Metal chopping and cutting Locksmithing
.3 Cutting metals
Chopping is an operation in which layers of metal are removed from the workpiece or the workpiece is chopped using a chisel and metal hammer.
Cutting is physically based on the action of a wedge shaped like the working (cutting) part of the chisel. Cutting is used when machining is difficult or not rational.
Cutting is used to remove (chipping) from the workpiece metal irregularities, removal of hard encrustation, scale, sharp edges of the part, cutting grooves and grooves, cutting sheet metal into pieces.
Cutting is usually done in a vice. Cutting sheet material into pieces can be performed on a plate.
Chisel is the basic working (cutting) tool for chopping, and hammer is the percussive tool.
The locksmith’s chisel (figure 8) is made from carbon steel tool steel U7A or U8A. It consists of three parts: impact, middle and work. Impact part 1 the working (cutting) part of the locksmith’s chisel is tapered to the top, and its apex (flank) is rounded; for the middle part 2 the chisel is held during cutting; the working (cutting) part 3 is wedge-shaped.
The angle of sharpening is chosen according to the hardness of the material to be worked. The following cutting angles are recommended for the most common materials:
Kreitzmeissel. chisel with a narrow cutting edge (figure 10), designed for cutting out narrow grooves, small precision keyways and for cutting off rivet heads. this chisel can also be used for cutting wide layers of metal: first, a narrow chisel cuts a groove, and the remaining protrusions are cut with a wide chisel.
Locksmith hammers, woodcutters used to cut down metal are of two types: with round and s with a square with the striker. The weight of the hammer is the main characteristic of the.
Hammers with a round hammer head are numbered1 through 6. Nominal weight of hammer 200 g; 400 g; 500 g; 600 g; 800 g; 1000 g. Hammers with a square hammer have numbers from 1 to 8 and weigh from 50 to 1,000 g.
Material of the hammers is steel 50 (not lower) or steel U7.
Working ends of hammers are thermal treated with hardness HRC 49-56 on the length equal to 1/5 of the hammer length on both ends.
Hammers with round hammer and 3, with square hammer and 5 are used for on-site locksmith works. Hammer handle length. around 300-350 mm.
Metal hammering: definition, purpose, technology of performance with detailed operational description
CHANNING is a locksmith operation during which a layer of metal is removed from the work surface or workpiece or metal is chopped into parts with the help of cutting and percussion tools.
Cutting is one of the rough machining operations with an accuracy of approx. 0.5 to 1 mm.
Tools for cutting
CANAVER
KREUTZMESSEL
HAMMER
CHANNING PRACTICES
Before you begin, set the vise height, fasten it securely, and assume the correct position. The workpiece should protrude by 3-5cm
CUTTING TECHNOLOGY
Laboratory work 2. Preparatory operations (marking, cutting and cutting of metals)
Familiarize yourself with marking, cutting and metal cutting operations.
Practically learn how to mark, cut, and chop (cut) workpieces.
Learn how to make a flow chart for making a part.
The machinist performs preparatory operations when processing workpieces, which come to him in the form of castings of metal, poured into pre-forms, forgings, obtained by forging or stamping, or in the form of pieces of rolled material. sheets, rods, obtained by passing the metal between rotating in equal parts rollers, which have a profile corresponding to the received rolled material, etc.д. Billet dimensions are always greater than the future product. Machining removes a defined layer of metal (a stock allowance) from the surface of the workpiece, thus reducing its size.
To avoid machining errors, a notch is made on the surface of the part. Marking is mainly used in individual and small-batch production. In large-scale and mass production factories, the need for marking is eliminated through the use of special devices such as conductors, stops, etc.д. A line marking is an operation where the workpiece is dimensioned and a line is drawn on the surface of the part to indicate the limits up to which the part is machined. Two marks are often made: one for the machining border and one for inspection. There are planar and spatial markings. Plane markings are used when marking flat parts or individual planes of a part only if it is not required to tie the marked planes together. The methods of plane marking resemble those used in technical drawing. Marking is carried out with tools similar to drafting tools. Because the spatial marking is achieved by connecting individual patterns, positioned in different planes and at different angles to each other, the markings are coordinated. The choice of marking method. by drawing, template, sample, location. is determined by the shape of the workpiece, the required precision and the number of products to be manufactured. With conventional marking methods, the accuracy of marking is 0.25. 0,5 mm, in case of fine marking. in hundredths of millimetre. Marking is carried out on the marking plates. solid, well processed cast iron plates.
Parts destined to be marked out are first prepared for marking, i.e.е. the workpiece is cleaned of dirt, scale and remnants of casting soil, especially carefully in those places where marking marks should be applied. Then the drawing is studied, the workpiece is checked and the bases are selected. Paint the surface to obtain distinctive marks and keep them for a long time. To paint parts, use ordinary dry chalk, chalk diluted in water, copper sulfate solution or red paint. Paint from ordinary dry chalk, which is rubbed on the surface, is fragile. To prepare paint from chalk diluted in water to milk consistency, boil the mixture, add carpenter’s glue and boil it again. Such paint soon deteriorates and gives off an unpleasant smell. To prepare a solution of copper sulfate in water, the following proportion must be observed: per glass of water 2-3 spoons of sulfate. After applying this solution on the surface of the detail remains a thin layer of copper, which is very easy to conduct the risks. To obtain red paint, dissolve shellac in pure alcohol and dye it red with fuchsin. A red, thick and thin layer is formed on the surface, on which the marking marks stand out clearly. The paint is applied with a brush, but it is time consuming, or with a spray gun.
By studying the drawing, the marker finds out the features and dimensions of the part, its purpose in the operation of the mechanism, mentally outlines the marking plan.
Checking the workpiece, the marker determines whether it has no defects, whether its dimensions match the future part and whether there is an allowance for machining. If the billet is cast, the overlaps are cut off, the irregularities are filled, and the remains of molding soil, rust, and scale are removed with metal brushes. Quality of marking largely depends on the choice of bases. lines or surfaces from which the dimensions are set off. The bases are determined according to the specific structural features of the component and the conditions under which it is used in the machine. When marking on a plane, the outer machined edges of the workpiece, the axes of symmetry or the centerlines of the mowing line are taken as bases and are applied in the first instance. At spatial marking as bases accept the processed surfaces, and in their absence. the surface that will not be processed.
