500 mAh, not 2500 mAh. This answers the question posed in the topic. I had to write a complaint to the seller, in response the seller offered to send me 4 similar batteries free of charge. I agreed. The package arrived. This time all 4 batteries turned out to be functional with similar capacity to the others. Proceed to the replacement of the cells: For tinning the paddles used flux LTI-120, an ordinary rosin is not tinned. It is better to solder on the “minus” side of the battery, t.к. the battery case is the “minus” and if there is a break in the insulation at the soldering point, it will lead to nothing. Finally the entire battery was taped tightly together and installed in the case: A test of the screwdriver showed that 600 was not wasted!
And yes, please don’t be stingy when clicking on “liked this review”.к. This is an incentive to write more reviews 🙂
How to replace the batteries of an electric screwdriver
As you know, any battery sooner or later will use up its life and needs either a partial replacement of batteries, or it should be replaced completely. When it comes to an electric screwdriver, for some it may be much easier to buy a new one than to replace the batteries in it, because it requires both time and a certain skill. However, with skill, replacing the batteries in an electric screwdriver can be a good alternative to buying a new one. In many cases, it is less expensive.
Screwdrivers usually use nickel-cadmium or lithium-ion cells as batteries. Nickel cadmium batteries are more undemanding and if you replace some of the cells in such a unit, it will work for a long time. Partial replacement of lithium batteries can also be done, but it is a bit more difficult. Keep in mind that not only will you have to solder the cells themselves, but also the balancing board. Also in recent years electronics enthusiasts often change the batteries of an electric screwdriver with their own hands, from nicd batteries to lithium batteries. It is a good way out if the screwdriver has to work often and intensively. Li-ion batteries have much higher capacity and more cycles.
How to replace dead batteries in an electric screwdriver
Battery life is much shorter than the life of an electric screwdriver and battery charger. New batteries are expensive and sometimes impossible to buy. But the battery consists of several cells, and they do not fail at the same time. It is usually impossible to work with an electric screwdriver when more than one battery is defective. Battery will not charge to rated voltage, will not hold the load, current output will drop sharply, etc.д. The failed cells can be replaced and the body and the healthy cells can be used. You can extend the life of an electric screwdriver by replacing the batteries yourself.
What types of batteries can be tinned
If we talk about the possibility of soldering leads, it can be connected in this way any elements, you only need to use the right flux. All batteries do not like overheating, so special measures must be taken to avoid this.
Lithium-ion battery packs stand out because they are extremely sensitive to temperature rise. And it’s not just about potential chemical deterioration. Li-Ion cells contain additional devices inside the case that increase the safety of operation. For example, a valve that opens when the pressure inside the jar increases. These devices are made mostly of plastic and overheating almost always puts them out of order. Therefore it becomes dangerous to exploit such banks and soldering can be used only as a last resort and very carefully.
On sale there are 18650 cells with already installed bars, which are well tinable even with ordinary flux. Such cells can be soldered, but even in this case it is necessary to be careful.
To begin with, you have to wonder if I need this conversion? After all, it would be a blatant “homemade” and in some cases can lead to failure of both the battery and the screwdriver itself. So, let’s look at the pros and cons of this procedure. It is possible that after this some of you might decide to give up on converting a Ni─Cd battery for your screwdriver to lithium cells.
The “pro” arguments
- The energy density of lithium─ion cells is much higher than the nickel─cadmium cells that are used by default in electric screwdrivers. That is, a lithium can battery will have less weight than a cadmium battery for the same capacity and output voltage;
- Charging of lithium battery cells is much faster than in the case of Ni─Cd. It takes about an hour to charge them safely;
- Lithium─ion batteries have no “memory effect. This means that they do not have to be fully discharged before they can be recharged.