In practice, the following order of marking is adopted: firstly, horizontal lines are drawn, then vertical, then oblique and arcs (circles and curves). When drawing straight lines, the scribe is led along the ruler (it is desirable to take rulers with bevels to increase accuracy), tilting it at an angle of 75. 80 to the surface to be marked and in the direction of movement (Fig. 6.))
To separate a piece of metal from a large piece or sheet, for rough machining products to give them the desired geometric shape, to remove burrs or hard crust from the surface of the castings, cutting through various grooves and grooves, cutting cracks in parts for welding apply metal cutting. rough machining operation, which provides an accuracy of machining not exceeding 0.5. 1.0 mm.
As a cutting tool for cutting, a chisel, cross-head, groove tool are used, and a hammer is used as a percussion tool. To use metal cutting tools effectively it is necessary to know basic laws of metal cutting.
The following surfaces are distinguished on a workpiece: machined, finished and cutting surface. The surface from which a layer of metal will be removed (chip) is called the machined surface. The machined surface is the surface from which a layer of metal (chip) has been removed. The cutting surface is a surface formed directly by the cutting edge of the tool on the workpiece. The cutting surface is the transition between the workpiece surface and the machined surface.
The plane of cutting is a plane tangent to the cutting surface and passing through the cutting edge of the tool. The shape of the cutting part (blade) of any metal-cutting tool is a wedge sharpened at certain angles (chisel, cutter), or several wedges (hacksaw blade, tap, tap, cutter, file).
Chisel is the simplest cutting tool, in which the shape of the wedge is particularly pronounced. The sharper the wedge, i.e.е. the smaller the angle formed by its sides, the less force is required to penetrate the material. For different metals there are certain angles of sharpening of cutting tools. Elements and geometric shape of the cutting part of the chisel are shown in Fig. 7.
Presentation “Practical work “Cutting and cutting metal
Please note that, in accordance with Federal Law 73-FZ “On Education in the Russian Federation” in the organizations carrying out educational activities, training and education of students with disabilities is organized together with other students, as well as in separate classes or groups.
“Relevance of establishing school-based reconciliation/mediation services in educational organizations”
Certificate and training discount for each participant
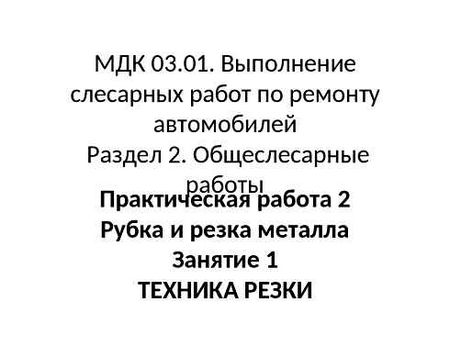
Description of the presentation on the individual slides:
МДК 03.01. Performing locksmith work for car repair Section 2. General fitter’s work Practical work 2 Cutting and cutting of metal Class 1 CUTTING TECHNIQUE
Goals and objectives to know: basic types of locksmith work, the order of their performance, tools and equipment used; safety precautions when performing locksmith work
Task 1. Cutting technique: А. Body and leg position B. Grip of the tool when cutting 2. Features of metal cutting: A. B strips with narrow sides. B workpieces with wide sides B. Cutting along or with deep cuts 3. Procedure for cutting pipe with pipe cutters 4. Procedure for cutting metal of small thicknesses 5. Cutting safety 6. Practical task: making a template to check the chisel sharpness
Cutting sheet metal Cutting sheet metal is held firmly in a bench vice. The distance between the vise and the body of the worker should be about 200 mm. When cutting, the body of the worker’s body should be straight, rotated at a 45° angle to the axial mowing line of the vise. Leaning freely on the left leg, the right leg must be placed in relation to the left at an angle of 60-70° (Fig.). Take the hacksaw with both hands.
Working position: a. body and hacksaw, b, c. With the right hand and the left hand respectively Right hand take the handle and press it to the palm and then clamp the handle with the fingers. The left hand is placed on the other end of the hacksaw. The machine should be pressed with both hands, but the greatest amount of pressure should be exerted with the left hand, and the right hand is used mainly to move the hacksaw. The cutting process consists of two strokes: the work stroke, when the hacksaw moves forward away from the worker, and the idle stroke, when the hacksaw moves backward toward the worker. No pressure is applied to the hacksaw during idle running, which only causes the teeth to glide, and during the working stroke, both hands apply light pressure so that the hacksaw moves in a straight line.
Cutting strip metal Strips with narrow sides (if at least three teeth of the hacksaw blade touch the length of the cut) must be cut on the narrow side, because in this case the cutting force is distributed over a smaller area, and therefore the cutting process is faster.
Cutting workpieces with wide sides When cutting workpieces with wide sides (Fig.) on their edge at the cutting points a triangular file is notched with a circular saw. Then tilting the hacksaw away from yourself first make a cut, then the slope gradually decreases until the cut reaches the opposite edge. When the slope is no longer tilted, the cut is made horizontally all the way to the end.
Techniques for cutting strips with deep cuts When cutting a strip longitudinally or with deep cuts (Fig.) put the blade in the side slots of the head of the frame, turn it 90° giving a lateral position to the frame. Thin sheets are clamped between two wooden blocks in a vise when cutting.
Pipe cutting with pipe cutters Pipe cutting is also performed with special appliances called pipe cutters (fig.), which give a clean cut. Cutting with pipe cutters is much more productive than with hacksaws. Rotating (rocking) the handle around its axis the cutting roller 3 is brought to the pipe wall until it contacts it under pressure. 1° pipe cutter turns around the pipe and gradually pushes with the crank of the roller to make the cut.
Cutting with scissors Hand scissors are used for straight-line cutting of small thickness metal, one handle of which is clamped in a vice. Hand scissors clamped in a vice (a) and chair scissors. fixed in a vice (b) and lever scissors (c)
Safety when cutting 1) fasten the hacksaw blades firmly and properly because a weakly fastened blade may jump out of the frame, and a tightly tensioned. 2) firmly and reliably fasten in a vise the part to be cut, because if it is not fastened properly, it may fall on the legs of the worker; 3) you cannot work with a hacksaw without a handle or with a cracked handle; 4) at the end of cutting reduce the pressure on the hacksaw and support the cut part so it does not fall on the legs; 5) don’t blow shavings out of the sawed area, as shavings can get into the eyes; 6) systematically remove scraps and blanks near the work place; 7) the work place must be clean, oil-free; 8) the work place must have a box for scraps, convenient for transportation on an electric truck; 9) the material, meant for cutting, must be placed on the side of the cutter.