The arguments against
- Lithium battery cells should not be charged above 4.2 volts and discharged below 2.7 volts. In real life, this range is even narrower. If these limits are exceeded, the battery can be destroyed. Therefore, in addition to the lithium cells themselves you need to connect and install a charge-discharge controller in the screwdriver;
- The voltage of one Li─Ion cell is 3.6─3.7 volts, and for Ni─Cd and Ni─MH it is 1.2 volts. So, there are problems with assembling a 12 volt battery for screwdrivers. Three lithium batteries in series can make a battery with a rating of 11.1 volts. Of four ─ 14.8, of five ─ 18.5 volts and so on. Naturally, the charge-discharge voltage limits will also be different. That means that there can be problems with the compatibility of the converted battery with the screwdriver;
- In most cases, as lithium cells for converting use cans standard 18650. In size they are different from Ni─Cd and Ni─MH cans. In addition, you will need space for the charge-discharge controller and wiring. All of this will need to fit into a standard screwdriver battery pack. Otherwise it will be very inconvenient to work with;
- The cadmium battery charger may not be able to charge the battery after it has been converted. You may need to modify the charger or use universal chargers;
- Lithium batteries become unusable at sub-zero temperatures. This is critical for those who use the screwdriver outdoors;
- Lithium batteries are more expensive than cadmium batteries.
USB & Li-ion Upgrading dead Black & Decker Screwdriver. 892
Converting an electric screwdriver to 12v lithium batteries
What we have: an old electric screwdriver Interskol Da-12ER-02 quite cheerfully working, but with dead batteries.
Our goal: replace old Ni-Cd batteries with new li-ion ones
To redo the conversion according to my variant, we will need:
- – Electric screwdriver Interskol Da-12ER-02))
- – 60W soldering iron.к. you can’t solder with a less powerful soldering iron
- – multimeter (tester)
- – “soldering acid. there are many variations, we take with a brush
Battery:
- 18650 lithium batteries, for example take batteries already with tails. Batteries we need high amperage read.
- protection board with balancer 3S 40A 12.6V 40A lithium battery protection board
- Wires are short, but thick cross-section of 1.5
- double-sided adhesive tape
- thick wide relatively soft gasket 1.5. 2 cm
Charger (may not be remodeled):
- – DC-DC converter (XL4015). Article about these converters read
- – breadboard, for example. We need a thick board.
- – 4 diodes from 100v 3A or a ready made diode bridge, I used to look. Or it will be taken from the original charge board.
- – capacitor from 470μf 35V. Or it can be taken from the original charger board.
- – two LEDs of different colors 5 mm.
- – thermal adhesive
- – wires of different lengths and cross sections.
- – 2 mm drill bits
Precautions:
- – when working with batteries, you must be extremely careful not to let them short-circuit, at the moment of contact, huge currents occur at the point of contact, which can lead to burns, eye damage, explosions and fires. And if all the components are out of order.
- – When working with acid, you must be extremely careful t.к. it can get into the eyes, on the skin, etc.д. the consequences can be very sad.
- – Work only with equipment disconnected from 220 V mains. You must also take into account that power circuits use capacitors which accumulate charge and when you unplug the device, it does not mean that the board is de-energized.
Let’s go:
If you don’t have something from the list above, it’s better not to start working on it.к. You’ll cause more hassle than you’ll get work done.
Foreword
You can also use 6pc. 18650, which will double our battery capacity, but require a higher charging current, which would require abandoning the native power supply without modifications, and our charging will last oooooooooooooo long.
I want to draw your attention and this is very important, the batteries in the photo are not suitable for our task, it’s my fault, I bought it without thinking. Use only high amperage batteries. But t.к. I didn’t have any options, I’ve been making.
Why do we need high amperage batteries. Lithium batteries are designed to use under certain conditions of charge-discharge, the ones in the photo allow them to cut currents of 2C i.e.е. in this case it’s about 6A.An electric screwdriver draws 15A to 25A at startup and about 10A at constant load. As we can see we have exceeded the manufacturer’s requirements. High-amperage batteries are designed for higher discharge currents starting from 10A, which guarantees us a longer life and less surprises in the future from improper use. Read about these batteries
Board with protection and balancing. will allow us to operate the lithium batteries within the limits that the manufacturers recommend. It will protect our batteries from deep discharge, as well as overcharge, which is very critical for lithium batteries and violations of this point will lead to very rapid degradation of the battery t.е. loss of capacity. This board also has a balancing circuit that is designed to equalize the charge on each battery cell. Our batteries are connected in series, which in operation will cause them to charge unevenly read.п.1, but this board will eliminate this effect. Presented board, upgraded at the request of the workers and self-balancing when the protection is triggered.