Practical task: making a template to check chisel sharpening 1. Mark and cut a rectangular blank with metal scissors, size 40×70 mm. 2. Blunt the edges of the workpiece. 3. Mark up a template on the workpiece to check the chisel angles according to the given angles. 4. Carry out cutting according to the markings.
Repeat what you have learned 2. Metal cutting mechanization 3. Draw (mark out) the template in accordance with the dimensions on a sheet of A4 size ½. 4. Have the drawing tools (ruler) on hand. Angle, compass, protractor), blank sheet of A4 format.
MDK 03.01. Doing locksmith work to repair cars Section 2. General Metalwork Practical work 2 Cutting and chopping of metal Class 2 CHECKING TECHNIQUE
Goals and objectives to know: the basic types of locksmith work, the order of their performance, the tools and devices used; safety precautions when performing locksmith and assembly work
Task 1. Cutting technique: A. Body and leg position B. Grasping the tool while chopping B. Blows D. Hammer force E. Choice of hammer weight 2. Order of cutting metal 3. Procedure for cutting blanks from sheet metal 4. Procedure for cutting wide surfaces 5. Safety when cutting 6. Practical task: Grinding tools by hand on the machine
Correct posture of the body and legs Correct posture of the body and grip when sharpening. essential requirements for high-performance work. When chopping metal with a chisel, the position of the body and legs must provide the greatest possible stability to the operator while striking. The chisel position is correct if your body is straight and half-turned (at a 45° angle) to the axis of the vice, and your left leg is half a step forward.
Grasping the tool when chopping The chisel is held in the left hand by the middle chisel edge at a distance of 15° from the foremost. 20 mm from the end of the striking part; the chisel must not be strongly pressed in the hand. Blows are struck with the right hand. As the right hand moves while striking the chisel, the left hand balances the tool in succession. Holding (grasping) the hammer. The hammer is taken by the handle with the right hand at a distance of 15 cm. 30 mm from the tip, wrap four fingers around the handle and press it against the palm of the hand, place the thumb on top of the forefinger. All fingers remain in this position during the swing and strike. This is how the hammer is held in what is known as a wrist strike without the fingers splitting.
hammer blows The hammer swing and strike have a significant influence on the quality and performance of the chopping action. The strike may be wrist, elbow or shoulder strike. With the wrist strike, swing the hammer only by bending the right hand. In this swing, the wrist is bent at the wrist until it is fully bent, with the fingers apart from the thumb and forefinger slightly apart (the little finger should not come off the handle of the hammer in this case). Then the fingers squeeze and strike.strike. The hand strike is used for precision work, light chopping, cutting thin layers of metal, etc. д.
Hammer blows In the elbow strike, the right hand is bent at the elbow. The swing is acted by fingers of the hand, which unclench and contract, the hand (moving it up and then down) and the forearm. Extend the arm quickly enough to obtain a powerful blow. Use this stroke for general chopping, chipping medium-thickness metal, or cutting grooves and slots.
Hammer blows In the shoulder blow, the arm moves in the shoulder, resulting in a large swing and maximum impact force from the shoulder. The shoulder, forearm, and hand are involved in this blow. Use the shoulder strike when removing a thick layer of metal and working on large surfaces.
Impact force The force of the blow must match the nature of the work, as well as the weight of the hammer (the heavier the hammer, the stronger the blow), the length of the handle (the longer it is, the stronger the blow), the length of the working arm (the longer the arm and the higher the swing, the stronger the blow). When chopping, both hands act in concert (synchronously), striking accurately with the right hand while moving the chisel at regular intervals with the left hand.
Correct setting of the chisel when chopping in a vice The setting angle of the chisel when chopping in a vice is adjusted so that the blade is on the chipping line and the longitudinal axis of the chisel bar is at an angle of 30. A smaller angle will cause the chisel to slip, while a larger angle will cause the chisel to be 35° to the workpiece surface and at an angle of. 45°. to the longitudinal axis of the jaws. A smaller angle will cause the chisel to slip, while a larger. at a higher angle it sinks unnecessarily into the metal and the machined surface becomes uneven. The angle of inclination, the chisel when chopping is not measured; an experienced locksmith by skill feels the inclination and adjusts the position of the chisel with the movement of his left hand.
Choice of weight of the hammer Locksmith mass chosen according to the size of the chisel (at the rate of 40 g per 1 mm of the chisel blade width) and the thickness of the removed metal layer (usually the thickness of the chip is 1 kg). 2 mm). When working with a cross cutter weight of the hammer is taken at the rate of 80 g per 1mm of the blade width. When selecting a hammer, the physical strength of the worker is also taken into account. The weight of the hammer should be approximately 400 g for an apprentice and 16 g for a young worker. 17 years. 500 g, for an adult worker. 600. 800г. The impact is not made by excessive muscular effort, leading to rapid fatigue, but by the accelerated fall of the hammer. At the moment of strike the handle of the hammer is firmly pressed with fingers: a weakly held hammer at inaccurate blow may bounce aside, which is very dangerous.
Metal chopping When chopping metal, the chisel is set vertically and the cutting is performed with a shoulder strike. Sheet metal up to 2mm thick is cut with a single blow, so put a pad of soft steel under it. Sheet metal over 2 mm thick or strip material is notched by about half the thickness on both sides, and then broken by bending it alternately to one side and to the other, or chipped.
Cutting out blanks from sheet metal After marking the contour of the part to be made, the workpiece is placed on the plate and the cutting is performed (not along the line of the marking, but at a distance of 2 mm from it). 3 mm. the sawing allowance) in the following sequence: the chisel is set obliquely so that the blade is directed along the marking ridge; the chisel is given a vertical position and light blows with the hammer, notching, along the contour; chop along the contour, applying strong blows to the chisel; when the chisel is repositioned, part of the blade leaves in the cut groove, and the chisel is again moved from the inclined position to the vertical and the next blow is applied; do this continuously until the end (closure) of the marking mark; turn the sheet over and cut through the metal along the clearly marked contour on the opposite side; turn the sheet over again and finish the chopping; if the sheet is relatively thin and cut through enough, the workpiece is knocked out with a hammer.
Cutting blanks from sheet metal
Cutting wide surfaces Cutting wide surfaces is a labor-intensive and low-productive operation used when it is impossible to remove a layer of metal on a planer or milling machine. The work is carried out in three stages. Previously, on the two opposite ends of the workpiece cut some metal, making the chamfer (bevel) at an angle of 30. A roughing planer or milling machine is then used to cut wide surfaces in a 45° pattern, and marks the depth of each operation with a line of crosscutters on the two opposite side faces. Then parallel cuts are made on the wide surface of the workpiece, the distance between them is equal to the width of the cutting edge of the crossbow, and the workpiece is clamped in a vise. Then the cross cutters are used to pre-cut a narrow groove (Fig. 75, a), and then use a chisel to cut off the projections left between the grooves. After cutting off the projections perform the final machining. Such a method (pre-cutting grooves on wide parts) greatly simplifies and speeds up the cutting process. On the workpieces made of cast iron, bronze and other brittle metals, to avoid chipping edges make chamfers at a distance of 0.5 mm from the marking risk.
Safety while chopping During manual metal cutting you must follow the following safety rules: the handle of the manual metalwork hammer must be well fixed and not have cracks; while chiseling with a chisel and cross cutter must use protective glasses; while cutting hard and fragile metal you must use protection: grid, shield; to protect the hands from injury (during uncomfortable work, and during training) protective visor must be put on the hand, and on the chisel. A protective rubber washer.
Manual tool sharpening Before sharpening, set the undercutters as close to the grinding wheel as possible. The clearance between the undercarriage and the sharpening wheel should not be more than 2. 3 mm, so that the tool to be sharpened cannot get between the wheel and the undercarriage. Sharpening is best done with water cooled with 5% soda or on a wet wheel. Failure to do so will cause excessive heat, tempering and loss of hardness, and therefore durability of the tool. Side edges after sharpening must be flat, even in width and with the same degree of inclination.
Check tool angle After sharpening the chisel or cross cutter, deburr the cutting edges. Check the sharpening angle with a template consisting of plates with angled notches of 70°, 60°, 45° and 35°. Hard materials (hard steel, bronze, cast iron) 70º Medium hard materials (steel) 60º Soft materials (brass, copper, titanium alloys) 45º Aluminum alloys 35º
Practical exercise: Sharpening a chisel 1. Set the clearance between undercarriage and grinding wheel on the sharpening machine to 2. 3 mm. 2. Sharpen the chisel at an angle of 60. 3. Check the sharpening angle using a template.
Homework Assignment Repeat the material learned Cutting grooves Bring a drawing tool (ruler. Angle, compasses, protractor), A4 size blank sheet.
http://delta-grup.Note: The cutting technique is very important for cutting.htm http://delta-grup.ru/bibliot/18/161.htm http://www.e-ope.ee/_download/euni_repository/file/3739/1.zip/index.html
Brief description of the document:
The presentation “Practical work “Cutting and cutting metal” is designed for 2 classes.
Class 1. CUTTING TECHNIQUE. Consists of the following sections:
Cutting technique: A. Body and leg position. Б. Tool grip when cutting.
Features metal cutting:A. Strips with narrow sides. Б. blanks with wide sides. В. strips lengthwise or with deep cuts.
How to cut small thicknesses of metal.
Practical task: making a template for checking the chisel sharpening.
Class 2. CHANNEL TECHNIQUE. Consists of the following sections:
Cutting technique: A. Position of the body and legs. Б. Grip the tool when chopping. В. Blows. Г. Force of impact. Д. Choice of hammer weight.
Metal cutting rules and techniques and safety rules
Efficient and clean metal cutting depends on proper machining techniques. When cutting metal, you should stand stable and straight, with half a turn in the vise. It is recommended to hold the hammer on the handle at a distance of 15-20 mm from the end and to strike powerfully in the center of the chisel head. Look at the chisel blade, not the head, otherwise the chisel blade will become crooked. The chisel must be held at a distance of 20-25 mm from the head.
Basic safety rules include:
- The chisel must be carried out wearing safety glasses and on a protective shield.
- Clamp the workpiece firmly in a vise.
- Work with tools that are in good condition.
- Do not stand behind your colleague.
- Reduce the force of the blow at the end of the work.
Chopping and cutting metal
Dressing is a metalwork operation designed to remove distortions in the shape of the workpiece (dents, convexity, waviness, warping, etc.) and to create a smooth surface. п.) by means of plastic deformation. The metal is straightened both when cold and hot. Dressing can be done manually on a steel or cast-iron plate or on an anvil. Straightening is performed using presses and straightening rolls.
They use soft hammers (copper, lead, wood) with a round polished edge (a square edge leaves traces in the form of chips), smoothing boards and supports (metal or wooden bars) for dressing thin sheet and strip metal, straighteners for hardened parts with shaped surfaces.
The curvature of the workpieces is checked by eye based on the gap between the plate and the workpiece placed on it. The curved places are marked with chalk. Straightening of metal bent along the plane is the easiest. In this case, strong blows are made with a hammer or sledgehammer on the most convex areas, reducing the force of the blow as they straighten. The workpiece is periodically rotated from one side to the other. Straightening of metal curved along the edge is more complicated. This involves stretching a part of the workpiece. Metal with twisted (spiral) curves should be straightened using the straightening method. To do this, one end of the workpiece is clamped in a bench vice and the other end in a hand vise. Then the curvature is straightened with a lever. Results of straightening are checked by eye, and a more precise check is carried out on the marking or inspection panel by translucency.
Straightening of plates is a complex operation.
It depends on the type of deformation of the workpiece (convexity or dent in the middle of the sheet, wavy edges, both convex and wavy edges, etc.). п.). The workpiece is first outlined with chalk or pencil wavy areas, then it is placed on the plate convex upwards so that the entire surface of the workpiece lies on the plate. Holding the sheet with your left hand in the glove, with your right hand apply hammer blows from the edge of the sheet towards the convexity (as arrows on 2).5,а). As you get closer to the convexity, the blows should be weaker and more frequent. During straightening, the sheet is rotated horizontally so that the blows are evenly distributed in a circular motion over the entire area of the workpiece. If there are several convexities, the blows are placed between them. As a result, the sheet is stretched and all “convexities” are set into a single one, which is straightened as described above. If the sheet is wavy along the edges but has a flat center, strike from the center toward the edges. Then turn the sheet over and continue straightening in the same way until the required straightness and flatness tolerances are obtained. Dressing of thin plates is performed with wooden hammers, and very thin plates are smoothed with wooden or metal smoothing boards. The sheets are periodically turned over. Quality of straightening is controlled with the help of a ruler.