Assembly:
We use batteries with the tails already welded on. The first thing we do is to remove the shielding from the tails, then we need to tin the ends. Tin without using acid (carefully) you can not get so take the acid, soldering iron and solder and tin. Solder at both ends. Apply a thin layer of acid, it is enough otherwise you will get splashes in different directions.
If you bought acid without a brush, you can pour it into a tube of nail polish or you can use a disposable syringe, where you squeeze a drop and immediately draw it back, leaving a thin film. We need to tin the plus sides of the first two batteries, in these places we will connect the batteries together.
After tinning everything, solder the batteries in a row and solder them together.picture. On one of the batteries the tab is reversed. Soldering is also done with a strong soldering iron, just put the tongue and press the tip of the soldering iron. This is what we should have.
Now we fix the ends with duct tape or it can be done before soldering. We glue a double sided adhesive tape to fix the board.
We disassemble the original battery. Remove the old batteries (Careful).
Bite off the black thing and solder. We need thicker wires.к. We will have currents up to 25A and more. That with thin wires can cause them to ignite, and we will have a loss of power. Batteries are carefully put aside.
Now we need to find a thick, wide relatively soft gasket 1.5- 2cm. I ripped it off the packaging of a gadget. We cut it to the size of the case and put it on the bottom, double sided tape and glue the batteries. Fix the black thing, the protruding end should be long enough to fit into our batteries to close the case with some tension. Don’t mix up the polarities!
In this case, the brown wire is minus and the black one is plus. The brown one is a lot thicker than the black one.
We cut the wires as short as possible not to lose current on losses, but we must take into account that we have to solder the device to the board. Solder and assemble the case and the battery is done.
Use a ready made battery with the existing charger but:
- – there are complaints that the case will be very warm which many are afraid of. But it uses a transformer in the charger and heating is normal for it. In my experiments with 1A it heats up to 60C. There is no system of current limitation in the design, so that the current in the system can be many times higher and the heat is higher. At the same time now we need more time to charge the batteries.
- – the charger is designed with a system to limit the charging time to one hour. Т.е. we have to recharge the battery to fully charge it.
- – it will be hard to use a native charger if we decide to use 6 18650 cells t.к. The maximum current delivered according to the manufacturer’s statement should be 1.8А. Т.е. Long use with currents higher than that can lead to unknown consequences. For 3 cells of 3000 mAh and the recommended charging current from 0,5C.1С (1.5A. 3A) we are within the parameters of the charger. For 6 cells we need double the charging current. And yes, as I said before, the charger has no current limiting circuit t.е. in a certain period of time we will charge our batteries at the limit of the charger’s capability, which is tolerable for 3 cells but not for 6 cells.
Basically these are the main nuances of using a native charger.
About the native charger.
At idle speed the charger gives us 19-20V and short circuit current not measured. Manufacturer claims a operating current of 1.8A.
SD-C804S charger schematic found on the Internet.
The circuit has, in my opinion, a number of incorrect notations, but not the point. There are no nodes in the circuit to monitor and limit the charging current. But there is a circuit for tracking the voltage performance on the chip U1 (not a fact, to confirm the performance of this node has not turned out), as well as a node to limit the time of the charge is made on the chip U2.
What prevents us: what prevents us is the charging time limitation circuit, but it can simply be disabled, otherwise it’s kind of fine. But, I could not get the charger to show the end of charge. Turned on the native battery to charge, the charge indicator light came on, but by breaking the circuit on the battery i.e.е. we got the power voltage at the output, the indicator never went out, and should have, if the end of the charge is regulated by the battery voltage (I am not a specialist in electronics and to understand how it works completely can not). And for us this is a critical point t.к. The protection board of our molded batteries at the end of the charge just breaks the circuit.
There was a lot of thought on how to make the charging. From upgrading the current circuit, with automatic selection of which battery is inserted the old or new one on simple elements, to front-end all on Arduino with control of everything and everything. But all this takes a lot of time and effort It was decided not to re-invent the wheel and go the way of all.
I use a DC-DC converter with charge current control on XL4015 chip
Rebuild native battery charger (horrible kolhoz):
We will remake it in order to be able to charge the old type of batteries.
Let’s take our Chinese board and connect it to the lab PSU and set the voltage to 19v, or let’s disassemble the battery charger and connect the outputs to the diodes.
We rotate the voltage trimmer and set the voltage at the output 15v t.к. Genuine Ni-Cd batteries have a full charge voltage of 1.4v-1.5V, and we have 10. For new battery pack it doesn’t matter, it’s more than 12V.6в.
UPD: The protection board with the balancer disconnects the batteries itself if the battery voltage exceeds 12.6V, so 15V is not important for us. It is important for us when charging the old batteries t.к. There is no protection board.
Switching the multimeter to current measurement mode. Turn the current adjusting resistor counterclockwise (I think in this direction) up to the end t.е. set minimum output current. Let’s connect the multimeter’s ends to the output, close the circuit, and set the current of 1A. The bigger current will charge our battery faster but the heat will be bigger. Do not set it above 1A.5A to be on the safe side. This completes the board setup.
Take apart our charger. To install the new board we will need to unsolder the original board, remove everything but the two LEDs, diode bridge, and the smoothing capacitor, as well as the battery connector itself. This is because we can not plug in a new board.к. The board is in the way. I decided to leave the original board intact and make a kolhoz.
We take the breadboard, diode bridge, capacitor, two LEDs or solder it all from the original board. We also unsolder the connectors.
Next, we need to assemble on a breadboard. Fig. (as best I can) what is circled with a black line.
And solder our LEDs as in the figure. The brown one is negative and the orange one is positive (what kind of wires we have). To keep the wires from breaking off at the solder point, we put hot melt glue on them. We solder everything according to the schematic. Do not mix up the polarity of the capacitor and all connections. LEDs in the housing attached to the hot melt glue.
As a result we have a kinky little thing like this.
Now all check, assemble and use. I have protection with this board does not work by pressing, but my hand may be able to make it work. The charge lamp will turn off when the charging current is less than 10% of the set current.е. less than 0.1А
Appendix from 15.09.20:
I don’t use the screwdriver very often, and I’ve worked on it three times. So today I put the battery pack on charge and after a couple of hours I heard a pop. Having opened the frame I found leakage of one of the banks, all batteries were depleted to zero and when you try to charge them from an external source, they do not take a charge. BMC board has no external damage and short circuits in the main points.
I did not understand what happened, and I have no desire to find out. Order myself a new screwdriver Interskol DA-10/14.4Л3, 1.5Ah [383.0.2.00]
As an option, I think, in the future BMC boards take not from obscure Chinese, but to take clones of BMC from real existing shurek.
The meaning and order of converting screwdrivers to lithium batteries
Why are Ni-Cd batteries failing fast?? In a daisy-chain of series-connected cans, each one is different. The chemical process is individual, the charge is different in closed systems. If one bank malfunctions, the design does not give the correct voltage. There is no charge control or balancing system in the individual components.
- Each Ni-Cd can gives 1.2 V, and li-ion 18650 gives 3.6 V.
- The capacity of a lithium battery is twice as big as a nickel cadmium battery of the same size.
- Overheated li-ion battery threatens an explosion and combustion, so setting the control of charge evenness in the banks is mandatory. The nickel-cadmium batteries do not have BMS, because the manufacturer is not interested.