Dressing ( hardened blanks is performed using different hammers with hardened striker or a special hammer with rounded narrow side of the striker. The blows are applied to the concave side of the workpiece, not the convex. The metal fibers on the concave side are stretched and the workpiece is straightened. Dressing of workpieces of complex shape, e.g. an angle at which the angle between measuring sides has changed after hardening, is performed in the following ways: if the angle is less than 90°, the hammer blows are applied at the top of the inner corner, if more than 90°. at the top of the outer corner.
Straightening is one of the most common locksmith operations. It is used to produce a curved shape of the workpiece at a given contour. In the process
Bending metal is exposed to the simultaneous action of tensile and compressive stresses, so it is necessary to consider the mechanical properties of the metal, its elasticity / degree of deformation, thickness, shape and size of the section of the workpiece, corners and bending radii of the part. The bending radius of the part should not be taken close to the minimum allowable, if it is not dictated by design requirements. It is advisable not to allow bending radius less than the thickness of the workpiece, as it leads to cracks and other defects. In the cold state is recommended to bend parts from sheet steel thickness up to 5 mm, from strip steel. thickness to 7 mm, from a round steel. diameter of 10 mm.
When bending a strip of sheet steel on it first put a risk.bending. Then the workpiece is clamped in a vice between the jaws so that the indexing riser faces the fixed jaw of the vice and protrudes over it by 0,5 mm. Finally, by hammering against the stationary jaw, the end of the strip is bent
For bending staple clamp the workpiece in the vice between the jaws of the jaw and the bar and bend the first end. Then, having put a bar-pressure bar of the desired size inside the bracket, the bracket is clamped in a vise at the level of the ribs and unbent the second leg.
Bending the strip at an acute angle using a special mandrel is shown on 2.7, д.
Bending strip clamp made of thin steel is performed in the following sequence: firstly clamp in a vice required diameter of the mandrel. Then bend the workpiece on a mandrel with two pliers and finish the clamp with a hammer on a mandrel in a vise. Finishing of half-open clamp is performed on the plate.
Machine designs feature assemblies with various directions and forms of bending: a splint or washer in a nut-and-bolt connection; bending of both parts to be connected; one part of the assembly bends into a recess or hole in the other part.
Bending operations are also performed in connection with fitting of various pipes. Copper and brass tubes of small diameter (up to 8mm) are bent manually in cold condition
mm) with large radiuses of curvature (more than 10. 12 diameters). The same tubes of larger diameter (8. 14 mm) is bent by hand using templates or spiral tightly wound springs that are placed inside the pipe at the bend. As a rule, pipes over 20 mm in diameter are spun with special devices or on bending machines, filled with sand or molten rosin beforehand. Copper and brass pipes are annealed in the bend area before bending. Steel pipes up to 10 mm in diameter are bent without heating and without filler, and pipes of larger diameters. in a hot condition and, as a rule, with filler. Aluminium and duralumin pipes are bent in hot condition. Pipes are heated only in the area of the bend at the underbend
length about jgd, where a is the outside angle of the bend;
Cutting is an operation of metal cutting. Using a cutting tool, such as a chisel, cross cutter or groove cutter, they remove the excessive layer of metal from the workpiece, cut it into parts, cut a hole, cut lubrication grooves, etc. п. Chiseling is used when the production conditions do not allow for machining or when high accuracy of machining is not required. Chopping of small workpieces is performed in a vice, large workpieces are chopped on a plate or anvil.
The following tools are used for cutting: chisel, cross cutter, grooving tool.
Metal chisel consists of three parts: working 2, middle 3 and striking (striker) 4 ( 2.10, а). The wedge-shaped cutting edge of the chisel 1 and the bit are hardened and tempered. After heat treatment the hardness of cutting edge reaches HRC356. 61, striker HRC337. 41. The chisel is 100 cm long. 200 mm, width of cutting edge. respectively 5. 25 mm. The angle of sharpening of the chisel, depending on the material to be machined, should be:
Hard materials (cast iron, hard steel, bronze) 70°
Medium hard materials (steel) I. 60°
The smaller the angle of sharpening, the less cutting force is required. However, the harder and more brittle the metal, the stronger must be the cutting edge and the larger the angle of sharpening; The chisel bit has the shape of a truncated cone with a semicircular top base. Therefore, the hammer always strikes in the center of the hammer.
A crossbow differs from a chisel in that it has a narrower cutting edge ( 2.10, б). It is used for cutting of narrow grooves, slots, etc. п. Grinding angles, hardness of the working and impact parts are the same as for the chisel.
Knevoks ( 2.10, c) differ from crucible by curved cutting edge, and are used for cutting out oil grooves in bearing shells and bushings and for other similar jobs.
Before starting work, the chisel is placed on the workbench on the left side of the vice with the cutting edge toward you, and the hammer is placed on the right side of the vice with the striker pointing toward the vice. The correct position of the locksmith’s body is of great importance: the locksmith must stand firmly half-turned to the vice.
Cutting quality and productivity depend on the hammer blow. There are three types of hammer blow: wrist, elbow and shoulder. Only the right hand is bent during the wrist strike. Such impact is used for light and precise work: removal of thin layers of metal, removal of small irregularities, cutting thin sheet steel, etc. п. With the elbow strike, the arm bends at the elbow and the blow is stronger. This blow is used for removal of medium thickness layer of metal, cutting grooves and grooves. In a shoulder strike, the arm moves at the shoulder, with
you get a big swing and maximum impact force. Shoulder thrust is used for cutting thick metal, removing of big allowance in one pass, treatment of large planes. The frequency of hammer blows should be 40 to 60 blows per minute for wrist blows and 30 to 40 for elbow and shoulder blows. When slicing, take the hammer with your right hand by the handle at a standing position for plasthand sheet metal 15. 30 mm from its end so that four fingers wrap around the handle and the thumb rests on the index finger. The chisel is held with the left hand, not squeezing the fingers tightly, at a distance of 20. 30 mm from its head. 26
To protect your hand from the accidental impact of the hammer it is advisable to put a rubber washer 8 mm thick on top of the chisel. 10 mm and a diameter of 45. 50 mm.
When chopping metal, it is important that the axis of the chisel is set correctly in relation to the workpiece surface. The angle between the workpiece (the planes of the vice jaws) and the axis of the chisel must be 45°, the angle of the chisel depends on the angle of the cutting edge and must be 30. 35°. A smaller angle of inclination of the chisel slips and not cuts, while a larger angle causes excessive deepening into the metal, creating a roughness of the machined surface.
When chopping, the chisel arms must operate in coordination with each other. Use your right hand to hit the chisel precisely with the hammer, and use your left hand to move the chisel across the metal. Do not look at the head, but at the cutting edge of the chisel.
When cutting strip and sheet metal at the level of the vice jaws, the part of the workpiece that goes into the chip (to be cut down) must be above the jaws and the risk of marking must be exactly at their level without tilting.
The cutting is done with an elbow strike. When placing the marks above the jaws the angle between the chisel axis and the work surface is periodically reduced
When chopping a metal layer on a wide flat surface the marking marks must protrude over the jaws of the vice by 5. 10 mm. In this case the crosshead first cuts a groove with a width of 8. 10 mm, the width of the gaps between the grooves must be 0,8 of the chisel cutting edge length. Then the chisel chops off the resulting ledge, The thickness of the chip removed by the cross cutter in one stroke is 0.5. 1 mm, and 1.5 mm with a chisel to cut the grooves. 2 mm. Chop cast iron, bronze and other fragile metals without reaching the opposite edge of the workpiece. Undercut places should be chopped from the opposite side or pre-make bevel at an angle of 45 °.
When notching grooves and curved grooves ( 2.14.6) first apply marks on the workpiece’s machined surface, then use a cross cutter to cut a 1.5 m deep groove. 2 mm per pass. The roughnesses left after cutting are removed by the groove cutter, giving the grooves the same width and depth along the entire length of the workpiece.
When hobbing a shaped workpiece on a slab or anvil first make light hammering cuts in the marked contour, leaving the cutting marks 2 mm behind. 3 mm. Grind sheet with firm strokes on chisel. If the sheet is thick enough to be cut on the edge of the workpiece, the edge of the groove is cut into a groove
but thick, it is turned over and chopped from the opposite side along the outlined contour. When notching workpieces with curved contours you must use a chisel with a rounded blade or a cross cutter.
Different methods of metal cutting are shown on 2.15.
Grinding of chisels and cross cutters is performed on sharpening (grinding) machines. For tool sharpening of tool steels (carbon, alloyed electrocorundum with grain size 40, 50 or 63 on ceramic bond. Before starting work, the undercarriage of the sharpening machine is set so that the gap between it and the periphery of the grinding wheel does not exceed 2. 3 mm. Then the protective screen is lowered and the machine is switched on. Set the chisel at an angle of 30. 40° to the periphery of the wheel, and with gentle pressure, slowly move across the full width of the wheel. During operation, it should be periodically rotated from one side to the other to ensure even and symmetrical sharpening. In doing so, the chisel is dipped in water for cooling each time. After sharpening the side edges of the chisel must be flat, of equal width and with the same inclination angles. The angle of sharpening is checked with a template that has corner notches of 70, 60, 45 and 35° ( 2.16, a, b). After sharpening, deburr with fine grit abrasive stone (dress the blade).
Cutting. the operation of cutting into parts of rounds, strips, sections, and pipes by hand and mechanically. Manual cutting of blanks depending on the profile and cross-sectional area is made with different tools: hacksaws, scissors
(manual, chair, lever), pipe cutters and flame torches. It consists of a frame (hacksaw), a movable head, a screw with a nut for tensioning the hacksaw blade and a fixed head with a shank and a handle. Hacksaw frames can be solid or sliding.
Hacksaw blade is a thin and narrow steel plate with teeth on one edge. Each tooth of the hacksaw blade is shaped like a wedge (cutter), which distinguishes the back
angle a, sharpening angle 8, rake angle v and cutting angle b,
A hand hacksaw is the most common tool for cutting thick sheets of strip and section metal, as well as for cutting grooves,
To reduce the friction of the bandsaw blade on the walls of the metal to be cut (kerf), its teeth are bred in different directions, thus increasing the thickness of the blade h to the kerf width. Teeth with a large pitch bend one by one to the right and left, teeth with a small pitch. two or three to the right and two or three to the left; this should form a wavy line.
When cutting metal with a hacksaw, the body of the metalworker must be turned to the right at a 45° angle to the axis of the vice. The position of the legs is shown on 2.17, е.
Before you start cutting metal, choose a hacksaw blade with respect to the hardness, shape and size of the metal to be cut. The degree of tension of the blade in the frame of the hacksaw is checked by lightly pressing the blade sideways with the finger: if it does not sag, the tension is considered sufficient. When working, the end of the handle should rest in the middle of the palm of the right hand and the thumb should lie along the handle from above. Hold the frame of the hacksaw with your left hand so that your thumb is inside the frame and the rest of your thumb covers the tensioning screw of the sliding head. Hold the hacksaw horizontally, move it smoothly without jerking and make 30 to 60 double strokes per minute. When running the hacksaw must run with at least 2/z of its length. When cutting thin material with a hacksaw, clamp it in a vice between two wooden bars and cut together with them. Metal cutting techniques are shown in 2.18.
The cut layer of metal in the form of chips, as you know, may have a different appearance depending on the conditions of processing.
Electric welding and gas cutting of metal. Cutting aluminum, cast iron. To increase productivity in welding, semiautomatic cutting machines are used to cut aluminum, cast iron, and aluminum alloys.
Electric welding and gas cutting of metal. Metal cutting. Basics of metal cutting.Welding of non-ferrous metals and their alloys.
Electric welding and gas cutting of metal. Metal cutting. Basics of metal cutting.Welding of non-ferrous metals and their alloys.
Mechanical cutting is usually used for metal thicknesses up to 10-12 mm, and in some cases up to 25-30 mm.
Electric welding and gas cutting of metal. Cutting aluminum, cast iron. To increase welding productivity semiautomatic.