- Lithium cells have no memory effect, unlike Ni-Cd, you can charge them at any time and within an hour.
- An electric screwdriver becomes much lighter after the battery is converted to li-ion, using 18650 batteries.
there are only two obstacles for converting your electric screwdriver to lithium batteries. it is impossible to work with it in minus temperatures. The capacity of the battery drops starting from as low as 10 0 C. Lithium batteries are expensive.
Knowing what input voltage an electric screwdriver requires, the charger is redesigned, taking into account the placement of the lithium battery cans and control cells in the factory container. You can also do the same with a flashlight by modifying the socket for a 18650 cell block.
Suppose you need to convert a 12 V electric screwdriver that uses Ni-Cd cans to li-ion. If you use 3 banks, the output voltage is insufficient: 3.6 x 3 = 10, 8 V. With 4 components, the power of the unit will be higher: 3.6 x 4 = 14.4 V. The tool will become lighter by 182 g, slightly increasing its power, capacity. all the same pluses. But it is necessary to leave the terminals and the native temperature sensor.
How to convert a cordless electric screwdriver to a lithium battery
When all the necessary materials and tools are prepared, you can figure out how to convert the electric screwdriver to lithium-ion batteries. The instructions for converting an electric screwdriver battery to lithium are as follows:
- First you need to disassemble the plastic housing of the original battery. Typically, screwdrivers, if equipped with a nickel-cadmium battery, there are 2 of them in the set. When the first one fails, it means to use it as a donor, from which an upgraded version of the power supply is made
- To disassemble the power supply you need to unscrew 3, 4 or 6 fasteners. Inside the case you will find the appropriate number of nickel-cadmium batteries (10 pieces or more)
- All the banks are connected in series, resulting in a total voltage. At this point you can pause and think about the fact that it is much easier to find a failed nickel-cadmium bank and replace it. To repair the cadmium battery you can buy a rechargeable Ni-Cd battery bank for an electric screwdriver in Cylinder, and solder it instead of the one which has a reduced voltage (does not hold the charge)
- Our main goal is not just to repair an old cadmium battery, but to replace the jars in it with a lithium source. To do this we remove all the jars by biting through the contacts
- Only the connector with plus and minus terminals, as well as the temperature sensor should remain on the case
- Thermo-sensor is not removed, because if you unsolder it, then when you connect the upgraded battery to the charger unit, it will not turn on (will not charge)
- If you are not good at electronics, you will need a controller, because its main purpose is to protect elements from overheating
- When the battery case of an electric screwdriver is ready to accept new lithium batteries, they need to be soldered together in series. For soldering a wire with a cross section of at least 2.5 kV is used. mm. If you use a wire with smaller cross section, the passing of large currents will reduce the power of the device
- Solder the lithium jars quickly so they do not heat up, or use spot welding. To quickly solder the wire to the bank, you need a powerful soldering iron with a power greater than 60 W
- The controller must be soldered to the banks connected in series. The connection diagram is shown in the photo
- Even if you are not familiar with electronics, according to the diagram in the photo above, it is not very difficult to solder the appropriate wires
- Now the resulting structure with soldered terminals should be placed inside the housing
- After the battery of an electric screwdriver is remodeled, you need to assemble it, and perform a test run on the tool. If the electric screwdriver works with an upgraded battery, the unit will charge it
This is interesting! If you want, you can install a digital voltmeter in the battery case, which will show the voltage value. Just immediately do not forget to install the switch to be able to turn off the voltage meter, otherwise it will constantly show the value and at the same time discharging the battery.
There are almost no difficulties in the process of implementing the work, if all the component parts are chosen correctly. Now, if you are going to modernize a portable power tool (and not only a screwdriver, but also a portable angle drill, angle grinder), then with the presence of instructions how to remake the battery of an electric screwdriver, it will not be very difficult to implement the process yourself at home.
After assembling the homemade device, it can be installed in the tool and to test the quality of operation. However, soon it will be necessary to charge the converted battery, so let’s figure out how to do it.