Locksmith Tip | A Better way to Cut Hard Metal Keys
Electric welding and gas cutting of metal. Metal cutting. Basics of metal cutting.Welding of non-ferrous metals and their alloys.
Electric welding and gas cutting of metal. Metal Cutting. Basics of metal cutting.Welding of non-ferrous metals and their alloys.
Electric welding and gas cutting of metal. Metal cutting. Basics of metal cutting.Welding of base metals and their alloys.
§ 8. Metal cutting. Depending on the shape and size of the material of workpieces or parts, cutting in manual metalworking is done with a handheld or.
METAL CUTTING
Cutting. is a metal-cutting operation in which a cutting tool (chisel, cross cutter or wire cutter) and an impact tool (locksmith’s hammer) are used to remove an excess layer of metal from the surface of a workpiece or to cut the workpiece into pieces. The layer of metal that is removed when machining the workpiece is called allowance.
Metal cutting is used when production conditions make machine processing difficult or not rational. Depending on the quality of incoming parts and the purpose of performed operations, chopping is used for removal of burrs and edges on cast and pressed parts, cutting through grease grooves, cutting down cavities, non-metallic inclusions and other defects of castings. Cutting operation the metal worker has to perform at cutting off metal blanks from rods, strips, sheets, when making pads, cleaning welding seams, removing from the workpiece large irregularities, cutting holes in thin sheet material.
Cutting has an accuracy of 0.5. 1.0 mm. Cutting is considered a roughing operation. This is done while the workpiece is stationary. Cutting is most appropriately performed in a chair vice (see “Cutting in the Vise”). Fig. 1.7), and bulky parts and cutting holes or parts from thin sheet metal. on a plate, anvil.
When carrying out the operation of cutting occurs cutting the metal. By cutting is the process of removing the excess layer of metal from the workpiece in the form of chips, carried out with a cutting tool. The process of cutting occurs during the following operations: chopping, cutting, filing, drilling, scraping, lapping, as well as the mechanical processing of blanks on metal-cutting machines (lathes, mills, planers, etc.).).
Cutting part of any cutting tool is shaped like a wedge. Thanks to the wedge-shaped design the cutting tool penetrates into the material to be machined and cuts the metal.
Consider the work of wedge (Fig. 4.1). Under the influence of force Р (Fig. 4.1, a) normal forces occur on its lateral surfaces N, which separate the metal:
Metal chopping
Chopping is the operation of removing a layer of material from a workpiece, as well as cutting metal (sheet, strip, profile) into pieces with cutting tools (chisel, cruz-meissel or grooving tool with a hammer). Cutting accuracy is not more than 0,7 mm. In modern mechanical engineering the process of metal cutting is resorted to only when the workpiece for one reason or another can not be processed on metal cutting machines. Cutting performs the following works: removal of excess material layers from workpiece surfaces (chipping of castings, welds, cutting through edges for welding, etc.).); chopping of edges and burrs on forged and cast workpieces; cutting of sheet material into pieces; cutting of holes in sheet material; cutting of lubrication grooves, etc.
Cutting is performed in a vice on a plate or on an anvil. Large-sized workpieces for manual chopping clamping in a chair vice. Cutting of castings, welded seams and flashes in large parts is performed on site. Manual hewing is a very hard and labor-consuming operation, that is why it is necessary to maximize its mechanization.
Tools used for cutting
Cutting tools used at cutting refer to cutting tools, they are made of carbon tool steel grades U7, U8, U8A. Hardness of the working part of cutting tools after thermal processing shall be not less HRC 53 56 at length of 30 mm, and hardness of the striking part. HRC 30 35 at length of 15 mm. The size of cutting tools for cutting depends on the nature of the work to be performed and are selected from a standard range of. As an impact tool for chopping use hammers of various sizes and designs. The most frequently used at chopping are locksmith hammers with round beater of various weight.
Locksmith’s chisel (fig. 2.20) consists of three parts: working, middle and impact. As in all machining, the cutting part of the tool is a wedge (fig. 2.20, а).
The action of the wedge-shaped tool on the metal being cut varies depending on the position of the wedge and the direction of the force applied to its base. There are two main ways of operating the wedge when chopping:
The axis of the wedge and the direction of force applied to it are perpendicular to the surface of the workpiece. In this case, the workpiece is chopped into pieces (Fig. 2.20, б);
The axis of the wedge and the direction of the force applied at its base form an angle smaller than 90° with the surface of the workpiece. In this case, chips are removed from the workpiece (fig. 2.20, в).
The planes bounding the cutting part of the tool (cf. Fig. 2.20, c) are called surfaces. The surface along which the chips run off during cutting is called the front surface, and the opposite surface that faces the workpiece surface is called the back surface. Their intersection forms the cutting edge of the tool. The angle between the surfaces that make up the workpiece is called the cutting angle and is indicated by the Greek letter b (beta). The angle between the front and machined surface is called the cutting angle and is designated by the letter 8 (delta). The angle between the cutting surface and a plane through the cutting edge perpendicular to the cutting surface is called the cutting angle and is denoted by the letter y (gamma).
The angle formed by the rear and machined surfaces is called the back angle and is denoted by the letter a (alpha).
The smaller the angle of sharpening of the cutting wedge, the less force should be applied when cutting. But as cutting angle decreases so does the cross-sectional area of the cutting part of the tool, and consequently its strength. In this connection it is necessary to choose the value of the angle of sharpening, taking into account the hardness of the processed material, which determines the cutting force required to separate the metal layer from the surface of the workpiece, and the impact force on the tool, required to create the cutting force.
As the hardness of the material increases, the angle of sharpening of the cutting wedge should also increase, since the impact force on the tool is sufficiently large and its cross-sectional area should provide the cross-sectional area required to absorb this force. The values of this angle for different materials are approximately: cast iron and bronze 70°; medium hard steel 60°; brass, copper 45°; aluminium alloys 35°.
Rear angle a determines the amount of friction between the rear surface of the tool and the workpiece surface, its value varies from 3 to 8 The value of the rear angle is adjusted by changing the inclination of the chisel relative to the work surface.
A cross cutter (Pic. 2.21) differs from the chisel by its narrower cutting edge. Cutting grooves, cutting keyways and similar applications. In order to prevent the crosshead from jamming during operation, its working part has a gradual narrowing from the cutting edge to the handle. The heat treatment of the cutting and impact parts, the geometry of the cutting part, and the definition of the cutting angle of the cross cutter are the same as for the chisel.
Groove cutter (Fig. 2.22) is used for cutting out oil grooves in bushings and sleeves of friction bearings and profile grooves of special applications. Cutting edges of the crosshead can be either straight or semicircular in shape depending on the profile of the groove being cut. The slotting tool differs from the chisel and crosshead only in the shape of the cutting part. The requirements for heat treatment and the selection of sharpening angles for groove cutters are the same as for chisels and cross cutters.
Locksmith hammers (fig. 2.23) are used at cutting as a percussive tool for creation of cutting force and are of two types with round bottom (fig. 2.23, a) and with a square (fig. 2.23, b) striker. The opposite end of the hammer is called a sock, it is wedge-shaped and rounded on the end. The hammer is fixed on the handle, which is held in the hand while working, striking the tool (chisel, crucible, grooving tool). To keep the hammer securely on the handle and to prevent it from coming off during work, wooden or metal wedges (usually one or two wedges) are used, which are hammered into the handle (Fig. 2.23, c) where it enters the hole of the hammer.
Cutting blanks of small size (up to 150 mm) from sheet material, wide surfaces of steel and cast iron blanks of small sizes, as well as cutting grooves in bearing inserts is performed in a vise.
Cutting workpieces into parts on a slab or anvil, or contour cutting of blanks from sheet material. Grinding on the plate is applied in cases when it is impossible or difficult to fix the workpiece in a vice.
In order to give the working part of the chisel, cross cutter or groove breaker the necessary angle of sharpening, it is necessary to grind it.
Sharpening of cutting tools is made on sharpening machines (Fig. 2.24, а). Sharpening tool is installed on the undercarriage 3 and with light pressure slowly move it across the full width of the grinding wheel. During sharpening, the tool should be periodically cooled in water.
Grinding of cutting wedge surfaces is carried out alternately on one side and on the other, which ensures uniformity of grinding and obtaining the correct angle of sharpening of the working part of the tool. The grinding wheel must be covered with a cover during the sharpening operation 2. Protect the eyes against abrasive dust by means of a safety screen 1 or safety glasses. Control of the angle of sharpening of the cutting tool in the process of sharpening is carried out with the help of a special template (Fig. 2.24, б).
Handbook on metalwork “Metal Cutting
Please note that, in accordance with Federal Law N 273-FZ “On Education in the Russian Federation” in organizations carrying out educational activities, training and education of students with disabilities is organized as a joint with other students, and in separate classes or groups.
“Relevance of Creating School Reconciliation/Mediation Services in Educational Organizations”
A certificate and a training discount for each participant
“Alchevsk Metallurgical College
for educational practice of students in the profession “Locomotive engineer”
Developed by: foreman Reviewed and approved by the
Metal chopping is a metalworking operation in which layers of metal are removed from a metal workpiece or the workpiece is chopped into parts.
Metal chopping is used to divide the workpiece into parts, remove excess metal, cut grooves, grooves, etc. Metal chopping is performed with a chisel or crossbow and a hammer.
Fig. 2. Chisel: 1. head; 2. impact part; 3. spindle; 4. spindle bar. working part; 5. cutting edge.
Chisel is a steel rod with a wedge-shaped cutting edge The angle of the chisel tip when chopping steel blanks should be 60°, and when chopping non-ferrous metals it should be 35°. 45°.
Stand upright when chopping workpieces and slightly turn the body relative to the vice. The right shoulder should be in front of the chisel head. The chisel is held so that the striking part protrudes from the hand of the left hand by 15. 30 mm
Fig. 3. Methods of metal chopping in a vice: a. wrist strike; 6. elbow strike: c. shoulder strike.
Depending on the hardness and thickness of the workpiece, the force of the hammer blow on the chisel must be different. Brush blow are used for removing small irregularities and thin shavings. The hammer is moved by the movement of the hand (fig. 3, а). In the elbow strike Arm is bent at the elbow and the impact is stronger (fig. 3, б). It cuts off the excess metal and separates the workpiece into parts. Shoulder strike is used for cutting thick chips, breaking bars and strips of great thickness (fig. 3, в).
When facing in a vice, clamp the workpiece so that the indexing rib is 1.5 cm below the level of the jaws. 2 mm.
In this case there is an edge filing allowance on the workpiece after machining.
The cutting edge of the chisel is set on the surface of the jaws at an angle of 30. 40° to the cutting plane the angle of the chisel to the edges of the jaws must be 45°. 60°.
When cutting on the plate, the chisel is set vertically on the scribing ridge and the blows are delivered. After the first blow the chisel is set so that half of its cutting edge was in the already cut through the hole, and half. on the marking notch, and make the second blow. When moving the chisel along the scribing notch, it is easier to get it in the right position and obtain a continuous cut.
Fig. 4. Position of the chisel when cutting in a vice: 1. vice; 2. jaws; 3. workpiece; 4. chisel.
If the thickness of the workpiece does not exceed 2 mm, the metal is cut on one side, while the other side is placed a plate of soft steel, so as not to blunt the chisel against the plate.
If the thickness of the workpiece is large, the scribing marks must be applied on both sides. First cut through the sheet on one side, about half its thickness. Then turn it over and cut it completely.
When cutting complicated shapes from sheet metal, first at a distance of 1 m on one side and then at a distance of about half its thickness. 2 mm from the marking lines, a shallow groove is cut with light strokes on the chisel. Then, using powerful elbow thrusts, chop the workpiece along the marked groove until the outline to be chopped is marked on the opposite side. After that the sheet is turned over and the final cut of the blank is made.
Locksmith tools are sharpened on sharpening machines with abrasive wheels.
Fig. 5. Sharpening a chisel on the sharpening machine: a. methods of holding the chisel when sharpening, b. template to check the correct angle of sharpening.
At enterprises, cutting is performed by locksmiths using pneumatic and electric hammers.
Sheet metal workpieces are cut by die cutters on presses and special dies. Use plasma and laser cutting for high-strength steels.
Regulations for safe working and occupational safety.
Wear protective goggles and wear a face shield when cutting.
Clamp the workpiece securely in a vice.
Work only with tools that are in good condition (no burrs, cracks, dents, etc.).